はじめに
ダイヤモンド・ライク・カーボン膜(DLC)は現在多くの部品およびコンポーネンツの機械的特性,摩擦やトライボロジー性能の向上のために最も頻繁に使用されるコーティングの1つとなっている*1,*2.DLCはアモルファスカーボン構造を持っている複数種類のコーティングまたはフィルムを含む.DLCの主な種類は下記になる.
- アモルファス・カーボン(一般的にa-Cと呼ばれる)
- テトラヘドラル・アモルファス・カーボン(ta-C)
- 水素化テトラヘドラル・アモルファス・カーボン(ta-C:H)
DLCコーティングとして,金属などの少量の添加物を含むアモルファスカーボン膜も含まれている.DLCコーティングは,通常,物理蒸着(PVD)または化学蒸着(CVD)のいずれかによって,場合によってはプラズマ強化(PECVD)によって成膜される.DLC膜の典型的な厚さは数マイクロメートルの範囲であるが,いくつかのDLC膜は数十ナノメートルほどの薄さにすることもある*3.
本稿では,DLCコーティングの機械的性質,接着性および厚さの完全な特徴評価のために,インデンテーション試験,スクラッチ試験,摩擦摩耗試験および膜厚測定の使用を要約する.
1.硬さと弾性率:インデンテーション試験
アントンパール社製テーブルトップナノインデンテーション試験機(TTX-NHT3)は,TiN,AlTiN,CrNまたはDLCのような硬質薄膜を試験するために開発された.TTX-NHT3は,研究および品質管理の目的としてDLC膜の硬度および弾性率を測るために優れたツールである.硬度および弾性率に加えて,TTX-NHT3は弾性仕事率および塑性仕事率を計算することができる.すべての結果は自動的にISO 14577標準に従って計算される.図1はTTX-NHT3を用いて金属基板上に成膜された厚さ2μmのDLCコーティングの試験で得られた押し込み荷重-押し込み深さ曲線を示す.
<TTX-NHT3での推奨測定条件>
- 圧子:ベルコビッチ圧子
- 最大荷重(Fmax):2mNから100mN
- ローディングレート:4から200mN/min
- Fmaxで保持時間:5秒
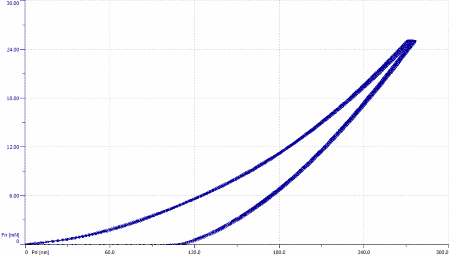
図1 厚さ2μmのDLCコーティングの一般的な押し込み荷重-押し込み深さ曲線(最大荷重25mN,ベルコビッチ圧子)
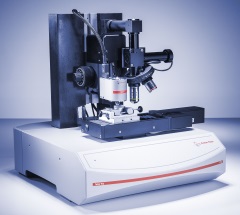
図2 アントンパールテーブル社製TTX-NHT3
インデンテーションの測定条件は,コーティングの厚さ,表面粗さおよび硬度に応じて変更しなければならない.通常,最大押し込み深さがコーティングの厚さの10%を超えない条件で測定する.同時に,最大押し込み深さが表面粗さ(Ra)よりも少なくとも20倍大きくなければならない.実際には,妥協が時々必要である.
2.コーティングの密着性:スクラッチ試験
スクラッチ技術は,コンポーネンツまた表面コーティングを持つ基板の密着性を評価するために使用されている.この方法は,硬質皮膜の密着性評価のために特別に開発されており,したがって,DLCコーティングはスクラッチ試験の主な用途の1つである.コーティングの密着性は,コーティングと基板システムの第一,第二または第三のタイプの故障に対応する垂直荷重として定義されている臨界荷重によって決定される.スクラッチ試験は品質管理と研究目的の両方に使用できる.
- アントンパール社製スクラッチテスターは,スクラッチ試験結果に同期されているパノラマ画像を記録する特許取得の機能を備えている.同期パノラマ機能は,スクラッチ痕全体の画像とスクラッチ試験中に記録された信号との同期を記録することになる.この特許取得済み機能は,試験されたサンプルはなくなった後でも異なるサンプルのスクラッチ結果を迅速かつ効率的に比較することができる.より信頼性の高い密着性分析の他に同期パノラマ機能はスクラッチ試験結果の記録保管に最適なツールもある.
- アントンパール社製スクラッチ試験機のもう1つの重要な特徴は,プレスキャンとポストスキャンの手順を経て真の押し込み深さを測定する機能である.真の押し込み深さを知ることにより,スクラッチ試験がコーティングのすべてを通過して基材まで到達したかどうか,したがって剥離が発生したかどうかを迅速に確認することができる.
以下の図3~5は,DLCコーティングのスクラッチ試験の代表的結果を示す.
<レベテストスクラッチテスタ(RST3)の推奨測定条件>
- 200μmの半径を持つダイヤモンド材ロックウェル圧子
- 連続荷重スクラッチモード(プログレッシブ)
- スクラッチ長さ2mm
- スクラッチ荷重0.5N-60N
- ローディング速度300N/min
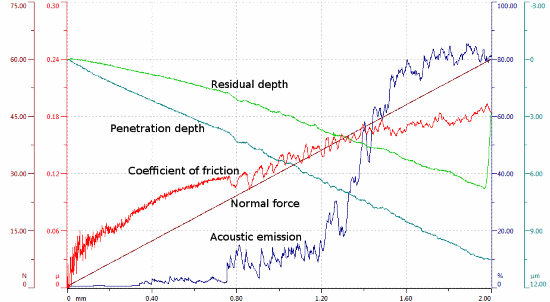
図3 一般的なスクラッチ試験で記録する信号(押し込み深さ,残留深さ,アコースティックエミッション,摩擦係数)金属上に厚さ2μmを持つDLCコーティング

図4 DLCコーティング,スクラッチのパノラマ画像
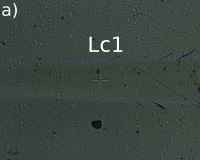
a)第一臨界負荷Lc1-サイドクラック
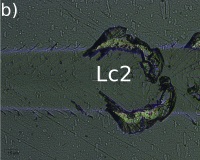
b)第二臨界荷重Lc2 - 一部剥離
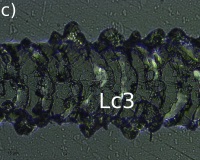
c)第三臨界負荷Lc3-完全剥離
アントンパール社製レベテストスクラッチテスターRST3はDLCや他の硬質膜の密着性評価のため200Nの最大垂直荷重が掛けられるロバストな装置である.硬質膜の密着性評価において業界標準的な装置として広く利用されているレベテストスクラッチテスターRSTの後継機種になる.
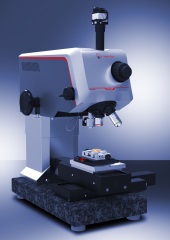
図6 硬質膜の密着性評価用顕微鏡付レベテストスクラッチテスターRST3
3.摩耗や摩擦係数:トライボロジー
ピンオンディスク型摩擦摩耗試験機などのトライボメーター試験機は,摺動接触中の2つの表面の摩擦および摩耗を評価する.摩擦係数(CoF)を知ることは,DLCコーティング生産時の品質管理,または調整された摩擦係数を備えた新しいDLCコーティングの開発にとって重要である.トライボメーターの利用により,摩擦係数は異なる条件下(荷重,環境,滑り速度,試験時間,温度など)で容易に測定ができる.耐摩耗性および摩耗量が重要である場合,トライボロジー試験で生成された摩耗痕のプロファイルをプロフィルメーター(表面粗さ計)を使用して分析できる.摩耗痕の断面積がわかれば,材料の摩耗量の算出ができる.
アントンパール社製のトライボメーターは様々な規定された条件下での摩擦特性を迅速かつ効率的に測定できる.したがって,DLCコーティングの摩擦特性を試験する際には不可欠になる.CoFと摩耗量の測定以外にも,トライボロジー実験を使用して,決められた条件下でのコーティングの寿命を測ることもできる.膜が破損した瞬間とその後にボールと接触する相手がDLCコーティング膜から基板材に変わる.対応する変化は,記録されたCoF対時間(距離)曲線で評価できる.図7に金属基板上に成膜された膜厚3μmのDLCコーティングの摩擦摩耗試験の例を示す.推奨される測定条件は下記になる.
- トライボメーター(TRB)
- 回転または往復モードでのスライディング方法
- 線速度10cm/sec
- 垂直荷重5N
- 測定距離1000m

図7 金属基板上に膜厚3μmのDLCコーティングの事例.測定条件は,直線往復モードで450℃の加熱ステージを用いて340℃で行った
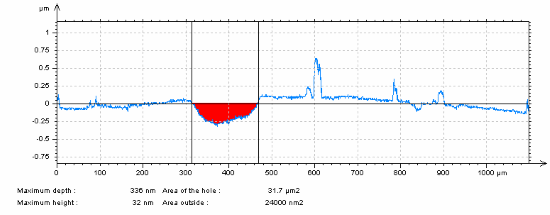
図8 300℃での摩擦摩耗試験後の摩耗痕のプロファイル
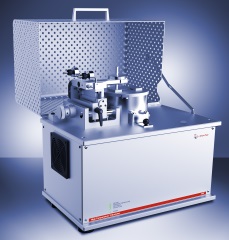
図9 回転モードのアントンパール社製トライボメーター希望の測定条件に合わせて直線往復モードに簡単に変更できる
4.膜厚:カロテスト測定
多くのコーティングでは,最終用途に致命的な影響を与える可能性があるため,膜厚は慎重に考慮する必要がある.DLCコーティングも例外ではなく,より大きな厚さによって膜内の残留応力が高くなり,膜の剥離につながる可能性がある.そのため,膜厚の管理が重要になる.
アントンパール社製カロテストは,クレータを作成するために,ボールを回転させてコーティング表面を摩耗させる.摩耗後のクレータの大きさから膜厚の計算ができる.単純であるが非常に効率的な測定方法である.
図10は,鋼基材上に成膜したDLCコーティングのクレータの一例を示す.クレータは,400rpmで15秒間,直径40mmの鋼球を使用して作成した.コーティングの平均厚さは,3回の測定の後に自動的に計算した.
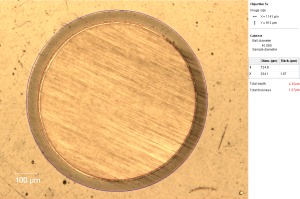
図10 鋼基板上の厚さ1μmのDLCコーティングのカロテスト試験後のクレータ
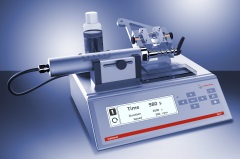
図11 アントンパール社製カロテストは,コーティング膜厚測定のためのコンパクトでありながら非常に効率的なツールである
これらの4つの測定方法により,DLCコーティングは,品質管理または開発プロセス中において機械的評価が可能となる.
<参考文献>
*1 S.V. Hainsworth, N.J. Uhure:Diamond like carbon coatings for tribology: production techniques, characterisation methods and applications, Int. Mater. Rev. 52(2007)153–174. doi:10.1179/174328007X160272.
*2 G. Dearnaley, J.H. Arps:Biomedical applications of diamond-like carbon (DLC) coatings: A review, Surf. Coat. Technol. 200(2005)2518–2524.
*3 S. Miyake, W. Kurosaka, K. Oshimoto:Nanometre scale mechanical properties of extremely thin diamond-like carbon films, Tribol. - Mater. Surf. Interfaces., 3(2009)158–164. doi:10.1179/175158309X12586382418535.