はじめに
高面圧,低速,低粘度のような境界潤滑条件下においては基材同士が接触し,その真実接触部では,凝着摩耗やアブレシブ摩耗が生じ,結果として焼付きや摩擦係数の上昇を引き起こす.このような過酷な条件下の摩擦に対するソリューションとして,極圧剤,摩耗防止剤等の潤滑油添加剤が適用されることが一般的であるが,いずれも摺動基材同士の直接接触を防ぐことが機能のポイントである.近年,各種ナノカーボン材料(フラーレン,グラフェン,カーボンナノチューブ)が固体接触を抑制し,摩擦を下げることが可能ということで,潤滑油添加剤として応用する試みがなされている.ダイセルではナノカーボン材料の一つであるナノダイヤモンド(ND)の潤滑油添加剤としての応用開発を進めており,実用化に向け,技術開発およびマーケティング活動を鋭意推進している.
1.ナノダイヤモンドに関する取り組み
一般的に,ダイヤモンドは地球上で最も高い硬度,高い化学的安定性,ワイドギャップ半導体としての電気特性,高熱伝導率,高屈折率を持つことで知られている.工業的には高温高圧法(HPHT)と化学気相蒸着法(CVD)法による製造方法が知られており,特にその硬度を生かして工業用ダイヤモンドは研磨剤や切削工具向けに幅広く使われている.
一方,ナノダイヤモンドは従来の工業用ダイヤモンドとは異なる特徴,性質を有する.ナノダイヤモンドの一次粒子径は4~6nm程度であり,最も小さなダイヤモンド粒子である.ナノ粒子であることから,わずか1μgでもその粒子数は4兆個にも上る.また,比表面積が300m2/gを超えるため,サイズ効果や個数の効果による新たな機能発現が期待される.一般的にナノダイヤモンドは爆薬を密閉容器内で爆発させることで得られる方法(爆ごう法)*1とHPHT法から合成されたバルクナノダイヤモンドを機械的に砕解する方法*2で得られ,その製法でダイヤモンド構造と性状が異なることが知られている.ダイセルが開発を進めているのは前者の爆ごう法ナノダイヤモンドであり,その表面に高密度酸素官能基が存在し,その官能基を足場にした表面修飾など化学的なアプローチが可能であることを特徴としている.
ダイセルはエアバッグ用のインフレーター(ガス発生装置)などの火工品事業で培ってきた火薬工学技術と,有機合成事業を軸にした化学処理・表面修飾技術を組み合わせてナノダイヤモンド事業の創出を目指している.事業化に向けて播磨工場(兵庫県たつの市)に爆ごう試験設備を設置し,2014年に試験製造を開始した.続いて爆ごうにより得られる煤を精製,分散してナノダイヤモンド分散液を得る精製プロセスのパイロット設備を新井工場(新潟県妙高市)に設置しナノダイヤモンドを安定に製造,供給する体制を整えた.
ダイセル製ナノダイヤモンドは幅広い分散溶媒ラインナップを揃えたDINNOVARE™(ディノベア)(図1)ブランドとして世界的にプロモーションを開始しており,大学や研究機関の研究者を中心にサンプルワークを行っている.本稿では爆ごう法ナノダイヤモンドの概要と有力なアプリケーションの一つである潤滑油添加剤としての機能を紹介する.
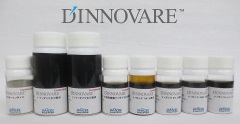
図1 ダイセル製ナノダイヤモンド「DINNOVARE(TM)」(ディノベア)
2.爆ごう法ナノダイヤモンドの概要,特徴,製造プロセス
ナノダイヤモンドは密閉状態の金属タンク内で爆薬を爆発させる方法「爆ごう法」により製造される.原料には酸素バランスが負となる混合爆薬を使用する.一般的な火薬であるトリニトロトルエン(TNT)とトリメチレントリニトロアミン(RDX:Research Department Explosive)の混合物が使用され,不活性ガスや水を充填した密閉タンク中で爆発させる.この爆発時に衝撃波が生成し,3000K・20GPa以上という高温高圧状態が維持され,爆薬に由来する炭素はプラズマ状態になり,ダイヤモンドの結晶核が発生し,ダイヤモンド結晶(図2)が成長する.
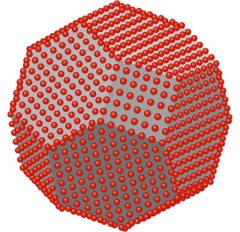
図2 ナノダイヤモンドのグラフィックイメージ
そして次に断熱膨張により冷却,圧力低下が起こり,グラファイト構造が安定な領域となるため,ダイヤモンドの結晶成長は止まり,周囲にグラファイト化した炭素が析出する.この工程は爆ごうが進む極めてわずかな時間で起こっており,時間軸は1マイクロ秒以下である.このためにナノダイヤモンドの平均一次粒子径は4~6nmとなり,サイズに分布はあるものの爆ごう条件の違いによる平均一次粒子径には大きな違いは生じない.爆ごう後に得られる生成物は,グラファイト炭素がダイヤモンド構造の周囲を覆うものとなっているため,グラファイト分を選択的に除去するために酸化処理が施される.酸化方法としては硝酸,過マンガン酸塩,過塩素酸などによる液相酸化,または空気(酸素),オゾンによる気相酸化が用いられる*3.透過型電子顕微鏡像(TEM)からは一次粒子の内部にダイヤモンドの結晶格子が観察され,その輪郭を覆うように,または上に曲線を描くようにアモルファスやsp2炭素の層が見られる(図3).
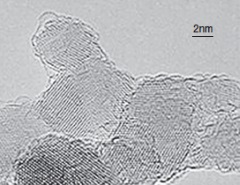
図3 ナノダイヤモンドのTEM画像
上述した酸化処理によってグラファイト分の多くは二酸化炭素にまで酸化され系外に排出されるが,このときにナノダイヤモンドの表面が酸化を受け,酸素官能基(カルボニル基や水酸基)が生成する(図4).酸化処理された爆ごう法ナノダイヤモンドは,表面に多くの酸素官能基を有し,水や極性溶媒への親和性が高いという特徴を持ち,分散剤を使うことなくpH調製とビーズミリングによる機械的解砕で一桁ナノスケール水分散液を得られる.その表面のごく短い置換基の効果により水中に自己分散する現象は,表面に高密度な酸素官能基を有するナノダイヤモンドのユニークな特徴であると考えている*4.
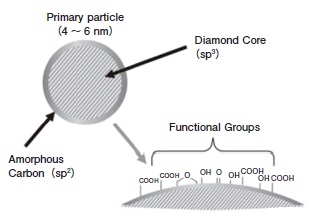
図4 ナノダイヤモンドの構造
ダイセルでは,ナノダイヤモンド表面に存在する官能基を基点に様々な置換基を導入することで潤滑油のような低,非極性溶媒にも分散可能なナノダイヤモンド粒子の開発に成功している.
3.潤滑油添加剤としての応用と効果
ナノダイヤモンドの潤滑特性評価においては,ボールオンディスク摩擦試験機(ブルカー社製UMT-3)を用いて摩擦摩耗試験を行った.試験片の材質はSUJ-2を使用,ボール(直径4mm)およびディスク(直径30mm,厚さ4mm)はともに鏡面加工品を使用した.基油はポリオールエステル(以下,POE)とし,表面修飾ナノダイヤモンドをPOEにナノ分散させて潤滑油とした.なお,ナノダイヤモンドの固形分濃度は,0.001wt%とした.摩擦試験条件は,境界・混合潤滑での評価となるように,すべり速度(1~150mm/s)と平均荷重(0.5~10N)を適宜組み合わせて条件を設定した.条件を表1に示す.軸受特性数の算出の際は,平均荷重FNと30℃におけるPOEの粘度を用いた.試験後のトライボ皮膜を把握するために,ディスク試験片の摩耗痕の詳細分析を行った.分析は,XPSを用いて,皮膜部をスパッタすることにより深さ方向での解析を行った.
表1 ナノダイヤ特性評価時の摩擦試験条件
|
POEのみ,およびナノダイヤモンド配合POEで摩擦試験した結果を図5に示す.なお,各プロットは,摩擦係数が安定したすべり終盤の1-10mにおける摩擦係数の平均値を平均摩擦係数として用いた.10Nの荷重をかけて試験を行った条件(図5の左の4点)は,いずれもPOEのみの摩擦係数0.15に対して,ナノダイヤモンド配合POEは0.1~0.13となり,境界潤滑領域において顕著に摩擦係数が低下した.図6には,試験後のディスク上の摩耗痕の光学顕微鏡の写真を示した.それぞれ,画像の左から右に向けて軸受特性数が低い条件となる.ナノダイヤモンド配合POEは,いずれの条件において摩耗痕幅がPOEのみと比べて狭くなっており,摩耗抑制効果を発現した.
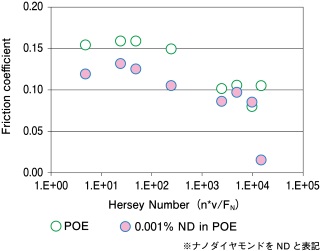
図5 境界潤滑域の軸受特性数
次に,摩耗痕上に形成されたトライボ皮膜のXPS分析によって得られた元素分析結果を図7に示す.Oの濃度が5at%で安定したところを皮膜最深部とし,皮膜の厚みを判定した.その結果,POEのみの場合は約90nm,ナノダイヤモンド配合の場合は約130nmとなり,ND配合により酸化皮膜の厚みがPOEのみと比べて1.5倍に上昇していた.この酸化皮膜の膜厚上昇が摩耗抑制効果発現の一要因であると推測している.
図8に,すべり速度50mm/s,平均荷重10Nにおける,800m摩擦試験後のボール側の摩耗量を示す.ナノダイヤモンド配合POEでの試験ではボール摩耗量が93%低減しており,顕著な摩耗防止効果が確認された.荷重10Nのボール接点は面圧に換算すると,1GPaにも達する極めて高い面圧条件であり,境界潤滑下での機能が期待される.
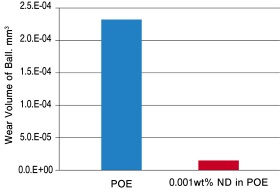
図8 ボール摩耗量の比較
まとめ
1GPaを超えるような境界潤滑領域において,ナノダイヤモンドを分散した系では,摩擦係数を約30%低下,摩耗量は約90%低下させることができた.
ナノダイヤモンド添加剤を活用することで,従来の摩耗防止剤では対応が困難であったような過酷な摩擦条件下での摩耗抑制が期待でき,添加剤として産業応用が期待される.今後はナノダイヤモンドによる摩耗抑制効果,低摩擦発現のメカニズムを解明し,ナノダイヤモンド粒子設計にフィードバックすることで,更なる機能向上を図る.
※ダイセルでは,DINNOVARE™のサンプルを提供しており,同社ホームページから申し込みができます.
DINNOVARE™のサンプルはこちらから
謝辞
ナノダイヤモンドのTEM画像をご提供いただいた信州大学工学部 林卓哉教授に厚く御礼申し上げます.
<参考文献>
*1 V.N. Mochalin, O. Shenderova, D. Ho and Y. Gogoti, Nature Nanotechnology, 7, 11(2012)
*2 Boudou, J. P., Curmi, P. A., Jelezko, F., Wrachtrup, J., Aubert, P., Sennour, M., Balasubramanian, G., Reuter, R., Thorel, A., Gaffet, E., Nanotechnology, 20(2009)235602
*3 S. Osswald:“Nanodiamond Pufirifation”, Nanodiamond. O. A. Williams, ed. Royal ociety of Chemistry(2014)89-111
*4 A. Krueger et al. phys. stat. sol. (a) 204, 9(2007)2881-2887