はじめに
近年,非破壊検査の役割は大きく変化し,品質管理の一部を担うだけでなく,独立した第三者性を要求され,社会的に責任ある評価を受けるようになってきた。
また,非破壊検査業界の位置付けは,航空機や原子力施設をはじめ公共・民間の施設や設備などの健全性を調査することにより,社会の安全と安心の確保を構築する役目を果たしている。品質の高いモノを作るには相当の非破壊検査が必要である。
本稿では,非破壊検査の概要と種類,適用範囲をご紹介する。
1. 非破壊検査とは
非破壊検査とは,モノを壊さずに検査対象物にあるきずを探すことであり,大きく分けて,1)表面きずの探傷,2)内部きずの探傷,と「検査対象物の状態」を把握することである。
1)表面きずの探傷
(1)目視検査
表面の状態やきずを調べる(材料,機器,構造物などに適用)
(2)磁粉探傷検査
表面または表面直下のきずを検出(磁石に吸引される強磁性体に適用)
(3)浸透探傷検査
目に見えない表面のきずを検出(金属,非金属,溶接部に適用)
(4)渦流探傷検査
小さなパイプなどのきずを検出し,材質判別に適用(導電性のものに適用)
2)内部きずの探傷
(1)放射線透過検査
エックス線やガンマ線を利用して内部のきずを検出(金属,非金属,溶接部に適用)
(2)超音波探傷検査
超音波の反射を利用して内部のきずを検出(金属,非金属,溶接部に適用)
2. 磁粉探傷検査(Magnetic Particle Testig)
鉄,ニッケル,コバルトおよびその合金などのように磁石に強く引き付けられる物質を強磁性体という。この強磁性体の試験品に磁界を作用させると,試験品は磁化されて内部に磁束を生じる。試験品の表面および表面直下に磁束を遮るようなきずがあると,その部分で磁束が空間に漏洩してきずの両側にN,S極の磁極が発生する。この時に試験面に磁粉(鉄製の微粉末)を散布すると,きずの磁極部分に磁粉が吸着され,磁粉模様を形成する。きず部に吸着された磁粉模様は,実際のきずの幅に比べ,数倍~数十倍の大きさに拡大されるため,容易にきずの存在を知ることができるようになる。
磁粉探傷検査の特性としては,以下の5点が挙げられる。
(1)試験体表面近くに存在する割れのようなきずの検出に最も優れた非破壊検査方法である
(2)きずが表面に開口していなくても,表面から2~3mm程度の深さまでに存在するものであれば,検出が可能である
(3)きずが開口していて,きずの内部が油や水で満たされていても検出が可能である
(4)試験品表面に塗料やメッキなどの表面処理がされていても,0.1mm程度の塗膜厚さであれば,そのままで検出することも可能である
(5)試験面上でのきずの位置,形状および大きさはほぼ正確に分かる
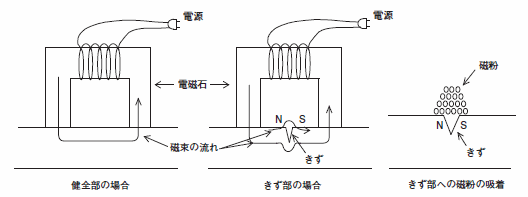
図1 磁粉探傷検査の一例
利用分野と適用限界
磁粉探傷試験は表面および表層部のきずの検出に適しており,鉄鋼製品の溶接部や素材の製造時検査および保守検査に用いられている。特に疲労割れなどの微細な割れの検出能力が高いため,保守検査で威力を発揮している。しかしながら,強磁性体の試験品にしか適用できないことや,磁束の流れる方向に直交するようなきずでないと検出できないため,同一箇所について相直交する2方向から磁化する必要があること,さらに,きずの検出能力を上げるため磁粉の中に蛍光剤を入れた蛍光磁粉を使用することが多く,この場合には作業場周辺を20ルクス以下の暗さにしなければならないなどの制約がある。
試験品の形状によっては試験品に直接大電流を流すこともあり,電極接触部分でのスパーク(火花)の発生に対する配慮や,試験体表面の凹凸・隅角部・ネジ部などでも磁束が空間に漏洩することにより,あたかもきずが存在するような磁粉模様を形成することがあるので,観察においても十分な注意が必要となる。
3. 浸透探傷検査(Liquid Panetrant Testig)
浸透探傷検査は試験体表面に開口している微細なきずの中に液体(浸透液)を浸み込ませ,次にこの浸み込んだ液体を表面に吸い出すと同時に表面に拡がらせ,液体の大きなにじみ模様としてきずを検出する方法で,液体の毛細管現象とぬれの現象を利用している。
浸透探傷検査の特性としては,以下の4点が挙げられる。
(1)金属,非金属を問わず探傷することができる
(2)1回の探傷操作で試験品全体を探傷することができ,またきずの方向に関係なくきずが検出できる
(3)特別な装置を必要としない携帯性に富んだものである
(4)比較的に取り扱いが簡単である
【浸透探傷の手順】
浸透探傷検査は,以下の5つの基本処理から成り立っている(図2)。
(1)前処理
きずの中の異物を取り去り,きずの中を空洞にする。
(2)浸透処理
試験品の表面を浸透液でぬらし,きずの中に浸透液を浸み込ませる。
(3)除去処理
きずの中へ浸み込んだ浸透液はそのままにし,試験品の表面の余剰浸透液だけを除去する。
(4)現像処理
きずの中の浸透液を試験品の表面に吸い出して指示模様が形成される。
(5)観察
検出した指示模様を観察し,きずかどうかの判別やきずの位置形状,大きさなどを調べる。

図2 浸透探傷検査の手順
利用分野と適用限界
浸透探傷試験は磁粉探傷試験と同様に表面きずの検出に適しており,鉄鋼材料に限らずアルミニウムやステンレス鋼でつくられた鋳造品や鍛造品などの小物量産部品や溶接部の製造時検査および保守検査に広く用いられており,最近ではセラミックスのような部品にも使われている。
木材やコンクリートのような多孔質な材料のものは試験品表面全体に浸透液が浸み込んでしまい,きずと健全部との区別がつかなくなるため適用ができないが,それ以外の材質のものは表面粗さが著しく悪くなければ何に対しても適用が可能である。ただし,浸透液をはじめ他の探傷剤によって変形,変質してしまう材料には使用できず,特に合成樹脂などに対しては試験前に探傷剤に侵されるかどうか確認する方が良い。
浸透探傷試験は浸透液をきずの中に浸透させるため,表面に開口しているきずしか検出できず,また開口していても傷口がさびや塗料でふさがっていたり,きずの中に油脂類や水が詰まっていると検出は不可能である。試験結果としては,きずの有無と試験品表面におけるきずの形状しか分からず,きずの深さやきずの内部形状は分からない。
4. 渦流探傷検査(Eddy Current Testig)
金属などの導電体に交流電流を流したコイルを近づけると,その導電体にうず電流(渦流)が発生する。この現象を電磁誘導といい,発生するうず電流の変化を測定して材料の試験を行う方法を渦流探傷検査または電磁誘導検査という。
うず電流の変化は導電体(試験体)の導電率,透磁率などの材質や形状寸法およびきずの存在またはコイルと試験体との距離に影響され,これらの変化はそれぞれ試験の指示として現れるので,きずの検出を目的とする探傷試験だけでなく材質試験,膜厚測定,寸法・形状検査など多くの分野に適用されている。
渦流探傷検査の特性としては,以下の5点が挙げられる。
(1)コイルが試験体と接触する必要がない
(2)管,線,丸棒などに対する探傷試験の高速化,自動化が容易である
(3)表面きずの検出に適している
(4)高温の試験体や細線,穴の内部など人間が接近できない部分の探傷ができる
(5)検査結果のデータの記録・保存が容易であり,保守検査に役立てることができる
貫通コイルによる探傷
内挿コイルによる探傷
利用分野と適用限界
渦流探傷検査は,交流電流による電磁誘導現象を利用する性質上,導電性のある試験体の表面および表層部のきずの検出に適しており,発電所や化学プラントなどにおける熱交換器や復水器などのチューブ(細管)の製造時検査および保守検査に適用されている。
また,前述のとおり材質試験,膜厚測定も可能であり,それぞれハンディータイプの測定器が市販されている。材質試験では金属材料の種類,合金成分の判別や熱処理状態,硬さなどの判別に利用されており,膜厚測定ではメッキ,塗装,プラスチックなどの被膜厚さ測定に利用されているが,材料の電磁気的性質の差異によっては判別や測定が困難な場合もある。
うず電流に影響を与える因子が多いということは,探傷試験の場合にはきず以外の因子がノイズを発生させ,きずの判別を困難にすることにもなり,凹凸があったり,複雑な製品や溶接部などの検査においては慎重な操作が要求される。
直管部と曲管部の探傷においては,直管部の場合,試験コイルと管とのすき間を一定に保つことができるので操作は簡単であるが,曲管部の場合はこのすき間を一定に保つことが困難であるため,コイルの移送を緩めたりコイル形状を変えなければならないなど,操作がかなり複雑となる。
さらに鋼のような磁性体の探傷においては透磁率が不均一であるため,大きなノイズが発生し,探傷不能となることが多い。この場合には試験体を強く磁化して磁気飽和させると透磁率の不均一が小さくなりノイズを抑制することができるが,装置が大型となり脱磁処理も必要となってくる。
特に近年,磁性体配管の保守検査法として従来法とは少し異なったリモートフィールド渦流探傷試験が試みられるようになってきたが,検出感度や検査速度が劣るなどの問題点を認識しておく必要がある。
5. 放射線透過検査(Radiographic Testig)
放射線透過検査は,エックス線やガンマ線の放射線が試験体を透過する現象および写真フィルムを感光させる現象を利用して,試験体内部の状態を2次元的撮影像としてフィルムに記録させる方法である。放射線が試験体内を透過する際,内部にきずがあると,健全部と比べて多くの放射線が透過し,エックス線フィルムをより強く感光させ,写真現像するとそのきず部分は健全部よりも黒く写る。このフィルムを観察することにより,試験体内部のきずを検出することができる。
エックス線とガンマ線は同じ種類の放射線で,エックス線はエックス線管内で電気的に制御して発生させる電磁波であり,ガンマ線は放射性物質の原子核内部から放射される電磁波でその性質は全く同じである。エックス線とガンマ線との使い分けは,エックス線装置は電源を切ればエックス線は発生せず安全管理面で比較的楽であるが,装置が大型となり狭い場所では使用が困難となる。ガンマ線源は常に放射線を出し続けているため,安全に対する維持管理が厳しいが,装置が小型で狭い場所でも使用が可能である。
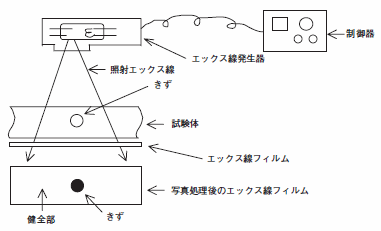
図4 エックス線撮影配置の一例
放射線透過検査の特性としては,以下の4点が挙げられる。
(1)試験体内部の状態が2次元的にフィルム上に写されるので,きずの種類,形状,寸法が視覚的にとらえやすい
(2)2次元投影像であるので,1枚のフィルムでは厚さ方向の寸法は判別が困難であるが,照射方向を変えて複数枚のフィルムを使うことによって判別が可能となる
(3)試験の結果をフィルムとして記録することができ,いつでも見直すことができる
(4)試験体の適用厚さの下限値の制限はなく,どんな薄いものでも撮影可能である
利用分野と適用限界
放射線透過試験は,内部きずの検出に適しており,主に圧力容器,船舶,橋梁,パイプラインなどの金属構造物の溶接部や鋳造品の検査に広く用いられているが,近年では食品,木材,文化財,セラミックスやコンクリート等の非金属材料に対する内部状況の調査にも頻繁に用いられるようになった。この試験ではエックス線の透過能力に限度があるために,試験体の厚さの上限について制限され,据置式装置の場合,検査可能な厚さの限界は鉄鋼材料で約300mmである。現場撮影に使用する可搬式の装置であればさらに薄くなり,鉄鋼で約60mm,コンクリートでは約450mmが限界となる。透過厚さが厚くなるほど装置も大型のものが必要となり,装置の配置時間および照射時間が長くなる。
また,透過法であるので試験体を挟んで放射線源とエックス線フィルムをそれぞれ反対の位置に配置する必要があり,透過厚さは薄くても片側だけにしか近づけない場合,撮影は不可能となる。
さらに,放射線を取り扱う際には放射線被ばくによる放射線障害についての管理が法令で詳細に定められており,撮影に関しては「エックス線作業主任者」「放射線取扱主任者」「ガンマ線透過写真撮影作業主任者」などの有資格者による取り扱いが規定されており,作業者および作業場周辺の人々に対する安全管理には細心の注意が払われている。
6. 超音波探傷検査(Ultrasonic Testig)
人間の耳で聞こえる音の周波数(20~20000Hz)よりも高い周波数の音波を超音波といい,この超音波を探触子を使って材料中に伝搬させると健全部では直進するが,きずがあるとそこで超音波の一部分が反射され,元の探触子に戻ってきて受信される。この現象(山彦の原理)を利用して,きずの存在位置や大きさの程度を知る方法が超音波探傷検査である。通常,鋼材では1~10MHzの周波数の超音波を使用し,試験体の表面から垂直に伝わらせる垂直探傷法と,入射角度を持たせて斜めに伝わらせる斜角探傷法とがあり,試験体の形状や検出したいきずの種類,方向などを考慮して使い分ける。
超音波探傷検査の特性としては,以下の7点が挙げられる。
(1)反射法を利用しているので,試験体の片側だけからの検査が可能である
(2)きずの厚さ方向の位置を正確に求めることができる
(3)検査可能な厚さの上限が大きい。場合によっては,鋼では3~5mの範囲でも検査可能であり,長さ測定においては10mでも測定可能である
(4)装置が2~6kgと小型,軽量である
(5)検査の結果がただちに得られる
(6)設備費,消耗品費などがRT(放射線透過検査)と比べると低額である
(7)超音波に対する安全管理がほとんど必要ない
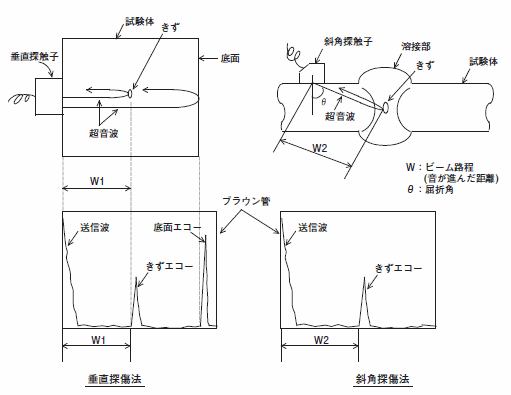
図5 探傷図形の一例
利用分野と適用限界
超音波探傷検査は放射線透過検査と同様に内部きずの検出に適しており,主に橋梁・建築鉄骨溶接部,鍛鋼品,コンクリート構造物や原子力発電所の製造時検査および保守検査に用いられている。金属材料のように内部結晶粒子が一定である場合は超音波は安定して伝搬し精度良く測定,探傷できるが,コンクリート構造物のように内部組織が一定でない場合は超音波の伝搬がスムーズでなくなり,精度が悪くなったり,探傷不可能ということも生じる。超音波探傷検査では反射して戻ってきた超音波を信号として情報化しているため,きずの種類,形状や深さ方向の寸法の特定は困難なことが多いが,近年ではコンピュータを利用した種々の探傷法も開発され,著しく改良されてきている。また,記録性に乏しく検査の信頼性も検査員の技量に大きく依存すると言われていたが,これも検査技術者資格認定制度に従って認定された有資格者による探傷やデジタル超音波探傷装置または超音波自動探傷装置を採用することにより解消されてきている。
7. その他の非破壊検査
○超音波厚さ測定
板材や構造物の厚さを測定する(金属,非金属,機器,構造物などに適用)
○ひずみ測定
構造物など表面のひずみを測定する(主に金属性の構造物)
○アコースティック・エミション検査
音響を利用して構造物の調査をする(各種材料,構造物など)
○赤外線検査
赤外線を利用して表面温度分布の測定をする(高温設備,電力設備,建築構造物のタイル剥離など)
○鉄筋検査
電磁波レーダ,電磁誘導法を利用し,鉄筋の位置や深さなどを測定する(橋脚,建物などのコンクリート構造物に適用)
おわりに
わが国で非破壊検査が1つの業種として発展したきっかけは,戦後,造船業に採用されたことだといわれている。昭和30年に初めて非破壊検査の専門会社が設立され,日本経済の発展とともに公共事業や民間の石油化学プラント,発電設備などの建設やメンテナンスを中心に広がりをみせている。
現在では,既存の設備の老朽化に伴う調査や,マンションなどの建築構造物,遊戯施設の健全性など要求が多様化している。今後はより生活に密着した分野にも幅広く拡大していくと思われる。