はじめに
自動車にはグリースで潤滑される多数の部品が使用されている。その一例を表1に示す。
表1 グリースが使用されている主な自動車部品
*:アンチロックブレーキシステム,**:排気ガス再循環装置 |
CO2排出量削減や省資源の意識の高まりから自動車の省燃費への取り組みが進んでおり,グリースを使用する自動車部品も小型軽量化や低トルク化,低摩擦化により省燃費に貢献することが求められている。
小型軽量化は部品強度の低下を招くため,グリースには安定した潤滑状態の確保・向上が期待されている。また,点検期間延長やメンテナンスフリーの観点から,自動車部品寿命の延長が求められており,使用されるグリースにも耐熱性,長寿命性などが要求されている。
さらなるCO2排出量削減が可能な自動車としてハイブリッド自動車や電気自動車が登場し,これら自動車は増加傾向にある。ハイブリッド自動車や電気自動車には電気部品や電子部品が多数使用されており,これら部品の接点部分にはグリースが使用されている。
本稿では,自動車用部品のうち,電気容量の確保を担うオルタネータをはじめとした電装部品・補機軸受用グリース,駆動系のホイール軸受用グリースおよび接点用グリースの技術動向について述べる。
1. エンジン電装部品・補機軸受用グリース
エンジンにはオルタネータ,カーエアコン用電磁クラッチ,電動ファン,アイドラプーリなど数多くの電装部品・補機が配置されており,ベルトを介してエンジンの動力により駆動される。電装部品・補機はグリースを密閉した玉軸受が主に使用されている。
軸受の使用条件は,小型化,高出力化にともなう高速回転,高温,高負荷,エンジンの振動に加え,さらに水がかかりやすいという悪条件も加わり非常に過酷である。また,VベルトからポリVベルトへと変更となった1980年中頃からオルタネータ,電磁クラッチ,アイドラプーリなどの軸受において計算寿命よりもはるかに短い時間ではく離(早期はく離)が発生するというトラブルが散見されるようになった。この早期はく離は,通常の金属疲労によるはく離と異なり,写真1*1に示すようにはく離下部断面にランダムな白色組織変化を伴う内部起点型はく離であり,白色はく離とも呼ばれている。
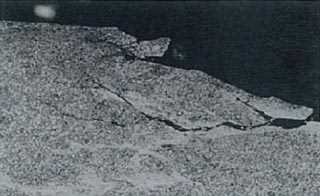
写真1 はく離下断面組織*1
白色はく離の発生メカニズムについて様々な説が提唱されてきたが,近年最も有力と考えられているのが,水素脆性説*2,*3,*4である。
水素脆性説とは次のとおりである。過大荷重,振動,急加減速などにより,転動体と内外輪間に滑りが発生し,活性な金属新生面が生成することによりトライボケミカル反応が起こり,グリース成分が分解し,水素が発生する。発生した水素が鋼中へ侵入し,ミクロ組織の変化,亀裂(水素脆化)を引き起こし,はく離に至るというものである。
グリースからの水素発生挙動はグリース成分,特に添加剤の影響が大きいことが長年の研究により分かってきた。水素発生挙動に対する添加剤の影響を明らかにするため,真空下でグリースを塗布し摺動を行って新生面を生成させ,その際に生成する成分を四重極型質量分析計を用いて評価した。図1*5に示すように,最大ヘルツ圧力960MPaにおいて,添加剤無配合のU0とスルホン酸塩配合のU2より水素および炭化水素の発生が認められたが,亜硝酸塩配合のU1では水素および炭化水素の発生は認められなかった。最大ヘルツ圧力を1200MPaまで上げると,U0,U1,U2ともに水素および炭化水素の発生が認められたが,発生量はグリースにより異なり,U1がU0およびU2より少なかった。これは,亜硝酸塩が新生面の生成を抑制した,あるいは新生面の活性を抑制した可能性が高いためと考えられる。
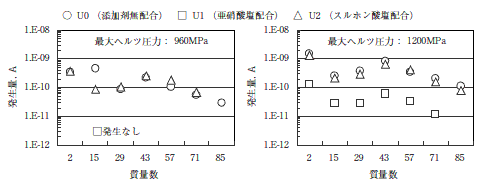
図1 質量数における発生量*5
現在では,白色はく離は十分な油膜厚さが確保でき,適切な添加剤を選定したグリースの適用によりほぼ解決されるようになった。
一方,グリースの水素発生に関し,新生面におけるトライボケミカル反応に加え,静電気の放電エネルギーの影響によるとの報告もある*6。これは,ベルトとプーリ間で発生した静電気がグリース中に帯電し,油膜切れにより金属接触した瞬間に静電気が放電し,その放電エネルギーによりグリースが分解するというものである。そこで,グリース中に帯電した静電気の除去を目的にグリースに導電性物質のナノカーボン粒子を配合した長寿命グリースが開発された。図2*7に示すように,従来グリースのL10寿命は250時間程度であるが,ナノカーボン粒子配合の長寿命グリースは3000時間でもはく離発生せず,組織変化も観察されなかった,とある。

図2 長寿命グリースの白色はく離試験結果*7
今後,最高温度は180℃を超え,最高回転数はオルタネータ用軸受では20,000min-1,カーエアコン電磁クラッチ軸受では13,000min-1を超えると言われており,白色はく離対策とともに高温高速対策も必要と考えられる。
2. ホイール軸受用グリース
乗用車用ホイール軸受は,小型・軽量・高信頼性向上とモジュール化推進の要求により,ナックルやハブなどの周辺部品を一部取り込み,ユニット化されている。これらはハブユニット軸受と呼ばれている。
ハブユニット軸受グリースには,耐漏えい性,せん断安定性,耐熱性,耐水性,さび止め性などの要求に加え,長距離輸送時の微振動によるフレッチング防止が求められている。そのため,耐フレッチング性に優れるウレア系グリースにさび止め剤などを配合したグリースが主に使用されている。
近年では,北米やシベリアなどの寒冷地における冬季の長距離輸送時にフレッチングが発生するという問題が顕在化している。低温で行ったファフナーフレッチング試験結果を図3に示す。低温未対策グリースは常温での摩耗量は少ないが,低温になると摩耗量が多くなり,耐フレッチング性能が悪化した。そこで,低温性を考慮して基油の流動点や増ちょう剤タイプの最適化を図った低温対策グリースは,低温においても摩耗量が少なく,幅広い温度領域で優れた耐フレッチング性を維持している。
図3 低温時ファフナーフレッチング試験結果(ASTM D4170 準拠:荷重550lb,揺動0.21rad,時間2h)
また,省燃費の観点からハブユニット軸受にも低トルクが求められている。軸受のトルクにはシールと予圧の寄与度が高いため,シール接触圧や予圧の低減が図られている*8。しかし,シールの接触圧低減は,水の浸入を容易にする。
一方,BRICsや発展途上国の自動車保有台数が増加しているが,それらの国々では未舗装道路が多く,道路にたまった泥水がハブユニット軸受にかかりやすいといった状況にある*9。したがって,これからのハブユニット軸受用グリースには低温時の耐フレッチング性に加えて耐水性,さび止め性の強化が課題となる。
大型トラックや大型バスのホイール軸受には,円すいころ軸受が使用されている。軸受には大きな荷重がかかり,さらに回転による自己発熱やブレーキからの伝熱などにより,多大な熱負荷がかかる。グリースにはリチウムグリースが主に使用されている。しかし,表2*10に示すように,積載量が非常に大きい状態で長距離走行すると,リチウムグリースは3ヵ月で軸受に損傷が発生した。ウレアグリースは1年間走行できたが,軸受に損傷が認められ,グリースの変色が大きく,軸受転送面のグリース残存量も少なく,油分が枯渇した状態であった。
表2 特殊大型車における1年間の実車走行試験結果*10
積載時総重量:120t,走行期間:1年,走行距離:18万km |
一方,リチウム複合グリース(リチウムコンプレックスグリースともいう)では軸受の損傷はなく,グリースの変色は少なく,また軸受内には十分なグリースが残存しており,非常に良好な状態であった。
また,ホイール軸受は車検時に点検されるが,問題なければ軸受は再利用される場合が多い。再利用する場合,グリースを入れ替えるために軸受を洗浄しなければならず,洗浄性も必要な性能である。表2のとおりリチウム複合グリースは,リチウムグリースと同様に良好な洗浄性を有している。
大型車のホイール軸受も乗用車と同様にユニット化が進むものと予想され,メンテナンスフリーに対応するためグリースには長寿命,耐熱性やせん断安定性の向上が求められると考えられる。
3. 接点用グリース
自動車には多くの電気・電子部品が使用さており,電流接点が多く存在する。この接点の摩擦・摩耗の制御を目的としてグリースが塗布されている。接点用グリースには,短絡しないための電気絶縁性と,作動時の金属接触による通電性の確保という相反する機能の両立,ならびに油膜形成による摩耗抑制が求められる。
従来,自動車の接点では比較的大きな電流が流れるものが多かったが,自動車の電子化やコスト低減から微小電流化する傾向にある。表3に接点用グリースの必要性能を示す*11。
表3 接点用グリースの必要特性*11
|
大電流接点では,その開閉時にアークが発生する場合が多い。アーク放電が起きると,接点は表面の酸化により電圧低下が起こり,グリースは炭化が進行し絶縁抵抗が変化するため,酸化亜鉛などの金属酸化物を添加したグリースが使用されている*12。
一方,微小電流接点では,通電性が最も重要となる。従来の鉱物油を基油としたグリースでは,低温になると粘度が増大し導通不良が発生する。
そこで,基油に低粘度の合成炭化水素油,増ちょう剤に汎用性の高いリチウムセッケン,さらに摩耗と腐食を抑制する添加剤で構成されたグリースが使用されている*13。
自動車の快適性を高めるため,自動車の基本機能ともいうべき「走る・曲がる・止まる」に関係する基幹部品にまで電動化が進んでいる。例えば,自動車1台あたりのモータ数は2010年に100個を,2015年には200個を超えると予測されている*14。また,電気自動車の普及も間近に迫っており,接点は増加の一途をたどっている。
おわりに
世界中のあらゆる場所で使用され,多種多様な部材から構成される自動車は,世界中の法規制(例:RoHS指令,TSCA,REACHなど)に抵触しないものが使用されていなければならず,グリースも例外でない。急激な環境・安全性への関心の高まりとともに法規制は世界的にますます多様化する。現在使用可能な添加剤が使用できなくなるなどの事態が起こり,グリースの開発に制限が課せられる可能性もある。
環境への配慮や安全性を確保しつつ,様々な要求性能や新規機構への対応など課題の多い自動車用グリースの開発に,グリースメーカの一員として今後も積極的に取り組んでいきたい。
<参考文献>
*1 池谷正道:NSK Technical Journal,677,25-31(2004)
*2 玉田健治:NTN Technical Review,61,29-35(1992)
*3 野崎誠一:NTN Technical Review,61,36-39(1992)
*4 三上英信:トライボロジスト,53,4,248-253(2008)
*5 東根泰葉:ENEOS Technical Review,51,2,53-57(2009)
*6 磯賢一:NSK Technical Journal,679,28-35(2005)
*7 磯賢一:トライボロジー会議予稿集,東京(2009)303
*8 沼田哲明:KOYO Engineering Journal,162(2002)33
*9 日本精工ホームページ参照(http://www.nsk.com)
*10 荒井孝:ENEOS Technical Review,51,2,62-66(2009)
*11 木下賢吾:潤滑経済,6,40-45(2008)
*12 岡庭隆志:月刊トライボロジー,9,30-33(2006)
*13 吉田浩之:潤滑経済,11,6-9(2005)
*14 高野:日経ものづくり,12,22-23(2006)