はじめに
工作機械は,高精度化・高速化・高効率化を中心に技術開発されてきた。主軸の高速については,セラミツク軸受とオイルエア潤滑の組み合わせで高速化が実用化されてきており,送り駆動系の高速高精度化については,ハイブリッド案内面・リニアモータ駆動による案内面も実用化されている。*1
最近の技術動向を特許出願内容からまとめると,次世代工作機械とは,(1)高精度・高効率な工作機械(高速主軸,パラレルメカニズム,リニアモータ駆動,複合加工),(2)環境対応工作機械,(3)精密加工が可能な工作機械となる。*2
ところで,工作機械を支える周辺技術の一つに潤滑技術がある。工作機械の機能を100%発揮させるために,適切な潤滑油を選定し,管理することは極めて重要である。当社は,潤滑油供給メーカーとして機械工場の潤滑管理の実態を調査し,潤滑トラブルを低減する手法や潤滑剤の開発を進めてきた。
そこで本稿では,機械工場の潤滑管理の実態および省資源・省エネに寄与する潤滑技術について紹介する。
1. 機械工場の潤滑管理の実態
1.1 潤滑管理の進め方

図1 潤滑管理の推進フロー
潤滑管理は,図1に示すように進める。潤滑管理を進める上で最も大切なことは,現状の潤滑管理の実態を正確に把握することである。機械加工現場での問題点を明らかにし,その問題を解決するための活動計画を立案・実行する。また,活動の効果を定期的に確認し,活動計画に反映することが肝要である。活動を継続するために,「潤滑管理要領書」などにより,標準化して定着させる。
1.2 潤滑管理の実態調査
潤滑上の問題点を抽出するために,例えば表1に示す項目を最低限点検し,潤滑管理の実態を明らかにする。我々が機械工場で調査診断した実例を図2に示す。
表1 潤滑管理状況調査点検項目
|
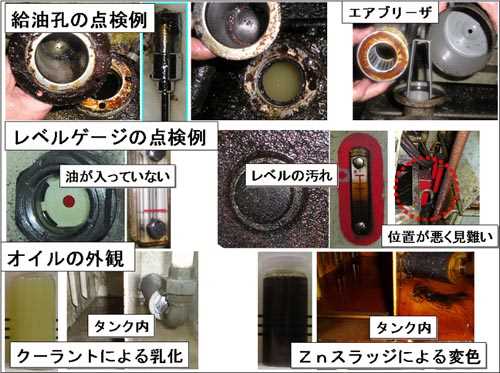
図2 潤滑管理の実態調査
給油孔には異物の混入を防止するストレーナが設置されているが,ストレーナの中は異物が多量に入っているものがある。また,ストレーナが破れているものもある。これらの油タンクの底をマグネット棒でさらうと,マグネット棒の先端に金属粉やスラッジが付着する。油はきれいだが,タンク底が汚れている。
レベルゲージは,汚れて見えないものや設置位置が悪く,レベルが確認できないものがある。また,オイルが入っていないものやレベルが下限以下のものもある。特にエアーオイラは,オイルが入っていないものが散見される。
図2の下段は,サンプリングしたオイルの外観である。クーラントが混入し,乳化したオイルや茶褐色に変色したオイルがある。機械加工現場では,水溶性クーラントが多く使用されており,クーラントが作動油タンクに混入する。クーラントが作動油タンクに混入すると,クーラントの成分は油に溶けないので粘着性のスラッジを生成する。このスラッジは,電磁バルブを固着させるなどのトラブルを発生させる。
油温の高い油圧装置にZn系作動油を使用すると作動油は茶褐色に変色する。Zn系作動油に使用しているZnDTPは,高温で分解してスラッジが発生する。このZnスラッジがタンク壁面やストレーナに付着する。このZnスラッジも潤滑トラブルを発生させる要因になる。
図3は,5Sの実施されていない設備や油漏れのある設備の事例である。制御盤の通気窓にオイルミストが付着して,ベトベトに汚れているものやモーターカバーが切粉や油ミストで閉塞しているものもある。

図3 自主保全活動の低下
油漏れのある設備が多く,油漏れが放置されている。油が飛散した機械設備の油漏れ個所を肉眼で確認するのは困難である。油漏れ個所の確認は,図3の下段に示すように作動油に蛍光剤を添加して紫外線ランプによって確認する方法が効果的である。
生産が優先される機械工場では,潤滑管理が十分になされておらず,問題が山積している。以前は,TPMの一貫として潤滑管理を推進していた機械工場も,保全経費の削減や保全担当者の減員により,機械を修理するだけで手一杯というのが実態である。
2. 攻めの潤滑管理による経済効果
2.1 潤滑管理のステップ
潤滑管理の推進は,ステップ別に次のように考えることができる。
STEP 1:初期の潤滑管理である
適正な潤滑油を適切な時期に適量供給して,潤滑状態を最適にする。
STEP 2:潤滑診断を行う
潤滑診断によって,機械の異常を早期に発見し,トラブルを未然に防止する。
STEP 3:潤滑改善を行う
設備の不具合個所,劣化個所について,潤滑改善を実施し,潤滑トラブルを低減する。
2.2 潤滑改善と効果
機械が故障している要因が潤滑に起因している場合は,潤滑改善を実施し,要因を排除する。もし機械設備に不具合があれば,潤滑技術を活用した設備改造を行う。
図4の事例は,工作機械の油圧装置において,油圧ポンプのトラブルが頻発している事例である。故障の主な原因は,油圧と減速装置の潤滑油系統が同一であるために,減速装置で汚染された潤滑油が油圧装置に供給されるためである。
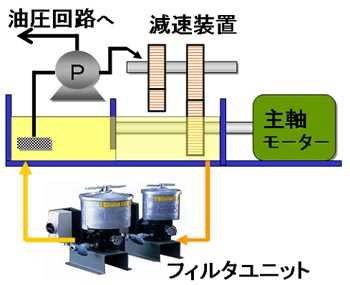
図4 設備の不具合トラブル対策
この機械は,潤滑設計に問題のある設備であり,油圧と減速機の潤滑系統を別々にする必要がある。しかし,設備改造が難しいことから,暫定処置としてバイパスフィルターによる潤滑油の浄油を実施した。この浄油(潤滑改善)を実施することにより,潤滑トラブルが1/6に低減された。表2は,浄油(潤滑改善)による効果を試算したものである。潤滑管理(潤滑改善)の効果は,潤滑改善実施前後によるトラブル低減効果をコスト比較すると実感できる。従来,潤滑管理はSTEP 1(初期の潤滑管理)とSTEP 2(潤滑診断)を実施し,トラブルを未然に防ぐという考え方であったが,STEP 3(潤滑改善)を実施して潤滑トラブルを削減するという「攻めの潤滑管理」を実施する必要がある。
表2 図4の事例のコスト計算例
|
潤滑点検で,作動油をサンプリングして外観を観察する。変色が大きいものや乳化している場合は新油に交換するという対策を実施している。図2の下段に示すように,作動油タンク内のサクションストレーナやタンク底にスラッジが堆積している場合が多く,油を交換しただけでは改善されない。スラッジトラブルを防止するためには,油を交換するだけでなく,油タンク内を開放して清掃するという潤滑改善が必要である。
なお,機械が停止できない場合は,暫定処置として,可搬式浄油機にて浄油する方法が有効である。浄油することにより,新油に交換するのと同様の効果が得られる場合が多い。オフラインフィルターを設置することにより,浄油の効果が持続できる。
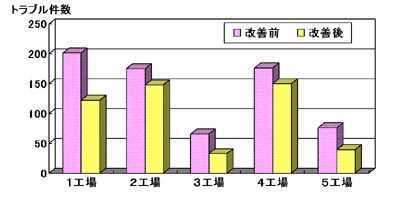
図5 攻めの潤滑管理の効果
図5は,工作機械を800台有する機械工場にて,潤滑管理を実施する前後のトラブル件数を比較したものである。「攻めの潤滑管理」を実践することにより,工場全体でトラブル件数は24%減となり,保全費は25%削減された。
3. 省資源・省エネ
3.1 浄油による作動油の寿命延長
作動油は,定期的に更油が必要であるが,作動油自身の劣化が進んでおらず,汚染物質(異物や水分)の混入がある場合は汚染物質を除去することにより,再利用が可能である。
汚染された作動油をフィルターにてろ過し,再利用することは潤滑トラブルの低減と省資源の観点からも有効である。図6は,金属などを含まないペーパーフィルターであり,廃棄する場合には分別廃棄に有利である。
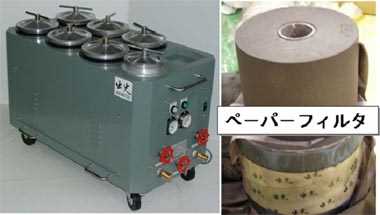
図6 フィルターによる浄油
クーラントが多量に混入し,乳化している作動油タンクの浄油は,真空式の除水装置を使用する。通常のフィルターや遠心分離機では,乳化した作動油の水分の除去はできないが,真空除水装置による水分の除去は可能である。
潤滑トラブルを低減する攻めの潤滑管理を推進することにより,作動油の使用量削減が可能となる。また,作動油の油漏れ防止とコンタミ管理を実施することにより,作動油の使用量削減が図れる。
(1)蛍光剤と紫外線ランプを活用し,油漏れ個所を確認して油漏れを防止する。
(2)浄油により,作動油の汚染トラブルを防止するとともに,作動油の更油間隔を延長して,使用量を削減する。
この活動は,石油資源の有効利用とCO2削減の観点からも有効と考える。潤滑油の使用量削減によるCO2削減効果は,潤滑油を製造するのに要した燃料などを詳細に計算する必要があるが,計算が困難である。潤滑油は最終的には,廃油として再生燃料に使用されるので,廃油の燃焼によるCO2の排出が削減できるとして,計算する。CO2の排出係数は,環境省のホームページから2.63t/kLである。
例えば,作動油を100kL/年使用している工場にて潤滑管理を徹底することにより,使用量を半分に削減すると 50kL×2.63t/kL=131.5t のCO2削減になる。
3.2 省エネオイルによるCO2削減
図7は,市販のZn系作動油と当社の省エネ作動油について,消費電力を比較したものである。タンク容量80Lのホブ盤の作動油の比較である。この比較テストでは,暖気運転時には9.4%,定常運転時でも4.6%の電力が削減された。
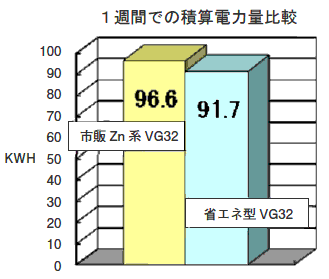
図7 省エネオイルの効果
省エネオイルによる消費電力およびCO2削減の効果を試算する。1台当たりの電力量比較は次のようになる。
〈市販Zn系〉
VG32:96.6kWh×4×12=4,637kWh
〈省エネ型〉
VG32:91.7kWh×4×12=4,402kWh
このような油圧装置が500台あり,電力単価を11円/kWhと仮定すると,消費電力によるコスト低減効果は1,300千円となる。
また,東京電力のCO2係数=0.000358t-CO2/kWhにてCO2削減効果を試算すると,0.086×500=43.0t/年 の削減になる。
おわりに
今までベテラン保全マンが潤滑管理を実践してきたが,2010年問題に象徴されるように,そのノウハウを若い保全担当者に伝授しないまま退職することが懸念される。日本のものづくりを支えてきたベテラン保全マンの技術の継承が,今後ますます重要になる。
このような環境下で,ISOが機械状態監視技術者(トライボロジスト)を標準化しつつある。日本では,機械学会と潤滑学会がこの資格制度を2009年にスタ-トする準備を進めている。潤滑技術をメンテナンスに活用する「メンテナンストライボロジー」という活動が注目されるようになった。潤滑油に携わるものとして,微力ながらこの活動に尽力していきたい。
<参考文献>
*1 幸田 盛堂:工作機械の最新技術動向 29回切削油研究会,2005-11
*2 H15年 次世代工作機械に関する特許出願技術動向調査(特許庁)
*3 上出 和則:工作機械の最近の技術動向,Koyo Engineering journal,No.165(2004)
*4 西端 伸司:工作機械の動向と軸受技術,NSK Technical journal,No.676(2006)
*5 久藤 樹:機械工場の潤滑管理の進め方,トライボレビュー,No.30(2007)
*6 出光社内資料