はじめに
射出成形機は1872年,アメリカのHYATT兄弟によって縦型の空圧式が発明されたと言われている。1869年には世界で初めてプラスチックの成形品が開発されている。
最近では家庭電化製品や色々な電子機器やOA機器,光学機器,自動車などの部品にも金属に代わってプラスチックが広く使用されるようになっている。プラスチック製品が増えている理由には,プラスチックが「軽薄短小化」という時代の要求にマッチしていることと,金属,木材,ガラスなどを代替する強度,耐熱性,透明性のある新しいプラスチックがどんどん開発されていることが挙げられる。
1. 射出成形機の工程
射出成形機(Injection Molding)とは,加熱溶融させた材料を金型内に射出注入し,冷却,固化させて成形品を得る方法である。複雑な形状の製品を大量に生産するのに適し,成形加工の一大分野となっている。
射出成形の工程は大きく分けて6つある(図1)。 ホッパーから粒状のプラスチック材料が投入されて加熱筒シリンダーの中に送り込まれ加熱溶融された状態で前進してシリンダー先端のノズル部分から金型内に注入(射出)し冷えて流れなくなるまで加圧する。
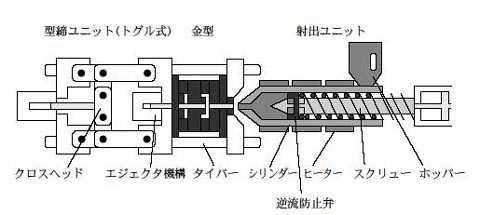
図1 射出成形機の工程
金型へ注入された材料は十分に冷えて固まり,金型を開き冷却固化して金型より突き出して取り出す。以上のような動作を繰り返して同じものを大量に生産する。一般に上記の機械の1サイクル時間は10秒から1分以下である。
射出成形法は射出成形機と金型によって次のような順序で製品を成形する。
(1)型締め…射出前に上下型を締める
(2)射出(注入)…加熱溶融材料
(3)保圧…成形後に保圧(圧力保持)
(4)冷却…製品を冷却
(5)型開き…上下型を開く
(6)製品取り出し…冷却固化して取り出し
2. 射出成形機の構造
自動車製造工場では,中型・大型の射出成形機を主に使用しており,自動車のバンパー他,内装部品を生産している。試作開発部署では小型機が多く電子部品や小型の部品開発に使用されている。
射出成形機には横型と縦型があるが,大体70%以上が横型の射出成形機である。横型の射出成形機は縦型に比べて機高が低くロボット等を付属せずに自動運転ができ,原料の供給が容易で機械の保守がしやすい。
これに対して,縦型の射出成形機は金型の開閉が上下方向に行われるようになっているため機高が高くなっており設置面積が少ない。金型の表面が上向きなためインサートした部品の位置決めが簡単である。また,下型固定で上型の上下動構造を採用すればインサート成形の自動化が容易になり,金型の重量を水平に支えて開閉するので,横型のように重力で前倒れがなく機械と金型精度が安定して耐久性に優れている。
3. 射出成形機の特徴
射出成形機は型締めユニットと射出ユニットに分かれている(図2)。型締めユニットは金型の開閉と突き出し(エジェクト)を行う装置で図1に示したようなトグル方式と油圧シリンダーで直接金型を開閉する直圧の方式がある。射出ユニットは樹脂材料を加熱溶融し,その溶融樹脂を金型へ射出(注入)する装置である。
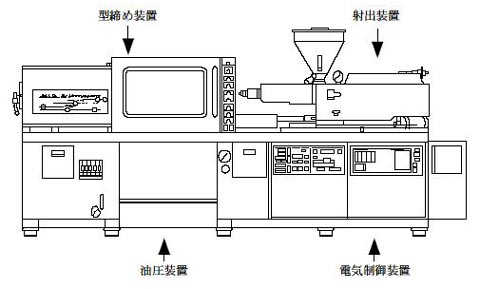
図2 射出成形機概要
工程を順に説明すると,図1のようにホッパーから投入された樹脂材料はスクリューの回転により射出シリンダーの前部へ圧送される。その過程で樹脂材料はヒーターに加熱された射出シリンダーから熱を受けさらにスクリューのせん断を受けて溶融される。成形品およびスプルーランナーに相当する溶融樹脂が射出シリンダーの全部へ溜められ,シリンダーが前進することにより金型へ射出(注入)される。
溶融樹脂が金型内を流動しているときはスクリューの移動速度(射出速度)を制御し,充填された後は圧力(保持力)で制御する。
速度制御から圧力制御への切り替えは一定のスクリュー位置や一定の射出圧力に達したときに切り替わるように設定する。
4. 設備の現状問題点
自動車生産工場の射出成形機は,中型,大型が多く高速化に加えて自動化されている。設備の構造も複雑化しており機能と精度を維持することが最重点課題となっている。また,最近では設備運転中や保全作業中の重大災害の事例も多く,安全性の高い設備が要求されている。
設備のチョコ停止や重大故障また,品質不良や災害の要因の多くは潤滑管理の不備や潤滑油の汚染が起因していると言っても過言ではない。チョコ停止の現象は重大故障や災害発生の前兆であると考えなければならない。特に油圧設備はこの時点で使用油の汚染状況や性状を分析診断して早めの対策をする必要がある。
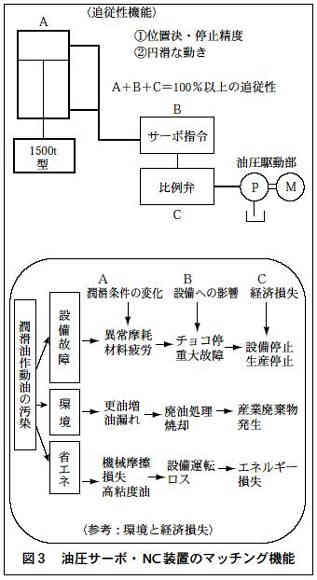
図3 油圧サーボ・NC装置のマッチング機能
射出成形機は高度な技術と複雑な構造になっていることから作業環境面や日常の保全性の点では考慮すべき点が多い。その一つとして設備周辺が異種油や粉塵また冷却水によって汚染が激しく,潤滑油が汚染されやすくなっている。二つ目は日常の点検面である。設備はほとんどが安全策で囲まれており自動運転されている。また,油圧装置,潤滑装置は機械内部に装備されているものが多く,日常のメンテナンスが十分とは思われない。
機械故障の中では独自故障の他に機械系と制御系のマッチングによるものが多い(図3)。
射出成形機はNC装置と油圧サーボ制御装置により連続運転されている。これらの装置は,複雑に組み合わされているために, 100%の追従性がなければ設備の価値がないと言っても過言ではない。故障により設備停止損失,品質不良さらには安全性を阻害して大きな経済損失になりやすいのである。
5. 使用油の汚染状況
出成形機の潤滑油(作動油)の汚染状況を調査したところ,全設備の60~70%の設備で使用油の汚染が確認された。汚染状況を表1に示すが,使用油汚染の要因の一つとして設備から発生する粉塵汚染がある。成形時に発生する粉塵や異物また,材料投入時の微小な粉塵による汚染である。
表1 使用油汚染状況
|
要因の二つ目として,成形された製品の冷却に使用する冷却水の混入によりタンク内が汚染され,潤滑油の急激な性状変化と酸化変質物の堆積で汚染が拡大し,油圧装置全体に及ぼす影響が大きいことがわかった。
6. 射出成形機の故障事例
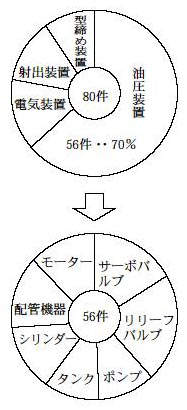
図4 装置別故障(平成15年1~6月)
射出成形機は故障現象として「射出成形できない」また「成形不良が出る」などで長時間の設備停止となっている。射出成形機の故障現象を装置別に見てみると,図4に示すように潤滑油(作動油)のトラブルが非常に多く,汚染の影響が大きいことがわかる。
7. 故障モードと原因について
油圧装置の故障内容を図4に示すように油圧装置の駆動部と制御バルブ系の故障が全体の50%を占めており,非常に多いことがわかる。そこで故障の内容と原因を調査したところ,故障モードとしてサーボバルブやリリーフバルブの作動不良や圧力低下また,吐出不足,作動油の加熱などが挙げられる。
原因については,異物(スラッジ)のつまりによる作動不良や弁座の異常摩耗による内部リーク等の他に作動油の粘度低下や油量不足等が挙げられる。表2に詳細を示す。
表2 故障モードと原因
|
以上,油圧装置の故障の直接の原因は先にも述べたように,射出成形機に使用される冷却水の混入や,材料投入時または成形時に発生する粉塵による作動油の汚染の影響と,設備の使用条件に応じた日常の汚染管理と潤滑油診断が定着していないためである。
8. 潤滑油管理のポイント
(1)日常の潤滑管理基準値の設定
作動油の汚染状況をみると冷却水の混入や粉塵による汚染に加え,高温使用による酸化劣化が激しく,スラッジの発生や極端な作動油の性状変化が起きやすく油圧装置に与える影響が大きい設備故障は必ず機械系と制御系のマッチング現象であり潤滑油が起因している。このようなトラブルは設備機能低下につながるばかりか安全性と作業環境を悪化させることも真剣に考えなければならない。
故障の原因は設備の潤滑条件が変化して摩耗が起こり機械的に摩耗が進行して作動不良を起こしたり,油中の酸化変質物や金属粉のつまりなどによるものである。
特にサーボ制御やNC装置を使用している設備は機械動作と指令は常に100%の追従性を必要とするため,スプールの汚れや摩耗によってサーボバルブの動作不良などは絶対に起こしてはならないのである。そのためには作動油の汚染度は常に管理限界以下に維持して10ミクロン以下の微小金属粉や酸化変質物までを完全に除去しなければならない。故障の多くは,油中の酸化変質物や10ミクロン以下の微小な金属粉が摩耗を進行させたり,スプールのつまりを起こさせたり,油起因故障の直接の原因となるため,設備内部を循環している潤滑油の状態を分析して潤滑条件の改善や日常の汚染管理の定着が重要である(表3)。
表3 日常管理基準値
使用油ISO VG46(耐摩耗性)
|
(2)特殊浄油装置と汚染管理
バルブやポンプをうまく作動させて機能を維持するには,物体の潤滑油領域に応じた適正な潤滑油と油膜が最も重要である。それが設備の精度にも大きく影響するのである。射出成形機は外部からの粉塵や冷却水また,異種油による影響を受けやすく潤滑油,作動油が汚染されやすい環境である。油圧ポンプやサーボバルブの異常摩耗やつまりの直接の原因は10ミクロン以下の金属粉や酸化変質物である。そこでこれらの異物を完全に除去する方法について紹介させていただく。
直接の原因となる,これらの微小金属粉や酸化変質物(スラッジ)の除去は一般的なフィルターでは不可能である。油圧装置の高速化になるにつれて5ミクロン以下の異物の完全除去を汚染管理の対象にしなければならない。そのためには日常の汚染管理基準値に基づき電気式の浄油装置や静電浄油機また,トリプルアールを実用化させていくことが必要である(表4)。
表4 浄油機の実用化
|
最近では,汚染度の激しいものや,難燃性の作動油を対象にした特殊浄油装置とトリプルアールと添加剤投入装置を組み合わせた浄油装置も開発し,実用化されているので使用条件に応じて使い分ければ故障低減はもちろん,使用油の寿命延長等経済性効果も大きい。
(3)添加剤「ジャスエース」によるスラッジ対策
自動車生産工場の生産設備に使用される鉱油系の潤滑油(作動油)の汚染管理を徹底させるため有力な手段として移動式または,定置型の各種バイパス式の精密浄油装置による「浄油」が行われてきた。
浄油装置設置直後は,異物によるバルブの故障は激減して,油の酸化劣化を抑えて油の寿命を大幅に延ばし更油回数も減少することで相当に普及してきた。
しかし,最近は浄油後のトラブルが多い,また故障率がだんだん増えてきたとの意見があるため調査したところ,次のような課題や問題を残していることがわかった。
- 定置型ではほとんどが設置後のメンテナンスが不十分である
- 使用油の条件が悪く処理精度が悪い
- 粘度の高い使用油は処理時間が長い
- タンク内は浄油できるが,複雑な回路内は浄油が困難である
- 添加剤の消滅が大きく,新油の追油が必要になる
制御バルブ系の内部汚損やスラッジの固化対策として鉱油系の潤滑油(作動油)を対象にした添加剤が開発されている。
固化したオイルスラッジを溶解し,油中でのスラッジを抑制して使用油の劣化を抑え,汚染防止にオイル添加剤(ジャスエース)の実用化を推奨する。 1985年頃からオイル添加剤の新たな調合と使用方法が開発された。この添加剤を投与することにより油圧機器内やタンク内のスラッジ発生によるトラブルが激減することが判明した。
最も故障の原因を成しているのがオイルスラッジやカーボンスラッジである。極論すればこの2つのスラッジを除去して発生を抑えてしまえば流体潤滑ラインにおける突発故障の多くは解決するのである。
添加剤(ジャスエース)は潤滑油(作動油)が必要とする摩耗防止剤,スラッジ分散剤,酸化防止剤,泡止剤,防錆剤等がバランス良く調合された「予防保全」を目的とした非塩素系の添加剤である。
まとめ
設備の高速化,高精度化が進む中で生産工程は有機的にライン化されている。したがって,一部の設備故障や誤った判断により大きな経済損失や環境汚染や災害につながる危険性を内蔵している。
潤滑油管理は単なるコストや経費の観点から考えるのではなく,汚染防止とリサイクル化を真剣に考えなければならない。そのためには日常の徹底した潤滑油管理が重要であり,使用者および保全技術者が一体となって状態監視しながら汚染管理と潤滑油診断を定着させていくことが急務である。汚染管理と使用油のリサイクル化により廃油を出さないことが地球にやさしい潤滑油管理といえる。