はじめに
電力設備の保全方式は,定期的な点検により保全を実施するTBM(Time Based Maintenance:時間基準保全)が中心であったが,最近では様々な設備診断技術を用いて設備状態を継続的に監視(Condition monitoring:CM)し,設備機器の状態を科学的・合理的に評価して適切に保守を実施するCBM(Condition Based Maintenance:状態基準保全)へと変更が図られており,これにより点検周期の延伸化や保全の最適化による保守費用の削減も志向されている。
トライボロジーを活用した潤滑油診断法は,1980年代前半から水力,火力発電などの電力の現場での活用が始まり,近年では風力,内燃力でも活用されている。中でも,原子力発電設備を対象として2009年度から始まった新検査制度を期に,潤滑油診断法は,振動法,サーモグラフィー法と共に保全活動の適切で的確な推進と,設備のさらなる安全性と信頼性の確保に向けてCBMのコア技術として導入され始めている。
当社は,実機の軸受損傷試験などの結果から,電力の現場に役立つ潤滑油診断法の開発と状態監視技術の向上を目指してきたが,本稿では「機械の血液」とも言える潤滑剤の分析による設備診断の概要と事例,そして当社がこれまで実施してきた設備診断への適用の有効性も紹介する。
1. トライボロジーと経済効果
トライボロジー(Tribology)は,1966年に英国の科学技術省が摩擦摩耗に関する損失を調査・発表した「JOST報告書」で初めて提唱された言葉として知られているが,一般には摩擦(Friction),摩耗(Wear)および潤滑(Lubrication)を包括する学問や技術を意味し,「相対運動をしながら互いに干渉し合う二面,ならびにこれに関連した諸問題と実地応用に関する科学と技術」と定義されている。
JOST報告書で提唱されたトライボロジー(摩擦・摩耗・潤滑)技術の改善による経済的効果は,表1に示す7項目についてその節減効果を明らかにしている。
表1 トライボロジー技術の改善による経済効果
|
それは,(1)保全費・部品交換費の節減,(2)耐用年数の延長による設備投資の節減,(3)破損で生じる波及効果の節減,(4)労働力の節減,(5)稼働率・機械効率の向上による設備投資の節減,(6)摩擦減少によるエネルギー消費の節減,(7)潤滑油経費の節減で,1966年当時の英国経済から算出したこれらの項目の節約額は,実に国家予算の約10%に相当する5億1500万ポンド(当時の換算レートで約5000億円)といわれている。
JOST報告と同様の算出式に基づき,(社)潤滑油協会などが日本における経済効果を検討した調査報告によれば,適正な潤滑管理の実施による最大経済効果は,1968年当時で年間約1.99兆円,また1994年当時で13.5兆円と試算されている。
このように,適正な潤滑管理は,大きな経済損失を防止でき,保全コストの低減に寄与できることがわかると同時に,トライボロジーに関連する技術の経済的重要性が認識される。
2. 潤滑油診断法
設備診断は,表2に示すように温度法・振動法・AE法・電気抵抗法,そして潤滑油診断法など種々の手法があり,それぞれの特性を活かし,保守・保全に活用されている。
表2 各種設備診断法の特徴
|
なかでも,振動法は,取り扱いが比較的容易であり,また測定機器類が豊富で測定が簡便であることなどから回転機器類の診断に多用されているが,低回転機器やすべり軸受などへの適用は困難であることが知られている。一方,潤滑油診断法は,摩耗粒子を直接観察でき,また異常検出感度が高く,さらに摩耗粒子の形状と材質から異常の発生原因や発生箇所を調査することが可能であるといった特長があることから,潤滑油が採取できる設備には有用な設備診断技術である。
3. 実機軸受損傷試験
当社では,すべり摩擦試験機を使用して得られた状態監視パラメータを用いて実機軸受による「実機軸受損傷試験」を実施し,異常予知診断の有用性を確認し,設備診断の精度確認を実施してきた。
本項で紹介するのは,更新予定の水車発電機を使用し,故意に軸受を損傷させる過酷な条件を与え,しゅう動面から発生する摩耗粒子などのデータを収集した例である。
試験に使用した発電機は,横軸型750min-1・2000kWの水車発電機の軸受である。図1内の破線内に試験軸受を示す。軸受には,表3に示す軸受温度,軸変位,回転速度,振動を測定するセンサーを取り付け,油中粒子をオンサイトでリアルタイムに測定する装置により,摩耗粒子の発生状況から潤滑状態の変化を測定した。
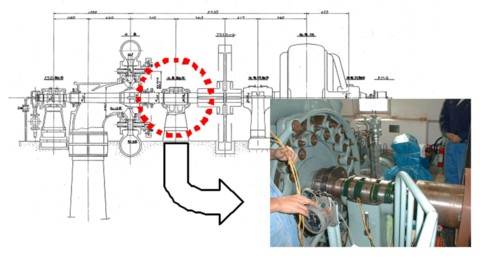
図1 軸受損傷試験の対象軸受
表3 測定機器
|
試験(図2)は,ヒーターを使用しない定常運転と昇温試験とした。主軸と軸受のすべり面で油膜が若干切れる,いわゆる混合潤滑状態とする必要があることから,外部ヒーターで油温を徐々に上げながら粘度を下げ,油膜を次第に薄くし流体潤滑から局部的な混合潤滑状態を発生させた。混合潤滑状態の確認は,潤滑油中の粒子数変化を油中粒子測定装置で監視した。定常運転時の試験は,油温が約32℃,回転数は定格の750min-1で約1時間実施した。この間,油温は47.7℃まで上昇したが,5~15μmと15~25μmサイズの粒子数はほとんど増加しなかった。
潤滑油昇温試験は,定格の750min-1に保持したままヒーターで潤滑油を昇温し,油膜を徐々に薄くして実機軸受の使用限界温度の目安としている75℃程度を約1時間保持した。この間,5~15μmサイズの粒子数は2×105個/100mL程度から最大で3×105個/100mL程度に増加した。高温試験は,75℃保持試験後に約2.6℃/10分程度の温度上昇を続け,最高油温108.3℃まで昇温させたが,この試験では,5~15μmの増加が顕著で,続いて15~25μmサイズもやや大きな変化を示した。
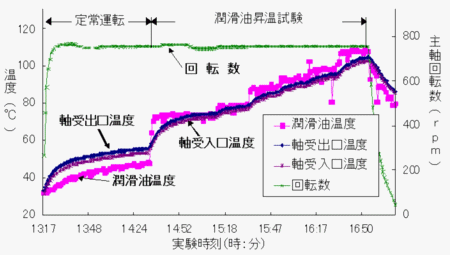
図2 実機軸受損傷試験
3.1 試験軸受の観察と発生粒子の検討
試験終了後に観察した軸受表面は,図3(a),(b)に示すように,試験前には観察されていなかった回転方向に直交する迫り出し部が観察されており,迫り出し部で油膜が薄くなり混合潤滑状態となっていたことを示唆していることが確認された。油中では,潤滑状態が厳しくなると軸受表面から摩耗粒子が発生する。そこで,定常運転で健全な状態の粒子数データを3点とり,その平均値と昇温試験で発生した粒子数との比率を粒度分布比として表し,潤滑状態状況の検討を行った。その結果,図4に示すように,潤滑状態が厳しくなったと思われる75℃保持試験中には,粒度分布比が大きくなり始める粒子サイズが発生していたことがわかった。
(a)試験前
(b)試験後
これらの結果から,油中粒子は潤滑状態を表すパラメータであり,潤滑状態が厳しくなるとともに増加し,10~30μmサイズの粒子が徐々に多くなることが分かり,油中粒子の粒度分布比は,潤滑状態を評価する新たなパラメータとしての活用が確認でき,発生する摩耗粒子の粒度分布の変化を捉えることで潤滑状態を診断する方法が有用であることが確認できた。
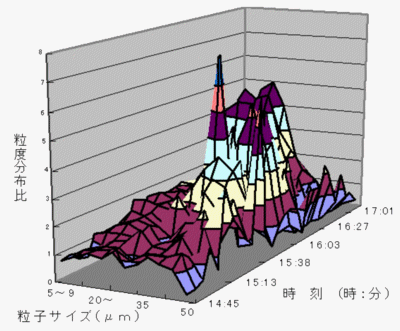
図4 発生粒子の粒度分布比
4. 潤滑管理の必要性
図5と図6は,大手電力会社の1992年から2009年までの17年間にわたる水車発電機の潤滑油汚染度の管理結果である。これらのデータは,試験機による摩擦試験と実機による実証試験とで得られた結果と,さらに実機データも反映させて評価パラメータと閾値(管理基準値)を制定して診断を継続したものである。
水車発電機の圧油は,油圧系統に精密な電磁弁類があることから,汚染度が悪化した場合の影響を受けやすく油の汚染度管理は重要である。管理基準を制定した当初,「良好」と判断されたものは60%程度であったが,管理に対する意識の向上とともに,対策と対応が円滑に進み2000年以降は70~80%程度に向上し突発故障が激減した。
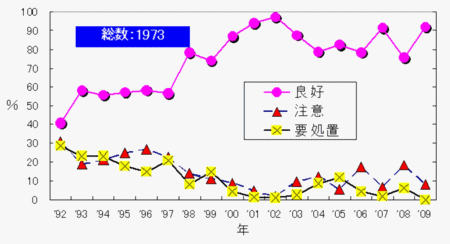
図5 水車発電機の圧油汚染度
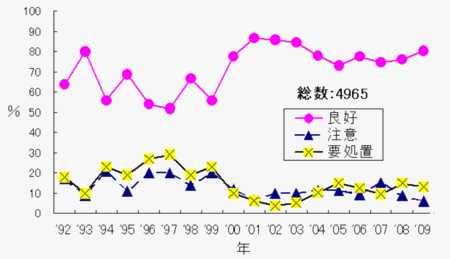
図6 水車発電機の潤滑油汚染度
また,潤滑油の管理データも,圧油と同様に管理が始まった数年間は良好な状態が50%程度であったものが,2000年以降は70~80%以上が良好な状態を維持している。ここで紹介する大手電力会社の水車発電機は,負荷に応じて起動停止を繰り返すことが多い発電機も保有しているが,起動停止の多い発電機は短時間であるが周速が極めて遅い瞬間があり,油膜が形成しにくくなる。そのため,潤滑管理のデータには一定の割合で汚染状態が「注意」と判断されるものもあるが,潤滑油診断技術は軽度な摩耗状態でも早期に検出できることから,データに基づき更油や濾過,あるいは軸受のギャップ調整を計画的に実施するなど保守が的確,適切そして迅速に実施されている。
実機の使用条件を反映させて実施した実験と,実機の損傷試験などで得られた貴重なデータとから制定された管理基準を適用したこの一例は,20年以上にわたるCBMの実例であり,管理基準を制定して適切に運用する好例である。
おわりに
電力の現場では,保全形式をTBMからCBMへと移行させ,設備の状態を非分解で適切に評価しながら,設備の状態に応じた最適な保全や,効率的な設備稼働,そして保全の最適化による保守費用の削減も志向し始めており,設備診断技術には大きな期待が寄せられている。
機械の血液とも言える潤滑油は,設備の機能を十分に発揮させるために重要な役割を果たしているが,これまでの潤滑油に対する管理の中心は,「油の劣化」,あるいは「油の汚染」など,どちらかと言えば,油の性状把握や取替時期に力点が置かれていることが多いように思われる。
今回紹介したように,潤滑油には,潤滑状態を教えてくれる情報源としての「摩耗粒子」が存在しており,この「情報提供者」から設備の健康状態を非分解で知ることができれば,点検時期を合理的に判断することもできることから,コストダウンに寄与できるばかりか保全形式の主流となっているCBMにも成果が期待できると思われる。
<参考文献>
*1 赤垣 友治,加藤 康司,川畑 雅彦,古矢 千吉:“フェログラフィーによる実機ジャーナル軸受の破損過程の解析”,日本機械学会,第69期全国大会名古屋,Vol.C.1991,pp471-473.
*2 赤垣 友治,加藤 康司,川畑 雅彦:“フェログラフィー及び発光オイル分析法によるジャーナル軸受の異常診断に関する研究”,トライボロジスト,Vol.39.11.1994,979-986,pp47-54
*3 川畑 雅彦:“発電設備におけるメンテナンストライボロジービジネス”,トライボロジスト,49,3(2004),pp206-212.
*4 川畑 雅彦:“潤滑油診断技術の発電設備への適用”,日本保全学会,「第一回検査・評価・保全に関する連携講演会」,2008,pp65-68.
*5 神谷 徹,川畑 雅彦,宮田 昇,山下 和彦:“オンサイト潤滑油診断”,日本保全学会,「第五回学術講演会」要旨集,2008,pp67-70