はじめに
近年,インダストリー4.0,コネクテッドインダストリーズの取り組み,Society5.0などが提唱され,生産性向上や人手不足の解消,品質向上など製造業が抱える課題への取り組みが急速に進展している.それらの課題を解決するために,工場の設備や製造工程における異常検知や予兆検知等のコンディション・ベースド・メンテナンス(CBM),外観検査自動化,不良原因分析・歩留まり改善,最適化等のIoT技術やAIを用いた取り組みが拡大している.
1.コンディション・ベースド・メンテナンス(CBM)とは
現在,一般的にメンテナンスで運用されている一定の期間で点検・補修・部品交換を行う時間基準保全のことを,タイム・ベースド・メンテナンス(TBM)という.一方,機械から収集する各種センサーデータを活用し,故障や異常が起きる前に修繕・対策を行う状態基準保全のことを,コンディション・ベースド・メンテナンス(CBM)という.これら異常検知や予兆検知といったCBM技術は,機器や設備の異常を瞬時に検知し動作を停止するなど,メンテナンスコストの増大や生産性の大幅な低下を回避するためのアクションに直結するため,工場運営や設備管理の面で取り組みに対する効果が大きい.最近では工場設備のみならず社会インフラ関連の設備へも導入が進んでいる (図1).
本稿では振動センサーおよびAIを使った異常検知や予兆検知のCBM技術だけでなく,我々が実際の製造現場で取り組んでいる経験を基にプロジェクトの進め方やよくつまづくポイントについても紹介する.
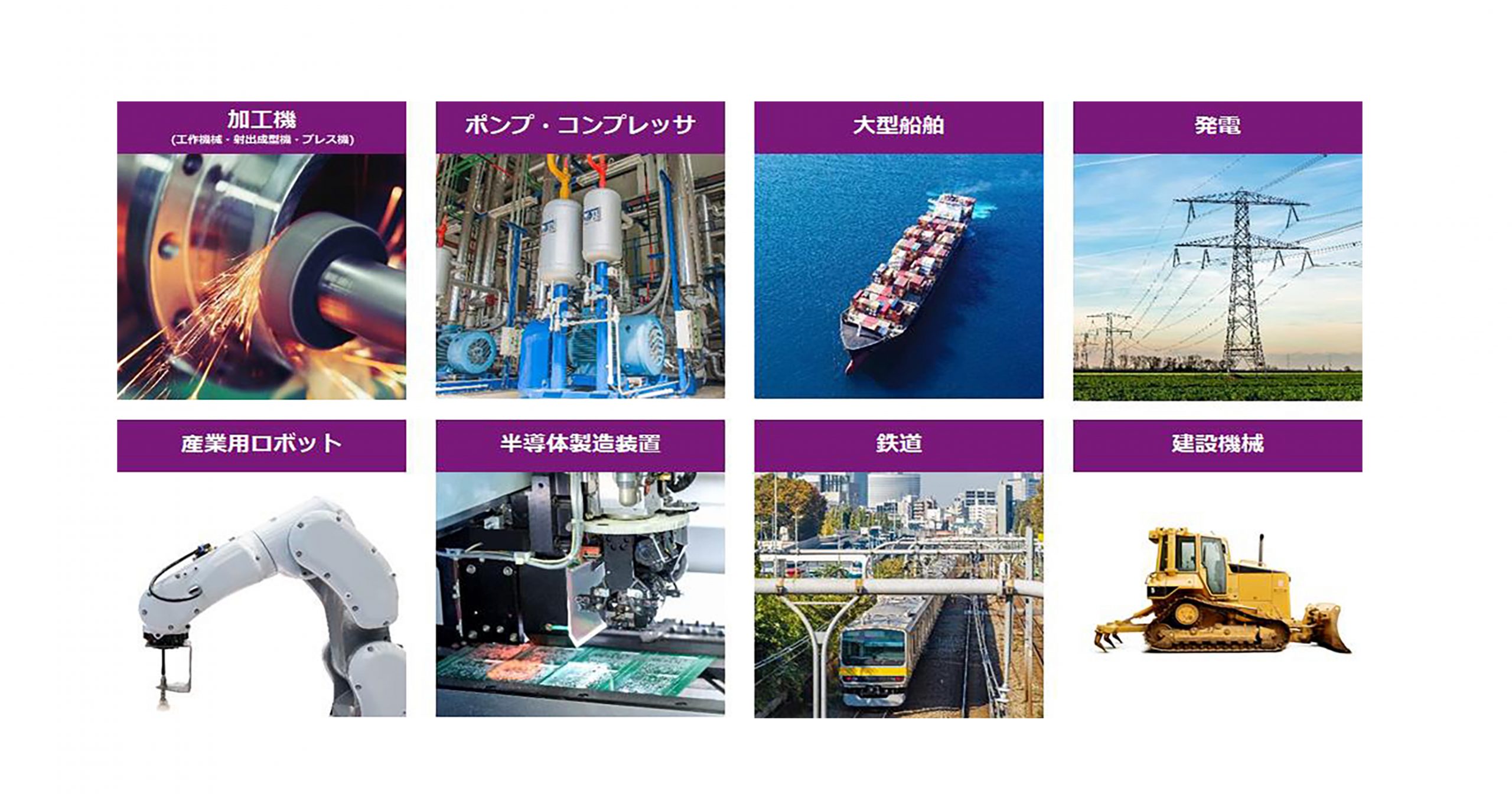
図1 CBM導入が進むマーケット例
2.CBMの市場での取り組み変遷
弊社が感じるここ数年の市場における取り組み指数の移り変わり(図2)について説明したいと思う.
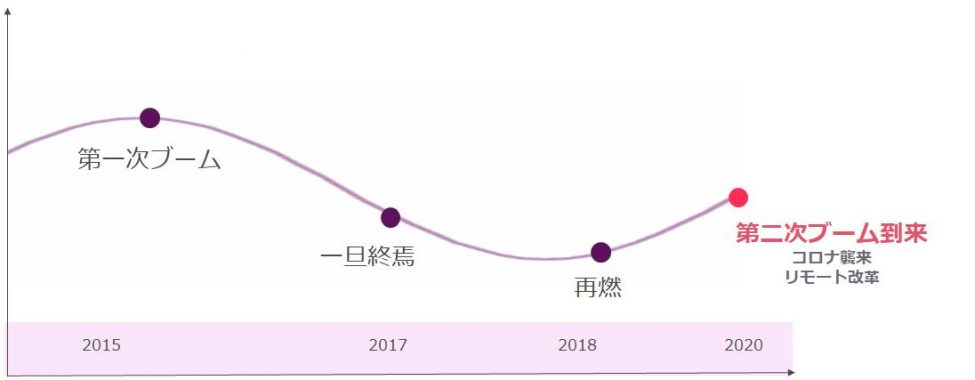
図2 市場取り組み指数の推移
2015年~16年 第一次ブーム到来
ドイツのインダストリー4.0や米国のIIC(インダストリアルインターネットコンソーシアム)を筆頭に,世界的に製造業へAIやIoTといったデジタル技術の活用が提唱されるようになった.その取り組みテーマ筆頭として一大ブームが到来.
2017年 第一次ブーム終焉
多くの会社が何らかの形で研究や実証を開始.当初の期待値としては,AIなどの技術を使えばどの設備でもポン付けですぐ劣化を知らせるシステムができるという期待感の中で,実際にテーマに着手してみてはじめて運用までの道のりの長さや,想定外にかかる費用などをはじめとする諸々のハードルを理解する.これらの理由で当時多くを占めていた取り組み先行型テーマが導入効果との兼ね合いで取り組み断念を余儀なくされるケースが見受けられた.表立ったバズワードとしてのCBMブームは終焉した.
2018年~ 第二次ブーム到来
第一次ブームほどではないものの,取り組みがまたじわじわ再燃.注目すべきはその多くが第一次ブームのときに多かったCBM単体&導入先行型ではなく,導入効果検証が事前に慎重になされた上で計画化されており,その背景がトップダウンのDX方針を実現するための手段として連動しているケースが多く見受けられるようになった.これら運用を見据え検証が具体化するテーマが増加し本質的な活用フェーズに突入したと感じる.また,ここにきて最近ではコロナウイルスの影響によるリモート改革の一環としても再度注目を浴び始めている.
このように紆余曲折を経つつも着実に現場活用に向けたステップを進んでいるというのが弊社の見解である.
当初,皆が思い描くほど実運用化されるケースに至るまでは時間こそかかっているものの,当時市場全体が手探りであった状況からはかなり取り組みを進めやすい知見や土壌が整ってきているように感じる.
3.最新動向
3.1 自動化システムでのCBM検討
最近増えているのが自動化システムの実現とセットでの検討である.例えば,製造業を例にとると,作業員が現場にいる場合,加工中の工具に故障や異常が発生してもすぐに気づき対処できるケースが多く,ロスはほとんど発生しない.逆に,自動化され無人となった工程では必然的に機械の異常や劣化状態をモニタリングする仕組みが人に取ってかわり必須となる.そもそも自動化システム自体が生産性向上を目的に導入されるため,異常が発生した時に生じる機会損出や,仕損じ品の流出といった生産ロスも甚大になるため,より必要性が高まる(図3).
また,製造業のみならず,船舶や建設機械といった大型の移動体も無人自動操縦に向けた開発が進んでおり,CBM検討が進んでいる.これら海運や建設業をはじめとする社会インフラは長年現場作業員の高齢化や人手不足,それを助長する過酷な就労環境が社会問題となっており,ICT技術の活用で現場作業の負担軽減と省人化実現が急務となっているためである.
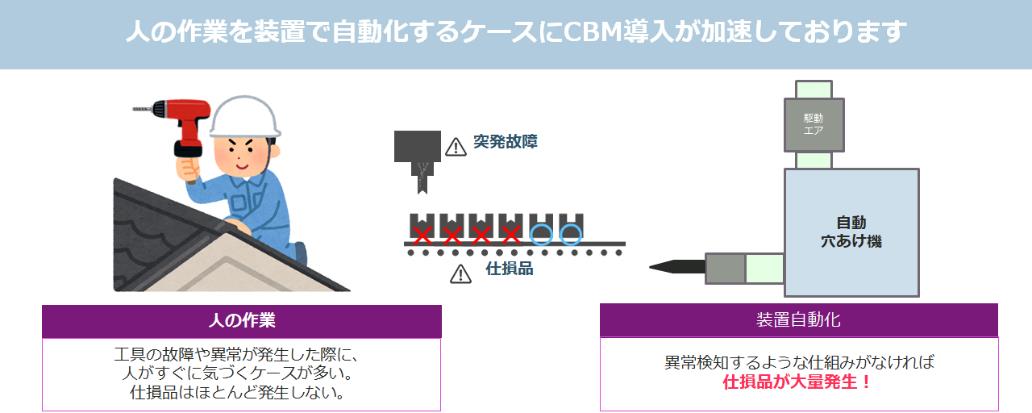
図3 設備自動化に伴う異常検知システムの必要性
3.2 クラウド×サブスクリプション型サービス
最近では,既存設備にレトロフィット的に後付け可能で,センサー~可視化システムまですべてパッケージ化されたサービスがリリースされてきている.これを利用することでユーザーは自分たちでシステムを構築することなくCBMを開始することができる.
これらのサービスが最近になって進展してきた理由は,現場でのクラウド活用の理解が進んでいることがいえるだろう.クラウドを活用することでサービスを提供する側としてはユーザーの管理がしやすくなるし,ユーザーとしてもオンプレミスで個別に構築するより大幅に導入コストも利便性も向上する.製造業でも少し前までは工場のセキュリティポリシーの観点でクラウド活用自体が断固NGである企業が多かったものの,最近ではもたらされるメリットとデータ秘匿性の観点で使い分けが進んできていると感じる.具体的には工場内の生産稼働内容に直接関係ない装置自体の異常を知らせるためのセンサーデータはクラウドに上げても問題ない,という判断が少しずつなされるようになってきている.
これらパッケージサービスは初期費用を抑えたサブスクリプション型で展開されているものが多く,何といっても導入ハードルの低さが魅力である.地道にスクラッチでCBMシステムの構築を進めようとすると,実現できるかどうかを見極める段階のPoCフェーズですら期間として数ヵ月~長いものだと半年以上,費用も数百万円かかってしまうのが普通であり,CBMを体験することなくプロジェクトを挫折させてしまう大きな要因となっていた.これらのサービスを活用すれば汎用的ではあるものの,CBMをまず体験し,効果を見極めたうえでシステムをエンハンスするか,やめるかを判断することができるようになる.現状はまだサービスが出てきたばかりの段階であるが,今後検知精度などユーザーにより異なる個別要求への幅広い対応や,実際に効果を体感したユーザー事例の浸透などが進めば,世の中的にも広く最初の選択肢として活用されると期待している.
なお,弊社でもサブスクリプション×クラウド型のサービスをリリースしている(図4).弊社のサービスは広帯域振動センサーを活用しており,より故障の予兆を早期に発見できるのがポイントである.広帯域振動センサーの有用性は後述する.
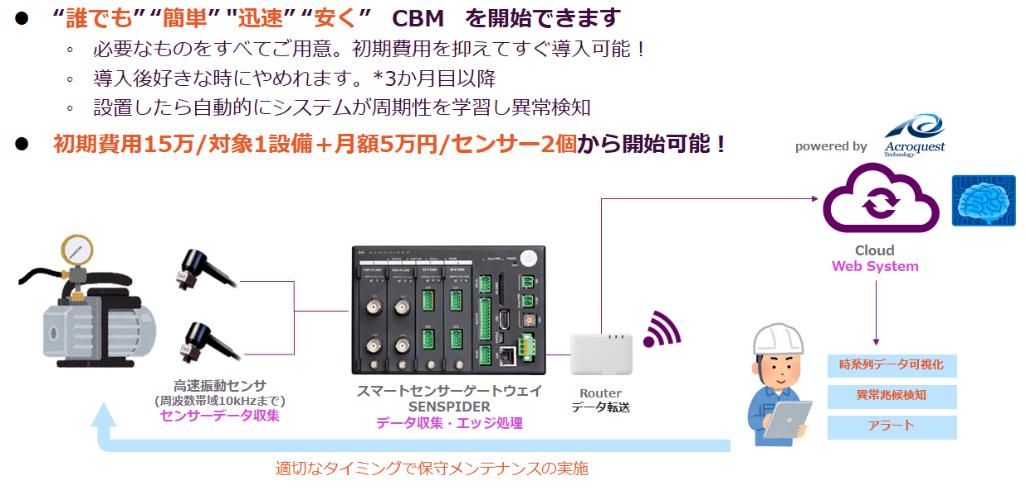
図4 マクニカ サブスクリプション型サービス
4.システム構築に潜むつまづきポイントや解決の方法
ここからは数々のプロジェクト経験にもとづく,CBMシステム構築をスムーズに進めるためのポイントを説明する.
4.1 導入効果の見極め
何でもかんでもCBMを導入すればよいというものではなく,テーマ着手する前に,そもそも導入コストをかけて進めるべきかどうかを慎重に判断することが重要である.例えば,壊れた時の経済的インパクトが大きく,頻度も高いようであれば,そもそも機械自体の見直しが必要となる.逆に,故障する頻度が低く,経済的なインパクトも低い場合は費用と期間をかけてCBM機能を導入するより,交換部品をもっておくことで十分対応できるケースもある(図5).
このように,最初に導入効果が高いスコープの見極めを行い,できるだけ定量的に効果を指し示すことができるテーマは検証に必要な予算確保もスムーズである.それ以外にも,先に記載したように自動化を成立させるためのCBMや,機械の状態が生産物の歩留まりやロスに直結するケース,普段人が立ち入れないところに装置があり遠隔で装置の死活を監視すること自体に価値があるなど,導入の背景に必然性の伴うテーマは逆算して費用対効果を試算しやすく進めやすいといえる.
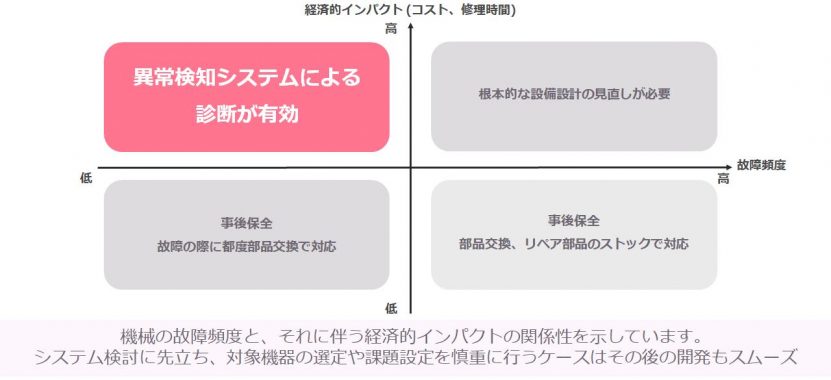
図5 導入効果の考え方
4.2 最初から完璧に異常を検知できるシステムを目指さない(目指せない)
前提として,異常を検知する判定モデルを作るために,検証段階で想定される異常時の再現を行い,データ収集が必須と思われがちであるが,この“リアルな異常時のデータ収集”は容易ではない.もはや永遠の課題ともいえる.そもそも,工程で実際に使っている高価な機械に傷をつけることはできないし,仮に検証機を用意したとして,そこに傷をつけたり,砂を混ぜたり,グリースを抜いたり,模擬的に異常時を再現することもできるが,どうしてもリアルな劣化時のデータとは差分がある.これら開発環境と本番環境との差分は判定精度に影響を及ぼすノイズとなる.これらの理由で,最初からすべて想定されるありとあらゆる異常時のデータを学習させることは不可能と考えたほうがよい.このように最初から想定されるありとあらゆる異常状態を完璧に検知できるシステム構築を前提に進めてしまうと大体のケースで失敗してしまう.
そのため,まずは正常データを活用した教師なし学習でしっかり正常時の確立を行い,外れ値を検知できるシステムで一旦は運用を開始し,そこで新たに出くわす異常を定期的にシステムに学習させ少しずつ精度を上げていく前提でアプローチを検討するのがよい(図6).
もう少し補足すると,実は一言に正常時といっても,そこには数多くの外乱により生じるばらつきが存在する.測定したい事象に加え,設備の違い(機種ごと・個体ごと),測定環境の違い(センサー個体差など),電気的なノイズ,動作モードの違い,設置環境など数多くの外乱要因が収集データに影響を及ぼす.そのため,まず正常時をばらつき含めきちんと定義づけることが重要である.正常時のデータ収集は日々の工程からすぐ開始することができるので,異常時に比べハードルが低いことは言うまでもない.
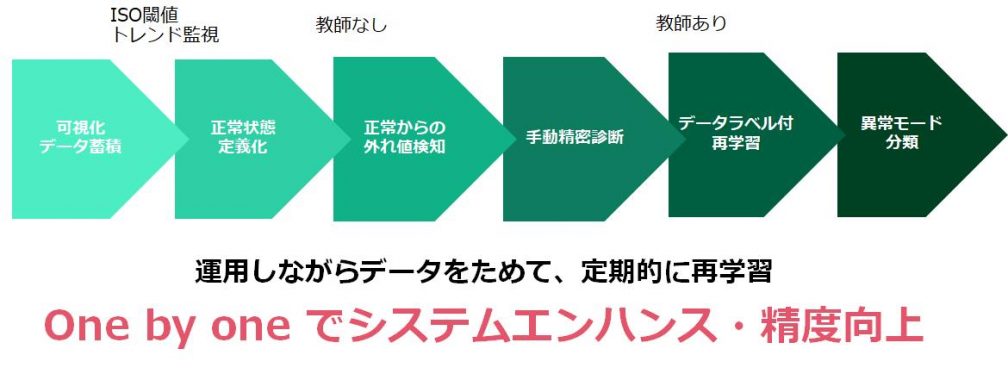
図6 検知精度向上に向けたステップイメージ
4.3 目標設定の明確化
そもそも,何をもって“異常”とするか,定性的な目標設定を最初に行うことが重要である.例えば,一言に異常といっても求められる値は認識が違うこともある.最初にプロジェクト関係者の中で異常の定義についてなるべく定性的な認識合わせを行うことで,検証を行うために必要な環境や,先に説明したばらつきもどの程度許容できるか,おのずと決まってくる.また,検証時におけるデータ収集は,その時の装置の状態をできるだけ詳細にデータと紐づけ管理することが重要である(図7).
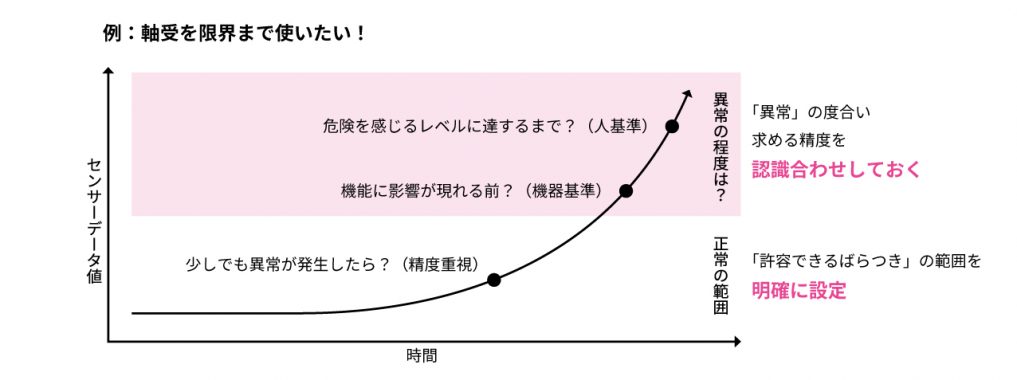
図7 目標設定の明確化
5.CBMを成功させるキーテクノロジ-
5.1 データ収集(広帯域振動センシング/前処理の重要性)
近年,IoTやAI技術の発展とともにセンシング技術の重要性が増大しているが,製造現場や各種プラントにおける各種センサーを用いた設備診断(異常検知等)というのは1970年代頃から行われている.
製造現場や各種プラントにおいては様々な設備が存在するが,中でもポンプやコンプレッサー,タービン,モーター等の回転機械は非常に多く使用されており,回転と負荷を伴う機械であることから故障も多いため,振動センサーを用いた診断技術も古くから用いられている.
一般的に回転機械は振動しやすい機械であり,機械的な故障が発生した際も振動現象の増大として現れることが多い.故障した際に機械に現れる現象としてはモーター負荷の増加(駆動電流の増加)や温度の上昇,振動や騒音の増大等が挙げられるが,特に振動に関してはより早期の異常から現象として現れることが多いことから設備診断に広く用いられている(図8).
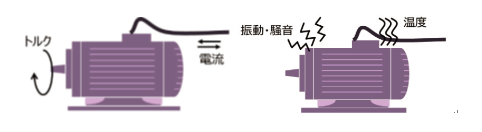
図8 機械故障時の現象例
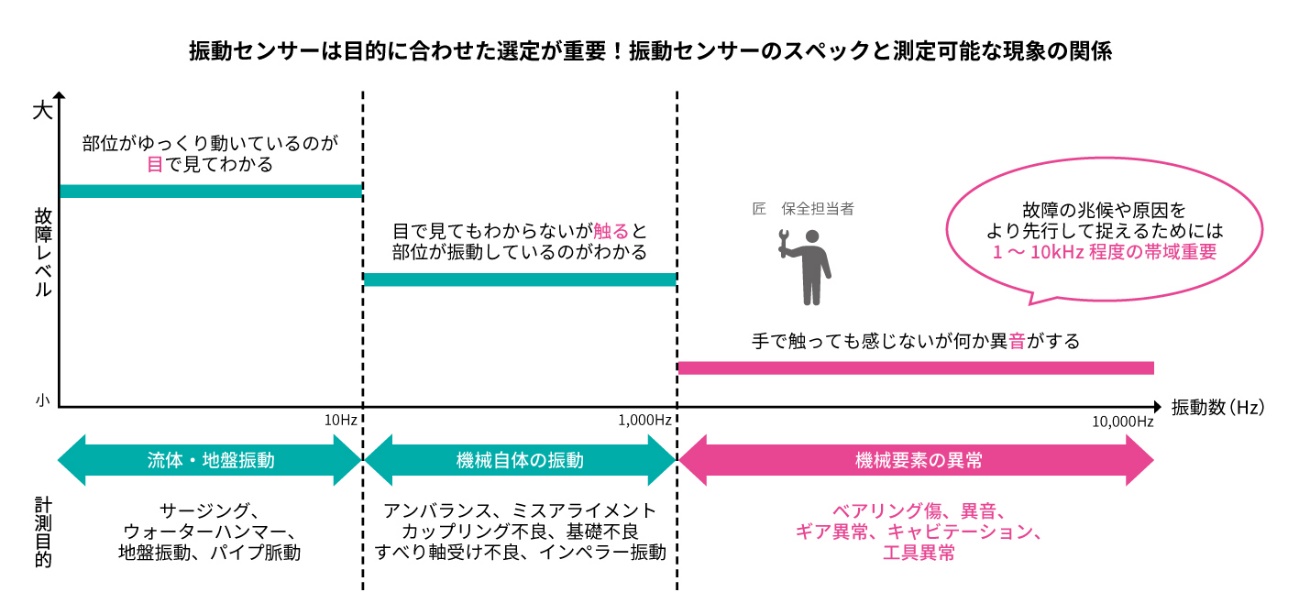
図9 広帯域振動センサーの有用性
回転機械異常の中でもベアリングやギアの傷や摩耗等の発生しやすい劣化を検知するためには,1kHz~10kHzといった広帯域の振動加速度センサーを選定することが有効である.実際の現場での例だが,対象機器から振動データを取っているのにもかかわらず,安価な1kHz程度までの振動センサーを用いて検知したい現象を周波数帯域が足りずに取りこぼしている,というもったいないケースも散見される.最初の検証段階ではなるべく帯域の高いセンサーを選定し,必要な帯域を見極めた上で,運用に向け必要十分なスペックに落としていくというアプローチをとることが有効である(図9).
5.2 AI
活用すべきデータとしては,振動やトルク,温度などの時系列データである.通常と異なる傾向が見えてきた場合に,異常発生の兆候を検知しメンテナンスすることでチョコ停・ドカ停の発生を未然に防ぐことができる.効率的な設備管理を実現することでメンテナンスコストを大幅に削減し,急な設備停止による生産性の低下を回避することが可能だ.
予兆検知においては,教師なし学習でAIが獲得した特徴表現とどれほど乖離しているかを評価する手法を用いる.これにより,未知の異常データが入ってきても正常データがあれば対応できる.例として工作機械の工具劣化度推定が挙げられる.劣化度推定では,異常検知でも述べた前処理を振動データに適用した後,正常状態を学習させた1D Convolutional AutoEncoderを使い異常値を算出し劣化状態を推定する(図10)。
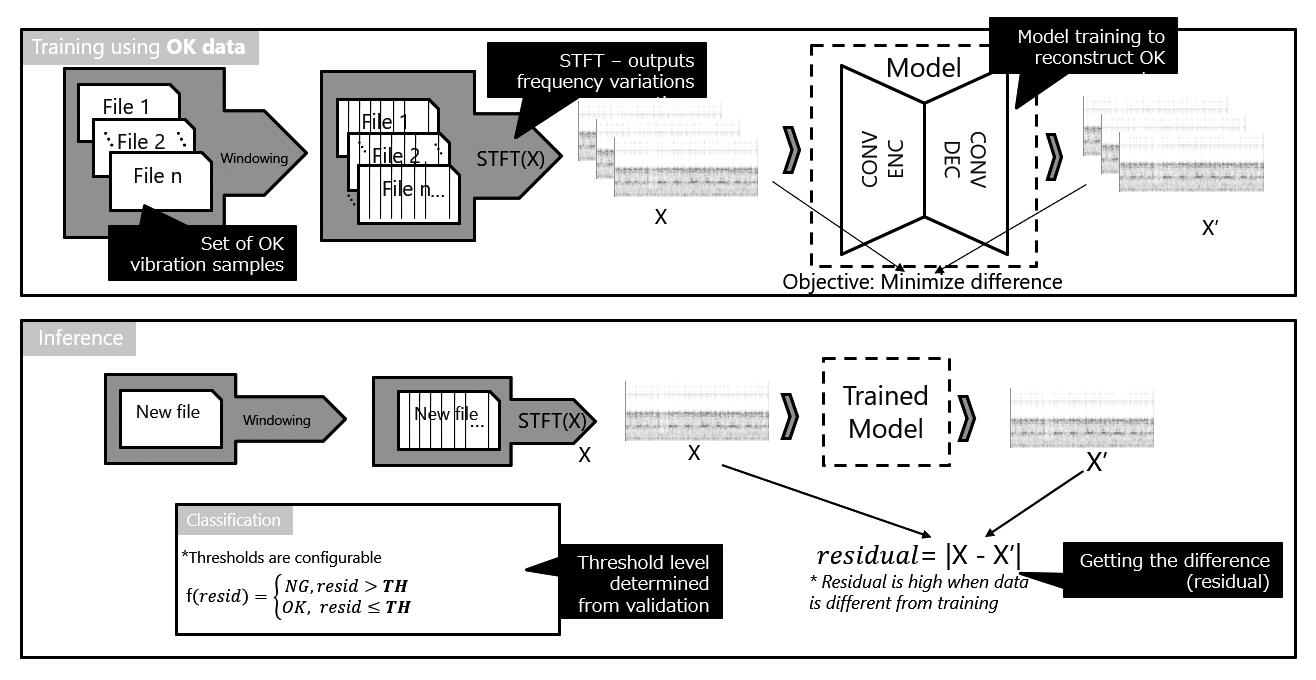
図10 1D Convolutional AutoEncoderを用いた劣化状態の推定
また別の例では,大型設備の予兆検知が考えられる.この場合,トルクや温度など振動データ以外の時系列データを活用することが多い(図11).ある一定期間内のデータを使って,次の一定期間内のデータを予測する回帰モデルを利用する.もしAIが予測した値と実際の値との差分が徐々に大きくなってきた場合,何らかの異常につながる現象が発生したと見なすことができる.モデルの種類としては,ARIMA(Autoregressive IntegratedMoving Average),AAKR(Auto-associative Kernel Regression),LSTM(Long short-term memory),FCN(Fully Convolutional Network)などがある.FCNは時系列データの分類に利用できるが,アーキテクチャの一部を変更することにより回帰モデルとして使用可能だ.
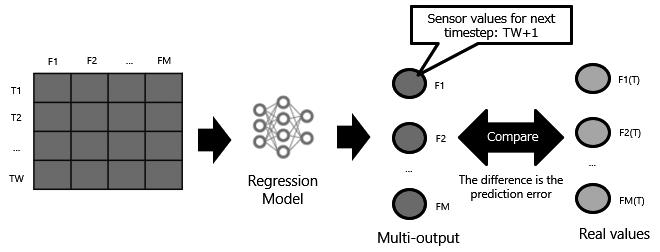
図11 トルクや温度などの時系列データを活用した大型設備の予兆検知例
6.ソリューションの紹介
最後に,マクニカが取り扱うソリューションについて二つ解説する.
6.1 スマートセンサーゲートウェイ“SENSPIDER”
SENSPIDER(図12)は高サンプリング対応(最大48kHz)のため,先に触れた広帯域振動センサーなどをはじめとする高精度なアナログセンサーデータを最大8chまで収集可能で,さらに,ユーザーカスタムアルゴリズムを実装(プロセッシング機能)することもできるので,判定・推論まで実施可能だ.SENSPIDERを開発した背景として,広帯域振動センサーを活用した場合のシステム構成が一般的に複雑・高額になりがちで,実証実験止まりの構成になりがちという点である.データロガーやPLCを活用するための構成の場合,センサーの種類に応じて専用のIOスロットを用意する必要がある.特に,広帯域振動センサーを接続したい場合はIOスロットに加え,外付けアンプや,センサー駆動用電源が別に必要となる.さらに,判定モデルや前処理などのアルゴリズムを実装する場合は別にコンピューターが必要となり,あっという間に数十万後半の大がかりなシステムとなってしまう.SENSPIDERはこれらすべて必要な機能を1BOXに集約しており,制御盤にもすっきり収納可能なサイズのためCBM機能の運用を想定した最適なハードウェアである.
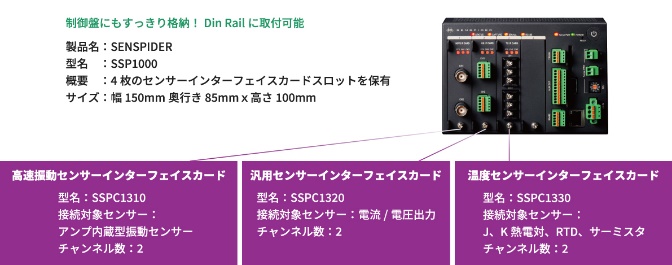
図12 スマートセンサーゲートウェイ SENSPIDER
6.2 AI運用サービス “Re:Alize.macnica.ai”
マクニカでは様々な業界における異常検知案件の実績をベースとしたAIモデルのライブラリを用意している.例えば先程説明したAutoEcndoderなどである.弊社データサイエンティストがお客様の実現したい内容やデータの質,傾向に合わせ最適なアプローチを適用し分析を行う.スクラッチでAIモデルを開発しようとすると莫大な費用がかかり,さらにそれが使い物になるかどうかはある程度の予算と期間を投じないと分からないという課題に対し,本サービスを活用いただければ効果検証までの費用,期間を大幅にミニマイズすることができる.さらに効果が見込めればそのまま運用までお使いいただくことが可能だ.その場合は運用後も必要となるAIモデル管理用のクラウド環境(精度監視,再学習,バージョン管理)を提供する(図13).
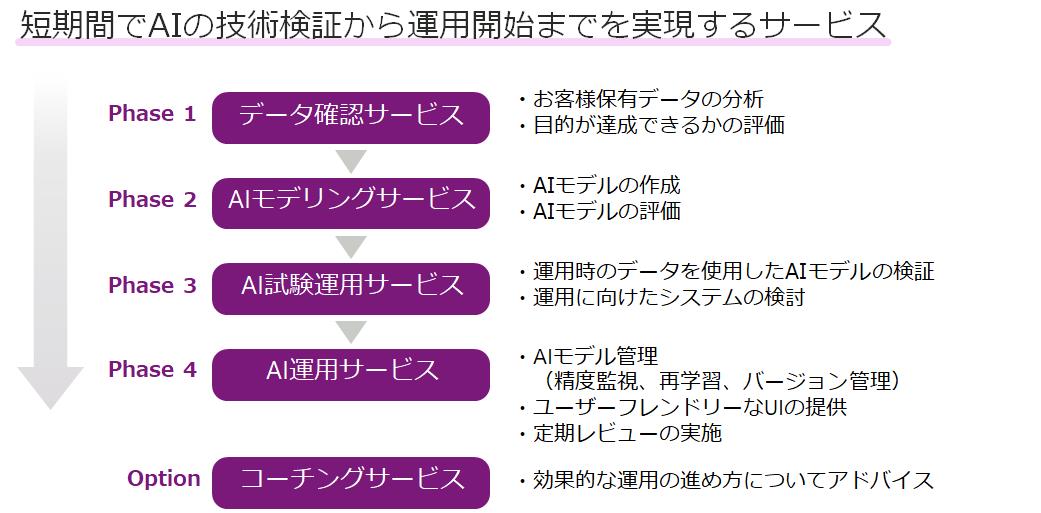
図13 Re:Alize.macnica.ai
まとめ
市場の動向からシステム構築のポイントを中心にお伝えした.実用化に向けたテーマが増えてきている中,少しでも手戻りなくシステム構築を進めるため最初の課題設定が重要である.
- 最初に導入効果を慎重に見極める
- 最初から完璧なシステムを目指さず正常データの活用から開始し運用の中で精度を上げていく
- メカ/回転機構の劣化・異常検知には広帯域振動センサーが有用
弊社ではCBMシステム構築に特化したチームがあり,センシングからAI,運用システムに至るまで幅広くサポート可能である.もしご興味があればお気軽にお問合せいただきたい.