工作機械や切削加工における切削油の使用について,油性切削油の利点や健康,環境,実利益的なコストについて解説する。
1. 工作機械や切削加工における切削油の使用について
近代的な工作機械やその切削加工では,以下のような適用に合った特別な潤滑油剤が必要である。
- 金属加工
- 油圧
- 摺動面
- 平軸受とローラーベアリング
- 高速スピンドル
- ギアーの組立て
12の主なドイツの工作機械メーカーへの調査によると,1台の工作機械には金属加工油以外に平均7種類の潤滑油が使用されている。これだけの潤滑油を使用することは多大なコスト要因であり,高額な在庫コスト,油剤使用の複雑性,廃液処理費が発生するだけでなく,油圧油や摺動面潤滑油がクーラントに混入するという問題を引き起こす。水溶性切削油を使用する場合は,混入する油圧油や摺動面潤滑油が液表面に浮き,水溶性切削油が空気に触れることを妨げ,バクテリアや酵母菌の成長を促進させる。これがプラスチックコートされた工作機械の摺動面を膨潤させたり,錆を発生させたりする。混入油を取り除くことに加えて,このような問題がさらにメンテナンスコストを増大させるのである。
企業化調査と実際の経験では,切削油を使用すると,機械への充填と消火装置の設置でイニシャルコストは高くついても,メンテナンスに掛かる費用と手間の顕著な低減でイニシャルコストが数年で完全にカバーできることを次の例が示している。
2. 油性切削油と水溶性切削油の比較
ハイテクエンジン工場における油性切削油と水溶性切削油の比較について以下に述べる。
1994年,ダイムラークライスラー社のドイツ,バッドカンスタットの新設エンジン工場では1日に1,100台のメルセデスベンツエンジンの製造が計画されていたが,新しい要求は1日当たり1,750台の生産量に増加させるというものだった。ドイツでエンジン製造が始まってから,コストを削減する技術がいくつか考案されてきた。水溶性切削油の代わりに油性切削油の使用が採用されたことも,その内の1つである。
最近では,加工油は生産環境面,化学物質使用における法律,水質保護法,労働安全法やリサイクル法などにおいて政府の規制が大きく関わっている。ダイムラークライスラー社のウンテルタークハイム工場油剤部門の長であるアルノキーヘル氏によると当初より水溶性切削油の使用拡大が難しいと分かっていた。1番の問題は2級アミンと反応しニトロソアミンを生成する亜硝酸塩である。そして微生物のせいで,水溶性切削液が腐敗してしまうのも,もう1つの問題である。この問題を解決するために殺菌剤を使用するには熟練者の判断と,多くの経験が要求される。そして,取り扱いの注意に従わなければ,重大な皮膚炎症や排水問題が起こる。
このため水溶性切削油が採用される量が減少すると予測される。油は可燃性で,空気と触れて爆発性の混合物を形成することもある。従来型の鉱物油のものは,粘度が下がれば急速に蒸発して低温で引火する危険性が増す。爆発の危険性とオイルミストの発生の傾向や沸点,引火点との間には相関関係がある。引火点が上昇すれば,またミストの発生や蒸発の傾向が少なくなれば,火災の危険性は低下する。これを解決するのは,特殊な低揮発性のベースオイルとアンチミスト添加剤を組み合わせて配合することであり,この特殊なベースオイルは,通常のベースオイルと比較すると蒸発量が10%程削減できる。この切削油は現在,バッドカンスタット工場のすべてのシステムと作業場で使用されている。
油性切削油と水溶性切削油を比較する主な要因は経済的知見である。もちろん,油性の方が,85%の水と希釈する水溶性切削油を使用するよりもイニシャルコストは高くつく。しかし,油性切削油を使用しても,コストを大きく低減する要因がある。フックスとメルセデスベンツは共同で,新しい低ミスト・低蒸発の油性切削油の開発,テストを繰り返した。結果,従来の製品と比べて,工具寿命は同じレベルを維持したまま,蒸発やミストのエミッション量は10%以下に減った。
この工場では,粘度が10mm2/s(@40℃)の油性切削油と,46mm2/sの油圧油を使用することが決定された(写真1)。
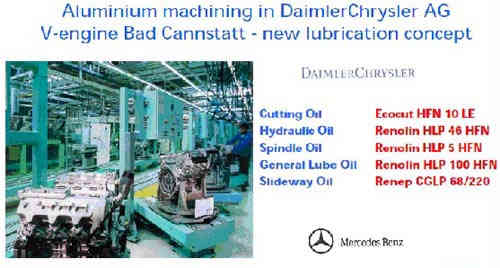
写真1 バッドカンスタットの新設エンジン工場の模様
油圧油が切削油に混入し,切削油の粘度を上昇させるが,製造工程では切削油の粘度は15.5mm2/sの限界値まで耐えられた。また,金属加工油の粘度は調整が可能である。油圧油・潤滑油を切削油と同じ種類のものを使用することで,在庫コストや機械と切削油メンテナンスコストを削減することができた(図1)。
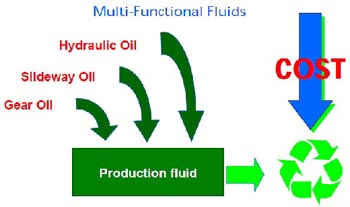
図1 切削油と同じ種類の潤滑油を使用することでメンテナンスコストの低減が可能
3. 健康,環境,実利益的なコスト
「作業員の中には水溶性切削油へのアレルギー体質者がいて,作業場でもはや働けないことがありますが,現在多数の従業員が我々の工場地区に戻ってきています。これが一番の成功です。」と資材管理技術部のハインツノワク氏は言う。切削油を油性に代えてからは,切削油が原因で起こる皮膚の炎症やアレルギー反応の報告はなく,工場ではオイルミストや蒸発の問題もない。低エミッションのオイルを完全に密閉した機械と中央制御の抽出システムで使用することで,エミッション量が10mg/m3の限界値よりはるかに低くなった。
水溶性切削油は汚染廃棄物として扱われるため,処理費用が高くつく。油性は水に浮くので簡単に除去できるが,エマルジョンの場合は,水と油が混合しており,自然分離は効果的に行えない。エミッション量が少なければ,火災の危険も減る。工場が稼動して3年間で,炭酸ガス自動システムを使用しなければならないような火災の発生は一度も報告されていない。
それから4年経ったが,切削油の寿命が長いため,更油は必要とされていない。ワークピースを遠心分離機に掛けた時に切削油が付いて出たり,洗浄工程で切削油が持ち出されたり,工程で起こる持ち出し量を補うために継ぎ足しさえすれば十分という状況になった。「すべての要因を考慮すれば,事態はさらに明らかになります。切削油の寿命が延び,油が除去しやすいため,洗浄工程で使用する洗浄水も長期間使用することが可能です。機械に腐食は起こらないし,機械の耐久性が向上しました。工場の衛生性が向上し,作業員の肌荒れの問題も改善できました。これらすべてがプラスの要因です。」と,アルノキーヘル氏は言う。
4. 油性切削油の利点
フックスは油性切削油が水溶性切削油と比較し,以下の利点があることを認識している。
- 油性切削油は微生物の攻撃の問題がないため,製品に殺菌剤を配合する必要がない。また,pH管理も必要ない。
- 油性切削油は適切に管理すれば,半永久的に使用可能である。他方,水溶性切削油は数週間,数ヵ月で更油が必要である。
- 油性切削油は更油が必要なければ,機械の休止時間もゼロである。
- 廃棄処分量は水溶性切削油よりも少量で,コストも少ない。
- 油圧油や摺動面潤滑油,スピンドル油に切削油と同じ種類の製品を使用すれば,コストが低減し,切削性に有害な影響を与えない。
- 油性切削油は水溶性切削油よりも管理が非常に容易である。つまり,労働コストが削減できる。
- 摩擦抵抗力を強めた精製ベースオイルを使用した油性切削油は工具コストの低減・削減に大きく貢献する。油性切削油を使用することで,工具寿命が10倍アップした例もある。
- 送り速度の早い加工では,油性切削油の方が水溶性切削油よりも仕上げ面精度が優れている。
油性切削油を使用する際,唯一のデメリットは多量の加工熱が発生することである。超硬ドリルの製造時,センタレス研削,ホーニング加工時のような場合には加工熱が発生する。これらの工程を油性切削油で行う場合,粘度はできるだけ低い方が良いが,火災の危険性と環境上の問題が高まる。この問題に対する解決策は,高発火温度を有し,蒸発性の低い低粘度の新規ベースオイルを使用することである。フックスは水素化分解したベースオイルや純エステルオイルを配合したLE(LE=Low Evaporation 低蒸発性)製品シリーズを1990年代始めから揃えている。純エステルオイルの代替品としては,水素化分解したベースオイルやエステルオイルを効果的に置き換えた混合物をベースとした特殊製品がある。
フックスはすべての製造工程を担当する全エンジニア,全環境コストエンジニアの方々に,LE製品に関するフックスの世界での長年の経験と,製品の利点を紹介している。フックスの技術と製品は,日本では奈良県北葛城郡王寺町に本社を置くマコトフックス(株)が三重県伊賀市と千葉県白井市の工場で製造し,市場に紹介している。
<参考文献>
*1 フライラー,Dr.ホーナー,トロマー,「ダイムラークライスラー社金属加工における水溶性エマルジョンに代わる油性切削油」ミネラルオイルテクニック マガジン,'00.9
*2 Dr.ホーナー,「各作業場での代替品」デアベトリーブスライター マガジン,'00.2
*3 Dr.ホーナー,「エマルジョンに代わるオイル」オートテクノロジー マガジン,'01.3
*4 アルノキーヘル,「加工油使用のコスト調査」メルセデスベンツAG 内部レポート,ZWT/PS 部,'96.10