はじめに
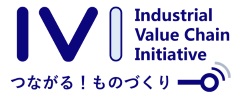
図1 IVIロゴマーク
IVIは,デジタル化社会に対応した次世代のつながる工場を,企業や業界の枠を超えて実現するための組織で,会社の規模や地域や国や文化の違いを超えて「つながること」で価値を創出することを目的とし,協調と競争のバランスがとれた持続可能な発展のためのエコシステムづくりを先導している.西岡 靖之 氏(法政大学 デザイン工学部 教授)を設立発起人の代表として,日本機械学会生産システム部門の「つながる工場」分科会が母体となり設立されたIVIは現在,226社・団体,594名が所属している.IVIの設立の背景や活動概要については,本誌「潤滑経済」2016年7月号(No.615)で紹介しているので,参照されたい(IoT時代の新たなものづくりを目指すインダストリアル・バリューチェーン・イニシアティブ).
IVIでは課題別にワーキンググループ(WG)が作られ,それぞれの取り組みテーマの実証実験を行っている.2017年3月に開催された「春の公開シンポジウム」では,25のWGが成果発表を行い,8つのグループが保守・保全を対象業務とする取り組み課題を発表した.
本稿では,保守・保全に関する8つのWGの中から,潤滑管理やメンテナンス技術の伝承など,広く製造現場で関心の高い,工作機械の潤滑油漏れをテーマにあげた「設備稼働データによる保守/保全の効率化」と,製造現場での保全ノウハウやスキルをナレッジ化する「保全ナレッジ活用による保守/保全の効率化」について紹介する.ナレッジ化では,設備の不具合情報を分類し,必要な時に症状や原因などの情報を取り出せるようにしている.
それぞれのWGでファシリテーターを務める「設備稼働データによる保守/保全の効率化」の福本 勲 氏(東芝デジタルソリューションズ)(写真1)と,「保全ナレッジ活用による保守/保全の効率化」の幸坂 知樹 氏(電通国際情報サービス)(写真2)に,現場でのIoT活用の実際についてお話を伺った.
1.WG「設備稼働データによる保守/保全の効率化」
1.1 本WGが目指したこと
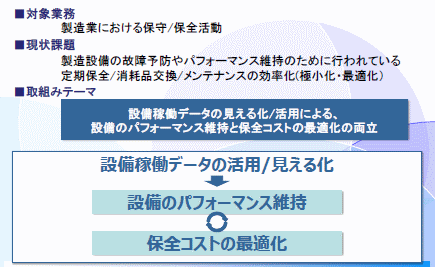
図2 WG「設備稼働データによる保守/保全の効率化」が目指したこと*1
1.2 「As-Is(現状)」の変革ポイントと「To-Be像(目指す姿)」
本WGは,稼働情報/センサー情報の収集,トレンド状況の可視化,アラート情報の通知などの仕組みを実現することで,異常を早期に(影響範囲が大きくなる前に)発見し,保全計画調整の柔軟性を確保するとともに,被害範囲の拡大を抑制し,対応工数/時間の削除につなげる.実証実験では大型工作機械の潤滑油漏れを取り上げた.図3では,As-Is(現状)として現在の課題を3つ,To-Be(目指す姿)として目指す姿を3つ挙げている.
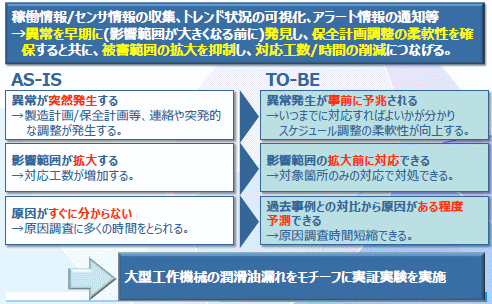
図3 変革ポイント(事前の予兆,拡大前に対応,原因の予測)*1
―大型工作機械の潤滑油漏れをモチーフに選ばれた理由を教えてください.
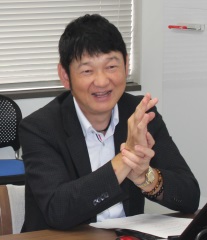
写真1 福本氏
―現状での問題点や影響範囲と,目標とする姿について教えてください
福本:現状における問題点は3つあります.まず,異常が突然発生した場合,製造計画や保全計画などに関する連絡や突発的な調整が発生する点が挙げられます.事後に対応した場合,製造する製品の納期などに影響を及ぼす場合も出てきます.事前に異常発生の予兆を把握できれば,製造計画の中に事前にメンテナンス計画を組み込み,製造計画への突発的な影響を極小化できます.2つ目は,工作機械内の他の部位に,漏れた潤滑油が付着して影響範囲が拡大してしまい,対応工数が増加することです.影響範囲の拡大前に対処できれば,潤滑に関する部品交換やメンテナンスのみの対応で済むため,他の箇所の清掃や対処が不要になります.3点目は,油漏れの原因がすぐには判明せず,その調査に多くの時間を取られていることです.
過去の事例との対比から原因を予測できれば,対処すべき作業や交換すべき部品などを予測できるため,調査のための時間や工数の削減と製造計画への影響の極小化が可能です.最後の原因調査の点に関しては,幸坂 知樹 氏がファシリテーターを務めるWG「保全ナレッジ活用による保守/保全の効率化」で実証実験を行っていました.
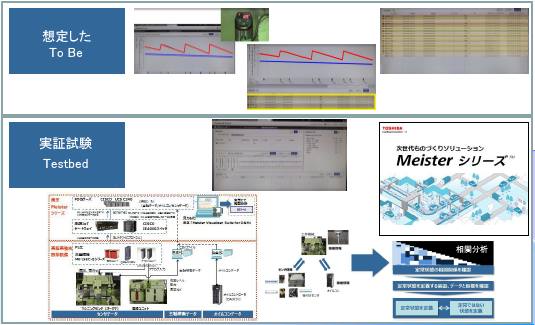
図4 実証実験の全体図*1
1.3 本WGの実証実験の内容
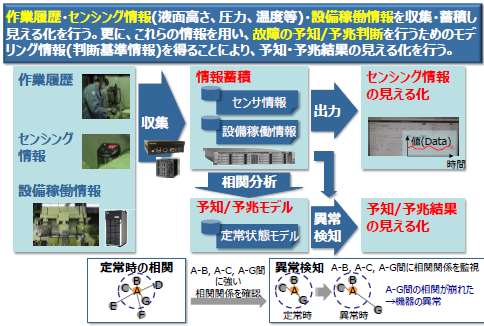
図5 実証実験の構成*1
福本:実験では,まず20~30年以上前のマシニングセンタに複数の後付けセンサーを設置し,作業履歴,センシング情報,設備稼働情報を収集しました.センシング情報(液面高さ,圧力,温度など)と設備稼働情報を使って,機械の状態をデータで閲覧できるようにすることで情報を「見える化」しました.また,センシング情報と設備稼働情報で相関分析を行い,予知・予兆モデル(定常状態モデル)を構築しました(図5).相関分析では,正常に稼働している時に,液面の高さや温度,設備稼働状況など複数の情報がどのような関係にあるのかを調べました.作業履歴についてはWG「設備稼働データによる保守/保全の効率化」の相関分析では利用していませんが,過去の事例との対比から原因予測を行うWG「保全ナレッジ活用による保守/保全の効率化」にて活用しました.
―センサーでどのような情報を取り込んでいるのでしょうか.
福本:時刻や液面の高さ,潤滑油量といった情報のほかに,工作機械がどのように動いているかを計測するための主軸データ(ステータス,電力,電流など),どの程度オイルが冷却されているかを判断するための油温制御装置データ(入口油温,出口油温,電力,周波数,制御指令値など),そして潤滑ユニットデータ(圧力,油温など)やコラム温度といった様々な情報を,センサーで収集しました(図4参照).工作機械の稼働情報については自動取り込みと,PCを使っての手動入力があります.
―センサー情報や設備稼働情報を使った相関関係の定義の仕方について教えてください.
福本:今回は,実験期間中に異常発生がなかったため,異常が起きていない正常時(定常状態)の相関関係を明確にすることを主眼にしました.収集した情報を用いて,異常の発生していない定常時には,複数のセンシング情報の間の相関関係がどのようになっているかを確認し,「定常状態モデル」として定義しました.そうすることにより,定常状態の相関関係が崩れた場合を「異常発生」と判断・診断できます(図5参照).相関が強いとわかっているデータがあれば対象のデータを重点的に分析しますが,そのような知見のないデータの場合,および明らかに物理現象として相関関係の存在しないデータを除外した上で,収集したデータの全ての関係を総当たりで分析します.こうした相関分析は,設備の異常検知や製品の不具合発生の検知をはじめ,多岐にわたる活用が可能です.
―相関関係の作り方について教えてください.
福本:データ分析によって相関関係を見いだす場合と,専門家の知見を参照して定義するケースの両方があります.実験では,全データの相関分析を行っていますが,データの正あるいは負の相関関係を絶対値で見るべきなのか,それとも設備の稼働ON/OFF情報,例えば主軸の電流値がゼロであるか正の値かといったようなステータスが影響するのかといったことについては,設備の専門家などの知識と照らし合わせて確認し,モデル構築を行いました.例えば,ある値とある値の相関分析を行う場合,一方の値の増減量に応じて他方の値の増減量が変化する場合もありますし,一方の値がゼロorプラス値orマイナス値かだけによって,値の大きさに関係なくもう一方の値が均一に増減する場合もあります.今回,主軸の電流値と液面高さの関係は,後者でした.主軸の電流値がゼロでない場合(プラスの場合)はその値に関係なく,単位時間当たり一定量ずつ液面高さが減少するというものでした.また,今回の実験では同じ素材とパターンの加工方法を対象としましたが,被削材や加工方法ごとに,それぞれの定常状態のモデルが定義されます.
―相関関係を監視して異常を検知する仕組みについて教えてください.
福本:「設備稼働データによる保守/保全の効率化」,「保全ナレッジ活用による保守/保全の効率化」のどちらも,実証実験のプラットフォームには,東芝デジタルソリューションズの「次世代ものづくりソリューションMeisterシリーズ」(図6)を活用しています.「Meisterシリーズ」は,製造現場や市場で起きたこと・今起きていることを精密に把握し,デジタル空間上で状況を再現,状況に応じたリアルタイムでの最適化や,不良・故障の未然防止等を市場・現場の情報を使い高度に実現するプラットフォームです.「設備稼働データによる保守/保全の効率化」では,Meister Digital Twin上に日々蓄積された膨大な装置稼働データから,事象パターン分析手法を用いてその特徴を捉えました.この手法を用いた「事象パターン分析技術」は,メーカーである東芝の「ものづくり」におけるデータ分析・活用の知見に基づき,膨大なデータの中から不良や故障の「複合的な要因」を高速に導出することができる技術です.
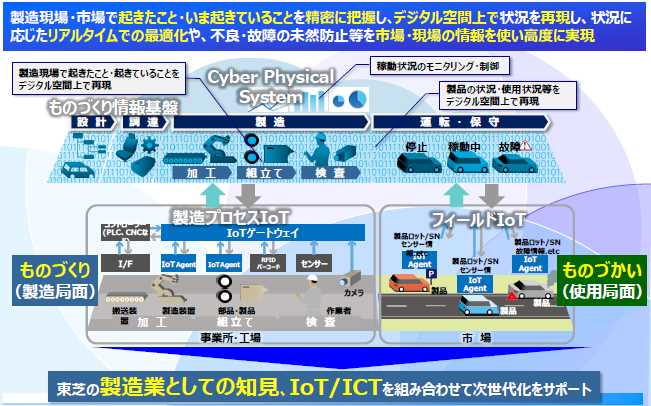
図6 次世代ものづくりソリューションMeisterシリーズ*2
―設備のパフォーマンス維持と保全コストの最適化の両立について教えてください.
福本:保全人員の育成コストなどを含めたトータルなコストが最適化されていくための取り組みとして兆候を捉えるモデルを作成し,それを元に過去事例から迅速に修理が行える概念検証を行いました.例えば,パフォーマンスを維持することだけに注視した場合,通常生産に不要な代替設備を用意しておいたり,保有する全ての設備の予備パーツを用意しておいたり,必要以上の頻度で必要以上に念入りな定期保全を行ったりといった対応を行うことが考えられます.しかし,そうした対応には必要以上のコストがかかることになりますので,コストを最適化しつつ品質や納期といったパフォーマンスを維持する取り組みが求められているということになります.この両立にはTBM(Time Based Maintenance)からCBM(Condition Based Maintenance)への変革がポイントとなります.データドリブンで故障の予兆検知をすることで,データに基づいた保全要員手配,保守部品の調達などが実現され,両立されていくものと考えます.
2.WG「保全ナレッジ活用による保守/保全の効率化」
次に紹介するWG「保全ナレッジ活用による保守/保全の効率化」の実証実験も,WG「設備稼働データによる保守/保全の効率化」と同様に,製造設備の故障予防やパフォーマンス維持のための,定期保全/消耗品交換/メンテナンスの効率化(極小化・最適化)を現状の課題として取り上げ,保守ナレッジ活用による変革に取り組んでいる.
2.1 本WGが目指したこと
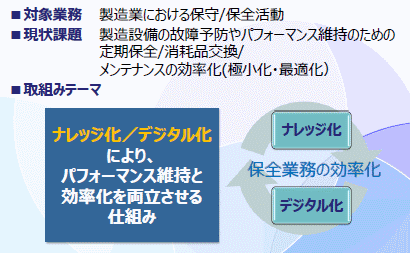
図7 WG「保全ナレッジ活用による保守/保全の効率化」が目指したこと*3
ナレッジ化では,過去の不具合情報を整理して,症状や故障部位,原因や対策などの情報をすぐに取り出せるようにし,デジタル化では,テキスト情報だけではなく映像情報なども活用する試みを行った.
2.2 ナレッジ化,デジタル化による「As-Is(現状)」の変革ポイントと「To-Be像(目指す姿)」
多種多様な製造設備に対する保守・保全業務を,保全ナレッジの活用による効率化を図ることを目指した.過去の事例をナレッジ化し,故障診断する,修理計画のリコメンドを行う,また,紙ベース,文字ベースの保全記録を映像,動画,図面などを組み合わせた記録としてナレッジ化することで保守・保全を効率化する.(図8)
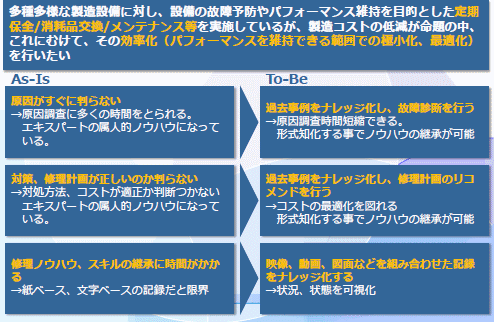
図8 As-Is(現状)の変革ポイントとTo-Be像(目指す姿)*3
―WG「保全ナレッジ活用による保守/保全の効率化」での多種多様な製造設備の故障予防やパフォーマンス維持の問題点や現場での課題などを教えてください.
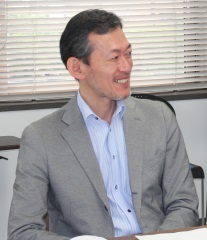
写真2 幸坂氏
―図8の変革のポイントのTo-Be像に,「過去事例をナレッジ化し,故障診断を行う,修理計画のリコメンドを行う,映像,動画,図面などを組み合わせた記録をナレッジ化による効率化」が挙げられています.期待効果などを教えてください.
幸坂:過去事例をナレッジ化し,故障診断を行うことで原因調査の時間短縮については,原因の複雑度によっても異なりますが,繁盛期の製造工場では数時間の設備停止でも大きな製造計画インパクトを与えることを考えると,原因調査の時間短縮による効果は非常に大きいと言えます.
過去事例のナレッジ化をし,修理計画をリコメンドすることで,現状では対策,修理方法がエキスパートの属人的ノウハウになっているものを,To-Beでは形式知化することでノウハウの継承が可能となります.また,故障の予測を含む事象に対して,どのような対処を行うべきかを,過去事例などから作業員に教示することができるようになります.
さらに,映像,動画,図面などを組み合わせた情報を利用して状況,状態を可視化することで,テキストのみの情報に比べ,作業者の間での理解や事象の共有,作業内容の伝達などが大きく向上します.
2.3 本WGの実証実験の内容
―保全記録のデジタル化・ナレッジ化の取り組みについて教えて下さい.
幸坂:本WGの実験では,紙ベースで残された保全記録のナレッジ化・デジタル化にフォーカスし,事象から原因特定を迅速に行うことを目指しました.保全記録のナレッジ化では,実証実験にご協力いただいた企業様の過去の不具合対応履歴をナレッジデータベースに投入し,不具合内容や原因箇所,機種,導入年次などで類似した不具合の有無や,複数ある場合には類似度がより高い順に結果を提示する可能性を実証しました.また,デジタル化では,クラウドベースのタブレットシステムの現場入力を試行し,入力データから過去の類似障害を自動で検索し,対応事例を提案できるようにしました.
ナレッジデータのエラーコードや部位,症状,原因,対策といった整備した辞書に対して,入力データの中の言葉が同義語や類似語を含め一致したものを抽出しています.ナレッジデータは過去の保全履歴の情報を元に作成しておりますが,元の情報は,記述方法が標準化されていないため,同じ症状や部位であっても表現が異なっているケースが多々あります.また,1つの文章内に症状や部位などが混在して記述されており,活用が困難な状態でした.これらの課題に対し,辞書を用いることで,表現の揺れを吸収するとともに,症状や部位などの切り口で情報を抽出できるようにしました.そのことにより,「何が(部位)どうした(症状)」を入力データとして,過去の情報を検索できるようにし,その検索結果として対応方法をレコメンドとして提示できるようにしました.
―保全記録活用の現状と改善ポイントについて詳しく教えていただけないでしょうか.
幸坂:実証実験を実施した工場では,マシニングセンタに関する過去10年分の保全記録が紙ベースで残っており,過去に故障が起きた際の箇所,その時に採った対策についてExcelデータ上で確認できる状態でしたが,保全作業の効率化への活用は限定的でした.それは,同じ部位のことを示していても記録者によってその表現が異なっていることが多く,テキストを読み返すだけでは,どの箇所が現象・故障部位・対策について書いてあるのか,特に若手にとって判断が難しいことが理由として挙げられます.(図9)
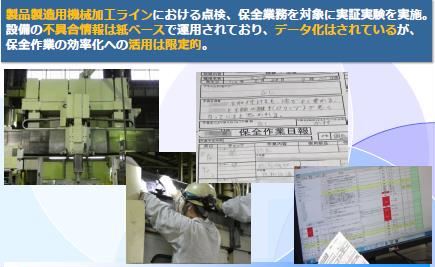
図9 紙ベースによる保全記録*3
テキスト中の表現を統一して辞書化を行い,故障部位の写真・異音の音声データ・交換方法の動画をテキストと一緒に残し,他のセンシングデータやスケジュールと組み合わせれば,事象から原因特定を迅速に導き出せる,ハイレベルな保全記録になります.数値化されたデータ,起きた事象,対処方法.これら3つが揃ったデジタルの保全記録を現場でどのように実現できるのか,そのプロトタイプを考え,現場でその効果を推定しました.(図10)
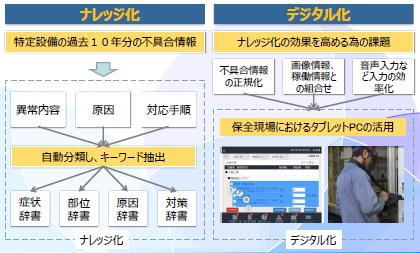
図10 ナレッジ化とデジタル化*3
―過去の事例を活用して,どのように原因予測を行うのでしょうか.
幸坂:原因がすぐに判らない,対策・修理計画が正しいのか判らない,修理ノウハウやスキルの継承に時間がかかるといった課題に対し,ナレッジ化とデジタル化によって保全業務の効率化を目指しました.ナレッジ化の作業では,特定設備の過去10年分の不具合情報を異常内容,原因,対応手順で自動分類した上で,キーワードを抽出します.その上で,症状辞書,部位辞書,原因辞書,対策辞書を作成し,症状,経過年,設備詳細,部品などに関する情報の組み合わせから,異常発生の傾向分析を実施しました(図11).こうした過去の不具合情報や辞書情報は,不具合が発生した場合に,ナレッジデータベースから抽出することができ,故障診断や修理計画のリコメンドとして作業員が活用できます.例えば,「症状」と「経過年」の組み合わせで調べれば,「油漏れはおよそ10年周期で件数が増加.原因は部品不良,劣化,ゆるみであることから経過年に応じた点検の強化などが不具合の未然の防止につながる可能性がある」とった傾向分析ができます.(図12)
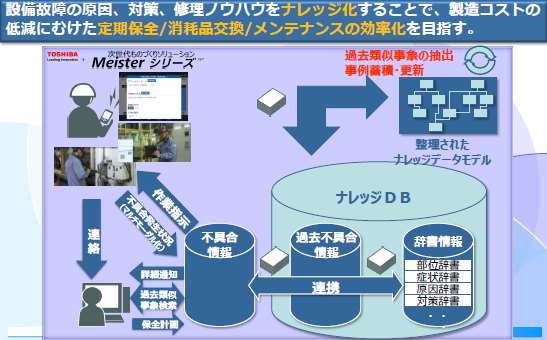
図11 過去事例を活用した原因予測*3

図12 過去事例の抽出による傾向分析*3
3.実証実験を振り返って
―実証実験を振り返って,今回の成果や今後の課題などについてお聞かせください.
福本:今回のWG「設備稼働データによる保守/保全の効率化」の実証実験により「ヒストリカルな情報(過去から蓄積された履歴情報)の見える化・活用」が保全現場に貢献できることが確認できました.また,修理計画や生産計画の柔軟性確保,影響拡大前の対応,作業内容・手配の導出といった保全作業をスムーズに実現できる可能性が高いことも確認できました.そして,20~30年以上前の工作機械への後付けの仕組みの導入により,その情報を収集し,設備のパフォーマンス維持と保全コストの最適化を両立できる可能性を確認できました.実証実験にご協力いただいた企業からも「自分たちの仕事の効率化,技能伝承に効果がある」とのコメントをいただいています.
幸坂:WG「保全ナレッジ活用による保守/保全の効率化」では,紙の保全記録を中心としたやり方がナレッジの継承を妨げているという仮説に対し,ナレッジ化・デジタル化の効果を確認できました.テキスト情報以外に画像や音声などの情報を付加したマルチモーダル化が情報の伝達に効果をもたらすことも分かりました.そして,ナレッジの見える化により全体的な傾向が容易に把握できることを確認し,任意の切り口による2軸チャートの見える化で容易に情報群の傾向を把握でき,保全作業の改善に活用できることも確認できました.今回の実証では,保全データのナレッジ化・デジタル化を実業務で使用するには至りませんでしたが,実証実験現場の保全業務担当者からは,「実現できると仕事が楽になる.新人の戦力化,活躍までの期間短縮につながる」といった声や「監視・予知・予防によって生産計画に影響を与える機械停止が少なくなる」といったフィードバックをいただきました.他にも以下のような様々なフィードバックを得ることができました.
- 現場では突然不具合が起きることがあり,日常点検時に限らず,「いつでも使える」仕組みであることが必要.
- 修理は過去の知見と経験に頼ることが多いが,知見や経験がない場合も考えると探索の仕組みの導入は効果がある.
- 原因から構成と交換部品の型式,納期,価格などを参照できるとさらに良い.
- 現在は経験とスキルがないと動けない.若手や新人は言葉や文字の説明のみでは理解できないケースも多い.写真,動画,音声,構成情報,部品調達との連動ができるとさらに業務効率が向上する.
福本:高度熟練労働者の世代が今後失われていくと言われる中,新しい技術を活用することで日本の現場力を維持・継承することが必要だと私たちは考えています.
―本日はありがとうございました.
<参考文献>
*1 IVI公開シンポジウム2017-Spring- WG 2L01-1発表資料:設備稼働データによる保守/保全の効率化
*2 IVI公開シンポジウム2017-Spring- 発表資料:次世代ものづくりソリューションMeisterシリーズ(TM)
*3 IVI公開シンポジウム2017-Spring- WG 2L01-2発表資料:保全ナレッジ活用による保守/保全の効率化