はじめに
生産設備機械における潤滑管理の目的は,故障を先取りした経済効果を高めるための科学的評価による管理手法を目指すことである。そのためには,トライボロジー技術を高め,資質と将来を先取りしたムリ,ムダ,ムラのない潤滑油の汚染測定,解析技術,劣化診断の傾向管理を踏襲した考え方と実践による防止である。以下で内容を紹介する。
1. 潤滑油管理と汚染・劣化診断の目的
生産設備の稼働を理想的に維持することは故障要因を先取りする保全活動として機械機構部の稼働を的確に保守する潤滑管理活動である。この潤滑管理の目的は,使用する潤滑油の適正油の選択と汚染や劣化を監視,診察し,常に適正な潤滑状態を保つための監視診断である。その主なる活動は潤滑油の汚染や劣化状態を観察・分析して機械稼働の異常な動きや負荷に伴う初期故障を先取りする診断といえる。
特に設備機械の稼働に伴うトラブル発生状況(表1)を見ると,潤滑油の汚染と劣化に関わる問題点を解決することが課題であり,日常における潤滑管理を実施・診断することは,機械稼働状態の保守に有効である。
表1 油圧装置のトラブル原因と故障発生率
|
2. 潤滑油,作動油の汚染・劣化の特長
潤滑油の汚染防止,劣化診断を管理するために要求される基本となる技術には,機械要素と機構の材質や摩擦,さらには使用する潤滑油剤の化学物質などの相性と潤滑性能を習得する必要がある。
特に,機械機構部に含まれている金属や合金材ならびに樹脂系の化学物質は潤滑油に含まれている各種の添加剤の化学物質との整合性を考えなければならない。なぜならば,お互いに化学反応を促進させる性質の場合,金属表面の変色・劣化,材質組織内部への亀裂・損傷を発生させるからである。
また,油中異物が増えると潤滑油の汚染や劣化の促進を招き,潤滑油の性能劣化はもとより,異物によるパッキンシール面への膨潤低下や部分損傷による漏洩の原因や設備故障を誘発する原因となる。
さらに,設備機械が稼働する環境面には空気中に含んでいるガス,液体,固体の物質は小さい粒子であるため潤滑油に浸入されやすい状況にあるため,機械周囲にあるチリ,ホコリ,湿度,温度,光線や職場で使用している化学物質などは潤滑油剤の劣化を促進する要因が多い。
これらを含め,潤滑油主成分の炭化水素化合物が汚染され,過酸化物を生成ならびに酸化・劣化を促進させる環境における要因と項目の酸化機構は,次のような系統にまとめることができる(図1)。
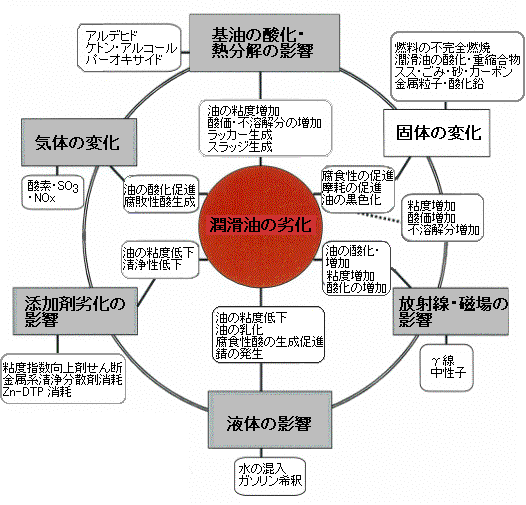
図1 潤滑油の酸化劣化要因と機構図
3. 潤滑油・作動油の汚染物は機械損傷の道しるべ
設備機械の動脈ともいえる潤滑回路を通る潤滑油や作動油が劣化すると,油中にスラッジや酸化劣化物などを生成し,潤滑性能が低下する。そして,清浄なオイルを必要としている機械の摺動面に損傷トラブルを発生させ,その機械摺動部分からは金属摩耗粉が多量に発生し,それぞれの摺動する機構部分に浸入してダメージ的な損傷を広範囲に発生させることになる。特に,潤滑系統の場合は軸受や歯車などの摺動する面を継続的に損傷させ,急激に機能低下を起こす破壊的損傷に進行することが多い(表2)。
表2 油中異物と油圧機器の損傷要因一覧
|
また,油圧装置においても油圧ポンプの損傷に起因させ,ベーン型とギヤ型では軸受摺動面を主に,ピストン型はピストンやヘッド摺動面など,形式によって異なった損傷や焼付き現象を発生させる。
制御弁では,バルブ内のスプール摺動面に融着し,動作遅れやかじり現象などの損傷障害を起こし,故障原因を判断しにくい場合がある。したがって,潤滑油や作動油内に混入した汚染物からトラブルを防止するには,油中に浮遊している阻害要因(油中異物)を回路内から早期に除去することが望ましい。それには使用している潤滑油・作動油の汚染度と劣化(性状)状態の定期的な測定管理を実施して,使用領域範囲状態にあるかを把握する必要がある。それは,設備機械や油圧装置を設置した初期運転から生産に伴う継続稼働に至る,機械の一生涯において性能維持と生産保障をするためにも潤滑油・作動油の汚染度と劣化(性状)状態を一定のクリーン範囲に維持することが油剤の寿命延長ならびに設備故障の予防になる。
4. フィルトレーションでクリーン範囲を維持
潤滑油・作動油は使用することで環境面と高温によって,自らも化学反応を起こして劣化物や汚染物が増加し,油中に異物(固形物,半固体,ゲル状)として存在,堆積する。
この油中にある異物の量を把握する測定方法には,体積,重量,粒子,金属系,化学物質など自動計測器によって数値化することができる。そして,カウントしたデータをJIS,NAS,ISOなどの規格をもとに使用領域の管理幅を定め,判断する方法などの自主管理を行う。
特に実施面では,使用領域ラインに近づいた時のアクションと使用範囲を超えた場合の計画・緊急措置方法は設備保護の面からオイルの再生処置対策が必要となる。オイル寿命を延長させ,機械機構部の回しやすさを継続的に保つ方法として,油中にある異物を安定的に除去する大きさを定め,フィルタに表示されているろ過粒度値を選定,捕捉量のよいフィルタを取り付ける方法がある。この方法は,オイルの流れを利用して自動的にフィルタの表面で除去し,油中の汚染物をろ過してオイルを清浄化するものである(図2)。一般的には,潤滑回路内の要所に設けて自動的に浄化するラインフィルタ(図3),タンク内におけるマグネットによる分離,バイパス回路による浄油機などの油中異物の性質に合わせた浄化方法を施すことがトラブル予防になる。
しかし,ラインフィルタろ過精度は油中異物の微小な粒子を通過させ,ろ過粒度の許容値より大きな粒径がフィルタ捕集面に蓄積して目詰まりをするため,定期的に点検を行い清掃やフィルタ交換が必要とされる。
また,フィルタ交換だけでは潤滑油,作動油の汚染と劣化が回復したわけではなく,捕捉した異物の発生源を確認しなければ設備故障を再発,拡大を招くことになるのでフィルタ捕集面に蓄積していた汚染物がどのような物質であるか見極める必要がある。
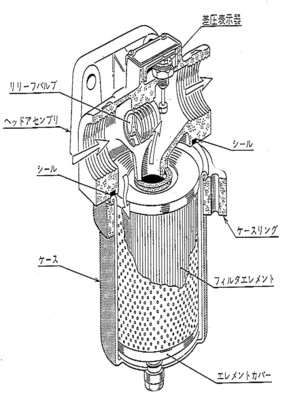
ラインフィルタ概略図
1.公称濾過粒度:フィルタのメーカーによって任意に示される値
2.絶対濾過粒度:フィルタを抜けた最大径によって示される値
3.濾過比率(ベータ値,βx値):次式によって示される値
―高いベータ値―
図3 フィルタの設置箇所
|
5. 汚染・劣化管理に伴う診断機器の種類と特長
潤滑油・作動油の汚染・劣化状態を把握するには,測定器を活用しての異物の大きさ・数量・重量・材質・形状・波形など特徴を数値化し,また顕微鏡や写真で実物観察する方法で,汚染物の先取り診断することが設備機械の異常状態個所の早期発見につながる。
具体的な方法としては,異物の総合評価,個別測定,物質測定に区分し,その中から固体,液体,気体,生物別に分けてから必要な測定方法を選択(表3)することで確かな汚染状態の把握ができ,結果として確かな考察と解析に伴う診断ならびに有効な対策へと導きやすくなる。また,固形物測定方法であるミリポア分析,微粒子係数測定,フェログラフィ分析,金属などの物性を測定する蛍光X線分析,ICP発光分光分析,油剤の酸化劣化,化学物質確認測定法である赤外線吸収スペクトル分析測定など,それぞれの測定装置ともに長所もあれば短所もあるため,測定機器の原理や欠点,注意すべきことなどについての知識を習得しなければ,確かな診断と対策につなげることはできない。したがって,潤滑管理者は測定方法別の長所と短所(表4)を理解する必要がある。
表3 潤滑油・作動油の汚染度測定ポイント
|
表4 潤滑油・作動油の汚染度診断機器の特長
|
6. 潤滑油の汚染・劣化の傾向管理とその評価
測定器で油中の異物は目的別に計測し,その数値が傾向管理で正しく評価するためにも試料油の採取方法と作業内容は大切な診断評価の一歩である。注意点として,クリーンな容器と採取機器を使い,周囲からの異物が絶対に混入しないようにする気配りと注意力で作業することが要求される。潤滑油の汚染・劣化を数値化する測定は性状(色相,粘度,全酸価),油中異物(ミリポア分析,ISO・NAS),劣化状態(IR分析),金属摩耗粒子(フェログラフィ分析)などがあるが,診断に必要性が発生した時点で測定項目のステップを拡大する。また,測定器によって得られた数値を傾向管理表に転記する上で肝心なことは,それぞれの項目ごとの目的が見える管理(図4)になっていると,潤滑油・作動油の汚染と劣化状態ならびに機械の摺動部に損傷状況が把握・検証されやすくなるということである。
「作動油剤:性状」
考察各測定項目は使用範囲内にあり,良好。 |
「作動油剤:汚染度」
考察:微量の金属摩耗粒子が確認されたが影響なし |
ミリポア分析写真
(1)タンク内油中異物 ×100
(2)回路戻り側油中異物 ×100
(1)-1 タンク内油中異物 ×200
(1)-2 タンク内油中異物 ×400
(2)-1 回路戻り側油中異物 ×100
7. 潤滑油・作動油の汚染度測定と評価
油中に含んだ異物を評価するには,潤滑診断業務を営む上で,測定結果の数値が何を物語り,何を表現しているのか,汚染物と損傷の因果関係を解析・診断する必要がある。実際の作業解析に当たっては実践経験からのノウハウ的要素が多分にあるため,経験の浅い人たち誰もが早く技術習得するための各測定や項目ごとの診断作業を標準化することで効率の良い測定と確かな潤滑油・作動油の汚染・劣化診断が信頼性の高い活動となる。
ここでは代表的な汚染度測定と評価ポイントついて述べる。
(1)ミリポア分析
ろ紙(絶対ろ過粒度:0.8μm)を用いた汚染物の重量値と顕微鏡写真(×50~×100)での評価をする。
(2)自動微粒子測定
精密機構の油圧装置にはISO清浄度,一般的な油圧装置にはNAS等級法の評価方法が有効である。また,管理等級を厳しくしてロボットなどの精密機構にも引用した管理も可能である。
参考としてISO:区間番号評価とNAS:等級評価の関係(図5)と各種油圧装置別推奨汚染度管理例(表5)を紹介する。
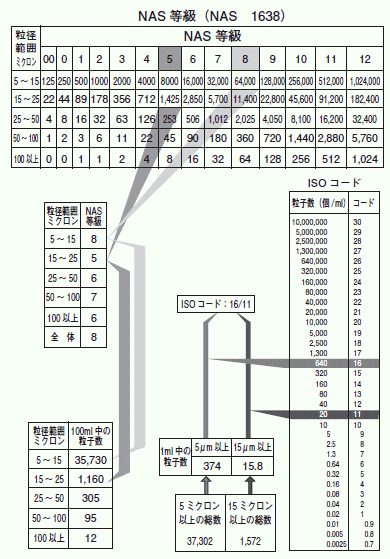
図5 汚染粒子評価:ISO法とNAS法
表5 各種油圧装置のISOとNASの推奨汚染度値
|
(3)フェログラフィ分析
強力な磁力によって,潤滑油中から分離,配列させた金属摩耗粒子を分類分析する方法であり,大きい摩耗粒子と全摩耗粒子を測定する定量フェログラフィと,摩耗粒子の大きさ,形状,色などを観察する分析フェログラフィの2つの方法がある。
定量フェログラフィは,測定した大きいグループ(5μm以上)をDl 表示し,小さいグループ(1~2μm)をDS表示して,それぞれカウントした数値を計算によって全摩耗量(WPC)と異常摩耗量(IS)が表される。計算方法は,
全摩耗粒子量(WPC):DL+DS
異常摩耗指数(IS):(DS+DS)(DL-DS)
実際に使用している定量フェログラフィ判定表を図6に示す。分析フェログラフィ顕微鏡による確認方法は,金属摩耗粒子の形態と分類表と摩耗粒子のサンプル写真などを引用して診断すると正確な判定になる。
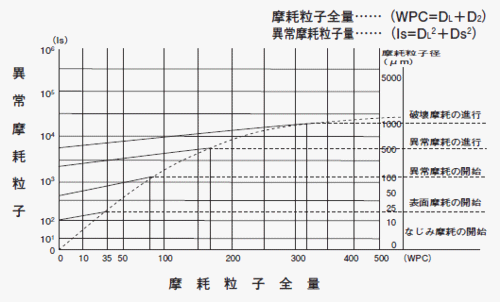
図6 フェログラフィ定量分析判定表
(4)ICP発光分光分析
プラズマ光源部,高周波電源,分光器,検出器およびデータ処理で構成されている。測定する試料中に大きな金属粒子が存在するとプラズマトーチ部のネプライザーが目詰まりや測定誤差を与えやすいので,前処理を測定原素に適した方法で行う(表6)。
表6 ICP発光分光分析の前処理方法
|
実際に使用している潤滑油や作動油に含まれている金属摩耗を測定し,抽出された金属摩耗元素濃度限界値の目安を(表7)に示す。
表7 金属摩耗元素濃度限界値の目安(ppm)
|
(5)赤外線吸収スペクトル分析測定
赤外線は,近赤外分光器,赤外分光器,遠赤外分光器で構成され,潤滑油・作動油に含まれる分子と固体の波長(ミクロン単位)と波数(カイザー単位)の特性を赤外線チャートに吸収値に伴う曲線で潤滑油基油・添加剤の分子構成の特徴が分かるので,他の化学物質の赤外線チャート情報と比較して化学物質の含有状態や化合物の構造を探すことで汚染・劣化・消耗状態の変化を診断することが可能である。
8. 油圧ロボット用ポンプの損傷防止診断事例
【ポンプの使用状況】
ロボット作動は微動のため低圧(3.5MPa),吐出量(13L/min)の定吐出容量型ベーンポンプを使用,作動油は鉱物系省電力型の油圧専用油(VG22)を使用し,40Lのタンク容量である。このポンプの経歴は2年ほどの周期でトラブルを起こし,その都度ポンプ一式の交換を実施しており,部品購入費や保全費用が増大している現状にある。
【損傷部の機構】
ポンプの構造は,軸とロータが一体化され,前後に軸受機構が設けられている。軸受の構造はベアリングタイプで,転動体は細い針状のコロが組み込まれ,ロータの軸回転バランスを保持する働きをする。
【傷部位】
損傷した軸受ベアリングの表面粗さを測定観察するとモータ側の軸径が最大値0.87mm摩耗減少し,転動表面にアブレシブ摩耗と欠損現象が確認できた。カバー側では軸径が最大1.13mm損傷減少し転動表面に赤紫色のテンパカラーとシビアースライディングの摩耗痕の段差を確認,さらに細い針状コロの転動表面部分では圧迫に伴う打痕跡と部分剥離の損傷が全数のコロ表面に多数観察され,潤滑領域の状態が異常である。
【故障の要因】
損傷面の観察から硬い異物が摺動面に混入し,噛込み損壊現象と判断される。また過去の故障歴でも常に同じ部位が損傷している。
【作動油循環回路内の摩耗粒子】
作動油に含まれる油中異物を循環回路部分とタンク内底部から採取し,金属摩耗粒子の形態を調べた。
*フェログラフィ定量分析では異常摩耗粒子(IS)が多量にあり,判定基準ランクが破壊進行領域にあった。
*タンク内の摩耗粒子をフェログラフィ定性分析で測定。その結果,黒色になった球状摩耗粒子,シャンク粒子,細い切削粒子など激しい損傷粒子が多量に観察された(写真1)。
疲労粒子
赤錆粒子
ラミナー(薄板)粒子
シビアー粒子
切削粒子
ボール状粒子
【損傷診断】
カバー側軸受内部の潤滑状態が閉鎖室になりやすい機構にあるため,油中の硬い異物が軸受の転動室内に堆積し,流体の悪い閉鎖現象が発生。軸を支える針状コロの間に硬い異物が噛み込み,コロの移動の乱れと軸の隙間に起きる重荷重が交互に加わり,圧痕損傷や転がり疲れ寿命による剥離現象を発生させていた。
【改善内容】
軸受方法を細い針状コロ式のベアリングによる転がり摩擦方式をすべり摩擦方式の軸受(DUブッシュ式オイル溝付タイプ)に変更した。
【効果確認】
軸受部内での油中異物堆積防止ができ,ポンプ騒音値も改善前の94~97dbから75~77dbに低下し,その後2年経過しても安定稼働を継続している。さらに全設備に採用した結果,消費電力量,部品購入費,保全工数など大きく削減され,潤滑管理費の数百倍の効果を上げた。写真2はベーンポンプロータ軸の改良前と改良後である。
改良前:ポンプ部品のトラブル(軸摩耗)
改良後:ポンプ部品の試験後(異常なし)
9. 今後の課題と展望
潤滑油・作動油の寿命は潤滑管理者のノウハウと技術力の発揮で異なる。潤滑油・作動油に含まれているベース・添加剤の物質が日々変化させられ,潤滑性能に障害を与え,汚染・劣化に導いて設備機械の稼働を妨げることに一刻も早く気付く必要がある。
潤滑管理は設備稼働を保証することであり,生産性確保と品質づくりが継続できる活動であると同時に,結果として多大なる経費低減を導き経済効果が積み重ねられることになる。有益な潤滑管理を達成するには,目先の管理ではなく汚染させないための日々工夫をする努力の継続と,潤滑診断技術力を生かした信頼される傾向診断の実践にあると考える。