潤滑油の生産量と添加剤の使用量および添加剤の種類と化学構造,機能について述べた。次に,添加剤の安全性,PRTR法,MSDSの概要について記述した。環境の変化に対応した潤滑油製品および添加剤の役割と性能について論じた。
1. 潤滑油の生産量と添加剤の使用量
最近のわが国の原油輸入量は年間約2億5千万kLである。この99%が燃料油等となり,1%が潤滑油製品となる。ゆえに潤滑油製品(高級品,並級品)の年間生産量は約250万kLといえよう。添加剤は平均8%添加されるとして年間約20万kL使用されており,平均価格1L 1,000円として年間約2,000億円の市場である。
2. 添加剤の使用例*1
各種潤滑油にどのような添加剤が加えられているのかを示すと表1のようになる。
表1 添加剤の使用例
|
3. 添加剤の化学構造と作用機能*2
1.酸化防止剤
潤滑油が金属の存在下で高温で空気に接触すると一部は酸化され,アルコール,ケトン,有機酸を経て一般にガム状スラッジと称する高分子樹脂状化合物を生成する。酸化は潤滑油の寿命を短くし,またガム状スラッジの発生は使用機械の正常な働きを阻害する。
このような潤滑油の酸化・劣化を防止するのが酸化防止剤であり,普通,実用面から低温用(タービン油,工業用潤滑油など)と高温用(内燃機関用潤滑油)に区分され,前者は連鎖反応停止剤であるヒンダード・フェノール系,芳香族アミン系などが用いられ,後者は過酸化物分解剤であるジアルキルジチオリン酸亜鉛が多く用いられる。ジアルキルジチオリン酸亜鉛は酸化防止剤としての働きのほかに腐食防止作用や極圧添加剤としての作用も持っている。また,この酸化防止剤の両者を組み合わせたものは相乗効果によって特に有効な場合がある。このほか酸化防止作用を助けるものに金属不活性化剤がある。代表的な酸化防止剤の化学構造は次のとおりである。
(1)2,6-ジターシャリーブチル-4メチルフェノール(DBPC)(図1)
(2)ジアルキルジチオリン酸亜鉛(図2)
酸化防止剤は,油の酸化によって生成した遊離基(フリーラジカル)と反応して不活性化する働きをする。
油への添加量は0.1~2.0wt%位である。
図1 2,6-ジターシャリーブチル-4メチルフェノール(DBPC)
Rはアルキル基または芳香族基
図2 ジアルキルジチオリン酸亜鉛
2.粘度指数向上剤
これは潤滑油の低温における粘度と高温における粘度との差を小さくする作用を有している。
粘度指数(VI またはVIE)の大きい油ほどこの差は小さい。最近では主にマルチグレードエンジン油,自動変速機油,作動油,ショックアブソーバー油に添加され,欠くことのできないものとなっている。
これらのポリマーを潤滑油に添加すると,低温では比較的溶解性が悪く一部溶解した分子も径の小さいまり状になって存在するため,添加油の粘度は低い。高温になるとポリマーの溶解性が良くなるとともに溶解した分子の径も大きくなるため,添加油の粘度は高くなる。
一方,潤滑油基油の粘度は温度の上昇とともに低下するが,ポリマーの溶解度上昇のため全体としての粘度の低下は少なくなる。代表的な粘度指数向上剤は次のとおりである。
(1)ポリアルキルメタクリレート(図3)
(2)ポリイソブチレン(図4)
油への添加量は2.0~10.0wt%位である。
RはC1~C18程度,平均C12
分子量は100,000位
nは重合度
図3 ポリアルキルメタクリレート
分子量は5,000~50,000位
nは重合度
図4 ポリイソブチレン
3.流動点降下剤
n-パラフィンをほとんど含まないナフテン系原油より精製したナフテン系潤滑油基油は,そのままで-40℃程度の低い流動点を示す。しかし,粘度指数は一般に低い。一方,パラフィン系原油より精製した高粘度指数パラフィン系潤滑油基油は脱ろう温度(-15~-20℃)に支配されてその流動点が決まる。
脱ろう温度を下げれば低流動点油は得られるが,潤滑油の収率は著しく悪くなる。したがって,今日ではなるべく高い温度で脱ろうして油収率をできるだけ落とさないようにし,流動点は流動点降下剤の添加によって補うという方法が取られており,この方法が最も経済的であるとされている。代表的な流動点降下剤は次のとおりである。
(1)ポリアルキルメタクリレート(図3)
(2)ポリイソブチレン(図4)
(3)アルキルナフタレン縮合生成物(図5)
(4)アルキルフェノール縮合生成物(図6)
含ろう油をある温度まで冷却するとろう分が溶解度を失って析出し,三次元的に成長し,スポンジのような網目構造をつくり,その間に油分を抱え込んでしまうようになると急に流動性を失う。流動点降下剤を添加しておくと,ろう分の結晶析出は止めえないが,アルキル芳香族型はろうの結晶表面に吸着し,ポリアルキルメタクリレート型は共結晶して網目構造のできるのを抑え,ろう分が塊状の結晶として析出していても油の流動性は失われない。
油への添加量は0.1~1.0wt%である。
Rはアルキル基
分子量は5,000~10,000位
nは重合度
図5 アルキル・ナフタレン縮合生成物
Rはアルキル基
nは重合度
図6 アルキルフェノール縮合生成物
4.清浄分散剤
潤滑油添加剤使用量の約50%は清浄分散剤であり,その大部分はガソリンエンジン油およびディーゼルエンジン油に使用される。
ディーゼルエンジンでは油に不溶な高温スラッジは主に潤滑油の酸化によって生ずる重合性スラッジプリカーサがスラッジ生成の主因であり,硫黄の多い燃料を使用する場合には生成する硫酸および不完全燃焼によるすすがこれに加算される。
ガソリンエンジンでは高温スラッジよりもむしろ停止発進運転に伴って生じる低温スラッジが主である。これはガソリンの不完全燃焼によって生ずるスラッジプリカーサがスラッジ生成の主因であり,これに水とアンチノック剤と掃鉛剤からくる金属およびハロゲンが加算される。
清浄分散剤はこれら固形物の沈積を防止,抑制するために油に添加される。清浄分散剤の役割は次のように分類することができる。
(1)分散作用
不溶性スラッジ,すす,固体きょう雑物の油中への分散
(2)可溶化作用
スラッジプリカーサ,水などの可溶化
(3)中和作用
有機酸,硫酸,窒素酸化合物の中和
代表的な清浄分散剤は次のとおりである。
(1)過塩基性金属フェネート(図7)
(2)ポリアルケニルこはく酸イミド(図8)
油への添加量は2.0~10.0wt%位。
Mは2価の金属でCa,Ba,Mg等,
Rはアルキル基,xは縮合度,
塩基価100~300mgKOH/g
図7 過塩基性金属フェネート
CH2-CH=CH-Rはたとえば分子量約1,000のポリイソブチレン
図8 ポリアルケニルこはく酸イミド
5.腐食防止剤
腐食防止剤はエンジンの部品に使用される軸受金属など非鉄金属の腐食を防止する添加剤であり,さび止め剤とは鉄の腐食を防止する添加剤のことで両者は区別して用いられる。重要な軸受金属としては銅-鉛,鉛-錫-アンチモン,カドミウム合金などがある。腐食防止剤はこれらの非鉄金属と反応して耐食性保護膜を形成する。代表的な腐食防止剤は次のとおりである。
(1)ジアルキルジチオリン酸亜鉛(図2)
(2)ジアルキルジチオカルバミン酸バリウム(図9)
(3)硫化テルペン
(4)リン硫化テルペン
油への添加量は0.2~2.0wt%位。
Rはアルキル基
図9 ジアルキルジオチカルバミン酸バリウム
6.さび止め剤
これは図10のように鉄あるいは鋼表面に選択的に吸着膜を形成し,それが水や酸素との接触を止めてさびの生成を防ぐ役割をする。
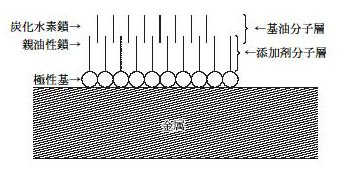
図10 鋼表面へのさび止め剤の吸着
循環油量が多く,少量の水しか存在しないゆるやかな条件で使用される場合には,アルキルこはく酸型のものやその有機アミン類中和物がよく用いられる。船舶機械や長期間貯蔵や,屋外装置類のような過酷な条件下の場合には,より吸着性の強い酸性フォスフェイト,アルキルチオ酢酸,Na-あるいはCa-スルホネートが用いられる。さび止め性能と極圧性能は競合する場合があるので混合使用の時は注意しなければならない。気相さび止め剤も紹介されている。
油への添加量は,0.1~1.0wt%位。
7.極圧添加剤
ハイポイドギヤーのように接触する金属面の負荷圧力が非常に高い場合には,鉱油だけでは油膜が切れて潤滑の役目を果たせない。このような極圧条件下で有効に作用する添加剤を極圧添加剤といい,硫黄,リンを含む化合物が使用されている。
硫黄化合物は高温下で金属と反応し,強固な硫化鉄被膜を形成して,摩擦,摩耗を防止する。
(1)硫化油脂
(2)硫化テルペン
(3)硫化スパーム油(図11)
(4)ジベンジルサルファイド(図12)
図11 硫化スパーム油
図12 ジベンジルサルファイド
過塩基性金属スルホネート(塩基価300~400mgKOH/gの過塩基性Ca-スルホネート)が有効である。
リン化合物も高温下で鉄と反応してリン化鉄を形成して摩耗を防止する。トリクレジルホスフェイト(TCP)(図13)が有効である。
油への添加量は5.0~10.0wt%位。
図13 トリクレジルホスフェイト(TCP)
8.油性向上剤
潤滑部の金属表面上に吸着して境界潤滑の際,単分子膜を残すような性質を与える添加剤をいう。一般に油性向上剤は極性化合物であり,極性基が金属表面に物理的に吸着し,他端の非極性基の相互の結合力で吸着膜を強固にし,摩擦や摩耗を減少する働きをする。ラードオイルなどの油脂,オレイン酸,ステアリン酸などの脂肪酸,高級アルコールおよびそのエステル類が油性向上剤として用いられる。
また,ハイポイドギヤー油やATFなどの使用中に発生する摩擦振動音を防止するのに油性向上剤が使用(併用)されて成功を収めている。
油への添加量は0.1~1.0wt%位。
9.泡消し剤
潤滑油が連続的に撹拌または循環されて使用される場合,空気をだき込み,消えにくい泡ができる。泡が生成すると潤滑油のしゅう動面への供給が不十分になったり,タンクからあふれ出たりして事故の原因となる。特に清浄分散剤が添加されている潤滑油は泡をつくりやすいので,泡消し剤を加えることが多い。
最も一般的な泡消し剤はポリオルガノシロキサンである。
(CH3)SiO[Si (CH3)2O]nSi (CH3)3
n=1~2,000
泡消し剤の作用機構は油と水の界面張力を減少し,空気泡の集合を容易にさせることにある。
10.乳化剤
切削油,圧延油および不燃性作動油など,乳化油をつくる場合に乳化剤が必要になってくる。乳化剤としては,石油スルフォン酸塩,硫化油脂や脂肪酸石けんなど陽イオン界面活性剤,トリエタノールアミン石けんなどの陰イオン界面活性剤,ポリオキシエチレンアルキルフェノールエーテルのように非イオン界面活性剤などがある。また,かびなど微生物の繁殖を止めることも大切である。
11.摩擦調整剤
潤滑油の摩擦調整剤(friction modifier;フリクションモディファイア,以下FMと略す)は潤滑油に微量添加することによって静および動摩擦係数を小さくする作用のある有機および無機化合物の総称である。元来,FMはギヤー油,変速機油,案内面油,トラクションフルイド等に添加され,動力の伝達を制御する場所に使用されてきた。1978年の石油危機以来,自動車の燃費が世界中の重要な課題となり,そのために自動車の潤滑油の低粘度化およびFMの添加が行われ,その結果,著しい燃費の向上が実現された。
代表的なものは次のとおりである。
(1)長鎖アルキルカルボン酸とその誘導体
(2)長鎖アルキルリン酸とその誘導体
(3)長鎖アルキルアミン,アミド,イミドおよびその誘導体
(4)油溶性モリブデン化合物
特に近年,旭電化が開発,商品化したSakura-Lubシリーズが好評を博している。
一例として,ガソリンエンジン油にFMを0.1wt%添加することにより,燃料消費量が数%低減する。
12.防かび剤(エマルション用)
エマルション中に生存する細菌,かび,酵母などの微生物が引き起こす障害作用を抑制または防止する。
防かび剤としては,フェノール系化合物,ホルムアルデヒド系化合物,サリチルアニリド系化合物などがある。
13.抗乳化剤
エマルションを破壊し,その構成成分に分離する。
使用済み水溶性切削油の油水分離,再生等に有効である。抗乳化剤としては,第4級アンモニウム塩,硫酸化油,ナフテン酸金属塩,リン酸エステル等がある。
4. 添加剤とPRTR法*3
PRTR法では,354物質が第1種指定化学物質と定められた。これらは,
(1)環境への排出量や廃棄物としての移動量の届出
(2)事業者間の製品安全データシート(Material Safety Data Sheet;化学物質等安全データシート,以下MSDSと略す)の交付
が義務付けられている。潤滑油添加剤には発がん性のある特定第1種指定化学物質は使われていない。添加剤として使われているPRTR法対象物質は表2に列挙する第1種指定化学物質である。
PRTR法の対象になる製品は,特定化学物質を1重量%以上含有するものである。
表2 添加剤関連第1種指定化学物質
(注)PRTR(Pollutant Release and Transfer Resister) |
5. 添加剤とMSDS
化学物質の譲渡・提供者に対して,物質の有害性等の情報提供(MSDS交付等)が2001年1月より義務化された。具体的には,
(1)名称
(2)成分およびその含有量
(3)物理的および化学物理的性質
(4)人体に及ぼす作用
(5)貯蔵または取り扱い上の注意
(6)その他省令で定める事項
など6項目が規定されている。
この中で石油製品に関連する主な通知物質は,ガソリン,灯油,軽油,鉱油(潤滑油,グリース等),石油ナフサ,石油エーテル,石油ベンジン,ミネラルスピリット,固形パラフィン等である。
6. 潤滑油製品の開発と今後の課題
1.ガソリンエンジン油
基油の精製度はなるべく高くし(水素化分解油で,飽和炭化水素成分がほぼ100%,芳香族炭化水素成分がほぼ0%),低粘度油を用い,マルチグレードエンジン油をメインにしている。
また,α-オレフィン共重合油(PAO)を基油にしてつくっている。
添加剤はコンポーネントを購入して基油にそれぞれ配合するという方法はあまりとられていない。最適のパッケージ型添加剤を購入して基油に混合している。
パッケージ型添加剤の構成成分は一例を挙げると,粘度指数向上剤(ポリメタクリレート),清浄分散剤(過塩基性Ca-フェネート,Ca-スルホネート,ポリイソブテニルこはく酸イミド),酸化防止剤(ジチオリン酸亜鉛,ヒンダードフェノール系酸化防止剤),流動点降下剤(ポリメタクリレート),泡消し剤(シリコーン油),さび止め剤(アルケニルこはく酸)の最適混合物である。
さらに燃費を向上させるために,最後にFM,例えばモリブデンジチオカーバイトを微量添加する。
エンジン試験は米国の公的機関に依頼して実施し,世界に通用するISO規格に合格させている。
ガソリンエンジンでは,排出ガスの後処理装置として三元触媒およびNOx吸蔵型触媒が用いられているが,触媒の被毒物質として燃料,エンジン油中のリン化合物および硫黄化合物が挙げられており,触媒寿命の延長のためエンジン油にも低リン化,低硫黄化が求められている。ガソリンはサルファーフリーガソリンが登場し,硫黄は10ppm以下となった。現在,これらの元素を含まずに低摩擦係数を保つ新しい添加剤の開発が進められている。
2.ディーゼルエンジン油
ディーゼルエンジン油の場合も,高度に精製した基油に,ガソリンエンジン油とほぼ同様な添加剤が添加されている。
ディーゼルエンジンでは,浮遊粒子状物質(PM:Particulate Matters)低減の一つの方策として,ディーゼル微粒子捕集フィルター(DPF:Diesel Particulate Filter)の装置が普及(一部では義務付け)されつつある。このDPFに関する技術的な問題点としては,エンジン油中に含まれる灰分(主としてCaを含む塩基性清浄分散剤に起因する)が燃焼できないため,これがフィルター内部に堆積して,目詰まりを起こし,排圧の増加,排気温度の上昇や燃費の悪化につながることがある。エンジン油の低灰化が急務となっている。しかし最近では軽油の超深度脱硫が進み,硫黄分は50ppm以下となりつつあるので,従来ほど多くのCa系清浄分散剤は必要となくなってきていると思われる。
3.高塩基性舶用シリンダ油
溶剤精製法で製造したパラフィン系あるいはナフテン系基油に対して,塩基価300~400mgKOH/gもある過塩基性金属フェネート,スルホネート,サリチレートを20~30wt%混合して,塩基価60~80mgKOH/g の高塩基性舶用シリンダ油製品を製造している。酸化防止剤,極圧添加剤,腐食防止剤の多機能を有するジチオリン酸亜鉛を添加することもある。
最近は海洋における大気汚染(NOx,SOx)も問題になりつつあり,船舶の排気ガスもクリーンでなければならない。
硫黄分の多い残さ燃料油の燃焼によって生成するSOxを中和することが重要である。また,大量に消費,燃焼される舶用シリンダ油自体も硫黄分の少ない添加剤がベターである。
4.工業用潤滑油*4
酸化安定性の優れた高性能タービン油を製造するためには,基油の精製度が重要である。添加剤としては,通常は,酸化防止剤としてジターシャリーブチル-パラクレゾール(DBPC),さび止め剤としてアルケニルこはく酸などが用いられる。TOST法による酸化安定性を比較すると,溶剤精製基油の場合3,800時間位,水素化分解基油の場合6,500時間位,FT(フィッシャートロプシュ)合成基油の場合9,500時間位という報告も見られる。
油圧作動油には,耐摩耗添加剤としてジチオリン酸亜鉛(ZnDTP)を用いたものと硫黄-リン化合物(SP)を用いた無灰型のものの2種類があるが,SP系のものの方が性能が良く発展している。基油の精製度と特性が重要でPAO基油のものは特に優れている。
5.金属加工油
従来,水溶性切削油あるいは油溶性切削油の極圧添加剤として,塩素化パラフィンが広く用いられてきたが,環境上好ましくないので,市場から除々に姿を消しつつある。
これに代わり得るものとして最近,研究開発されたのが過塩基性Ca-スルホネートで,著者の考えでは,この添加剤中の微細なCaCO3が固体潤滑剤の役目を果たすと思われる。したがって新しい切削油の添加剤組み合わせとして,次のものが推薦できる。
(1)過塩基性金属スルホネート(アルカリ価400mgKOH/gの過塩基性Ca-スルホネート)
(2)硫化油脂
(3)硫化オレフィン
(4)多硫化物
6.グリース
バリウム石けん(グリース原料)やバリウムスルホネート(さび止め剤)は非水溶性であり,わが国ではPRTR法の規制外である。しかし,欧米では規制されているので,その影響が及んでくる可能性はある。
シェルが開発した12-ヒドロキシステアリン酸リチウム石けんグリースは万能型グリースで,世界の60%のシェアを有している。
最近特に賞用されているグリースはウレアグリースである。耐熱性,耐摩耗性に優れ,摩擦係数が小さい。省燃費,長寿命グリースとして今後さらに伸びると考えられる。
7.生分解性潤滑油およびグリース*5
地球環境の保全,保護のため特に欧州では生分解性潤滑油およびグリースの研究開発が進んでおり,実用化されている。土壌菌等による生分解によって油は最終的にH2OとCO2となる。
生分解性の特に優れている油は,植物油と脂肪酸エステルである。
作動油の場合,基油としてナタネ油やトリメチロールプロパンエステルを用い,酸化防止剤としてDBPC を用いると酸化安定性の良い生分解性油が得られた。
グリースの場合,ナタネ油を基油とし,リチウム石けんを配合し,酸化防止剤としてアミン系酸化防止剤を添加すると酸化安定性の良好な生分解性グリースが得られた。
従来の鉱油系製品にくらべると,性能的にはやや見劣りがするが,規格に合格し,環境保全に有効なので,急速に伸びている。品質優先よりも環境優先という考え方が浸透している。
潤滑油添加剤に課せられた使命は大きく,今後更なる研究開発を推進しなければならない。
<参考文献>
*1 藤田稔,「石油分析化学」 石油分析化学研究所(1992)
*2 藤田稔,「燃料油・潤滑油および添加剤の特性と分離・分析技術」 技術情報協会(1996)
*3 「環境と潤滑油」 (社)潤滑油協会(2004)
*4 藤田稔,潤滑経済(2003)2 月号,P.40.
*5 藤田稔,MATERIAL STAGE,P.52,vol.1.No.6(2001)