はじめに
焼入れや焼戻しが代表的な処理法である熱処理とは,金属部品の性質を加熱,冷却操作によって変化させる処理法のことである.焼入れ処理では,鋼等の金属部品を高温に加熱した後に急冷して硬い組織を得るため,部品を熱処理油等の冷却剤に投入して冷却する*1.焼戻し処理では,焼入れ後の鋼等の部品を変態点以下の適当な温度に加熱後・冷却して硬さを低下,靭性を向上させる.焼入れ,焼戻し処理前後の部品には通常,防錆油の塗布による防錆処理が施されており,関連する不良の事例が数多くみられる.JIS K 2246:2018 防せい油*2,では“防せい油”と定義されるが,本稿では汎用的に用いられている“防錆油”を用いる.油剤メーカーでは防錆油の選定や防錆処理法の改善を提案しているが,提案不足と認識している*3~*5.
そこで,本稿では,熱処理,特に焼入れ工程に適用される防錆油に関連する課題,防錆油の選定や防錆処理法の改善による対策について述べる.
1.熱処理を伴う鋼部品の製造工程の動向
図1に,熱処理を伴う鋼部品の製造工程例を示す.例えば,切削された部品は,防錆油を塗布して保管・輸送後に,脱脂洗浄してから加熱し熱処理油に浸漬されて焼入れ処理を施される.その後,付着した熱処理油等を脱脂洗浄してから,焼戻し後に防錆油を塗布して一時保管・輸送される.
近年,このような工程において,切削に用いられる切削油の水系化が進んでいる.それによって,水溶性切削油と防錆油の混合による不具合や,脱脂洗浄工程の多様化に伴う焼入れ時の部品への防錆油,切削油の残存による不具合等が製造の現場で確認されている.
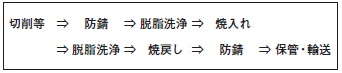
図1 熱処理を伴う鋼部品の製造工程例
2.防錆に関連する不良事例と対策
2.1 防錆油の種類と特徴
鋼部品の熱処理の前後工程で使用される防錆油には,主に,JIS K 2246に規定される溶剤希釈形や潤滑油形の防錆油が用いられている.防錆油は,鋼等の金属の表面に通常数μmの薄い油膜を形成して,加工過程や保管・輸送過程のような限られた期間の一時的な防錆の役割を担うものである.通常では目的とする防錆期間の終了後に脱脂洗浄により除去される.防錆油は,防錆添加剤,油膜調整剤,基油,その他から構成される.防錆添加剤には,金属スルホネートや酸化ワックスの金属塩,油膜調整剤にはワックス類や重質油,基油には重質溶剤や軽~重質油に分類される様々な構造の炭化水素系化合物,その他には,防錆油の酸化劣化を防ぐ酸化防止剤がほとんどの防錆油製品に配合されている*6.
本稿で取り扱う溶剤希釈形防錆油は,金属部品へ塗布後に溶剤が揮発して添加剤の濃縮された防錆塗膜を形成するものである.塗布した防錆油は,腐食要因物質の部品表面からの遮断作用,部品表面に存在する水や水溶性物質(水溶性切削油等の水系加工油剤や腐食促進物質)を表面から置換除去する水置換作用,表面から置換されあるいは外部から侵入してきた水等の水溶性物質の油膜内への可溶化作用等によって,金属部品のさび・腐食を防いでいる.
2.2 熱処理工程の前後で適用される防錆油に関連する課題と対策
表1に,熱処理を伴う各種鋼部品の製造工程で使用される防錆油に関連する不良事例について整理した.例えば,水溶性切削油を用いて切削された部品の一時保管時には防錆油が塗布され,部品上の防錆油は焼入れ前に脱脂洗浄される.脱脂洗浄された部品は焼入れ処理され,その後に熱処理油を脱脂洗浄されてから焼戻し,再び防錆油を塗布されて保管・輸送される.このような工程では,水溶性切削油と防錆油の混合による粘着物生成等の不具合,防錆油の脱脂洗浄不良,防錆油残存による焼入れ時の外観や硬さ不良,脱脂洗浄後に防錆油を塗布しない部品のさびや防錆油の油槽中の水分量に起因する防錆性能低下が懸念される.
本稿では,これらのうち,水置換性防錆油の適用による水溶性切削油の置換性,分離性の改善事例,脱脂洗浄性に優れる防錆油の選定による脱脂洗浄性の向上事例について述べる.さらに詳しい内容*3,あるいは,表1において本稿で紹介しない課題と対策について興味を持たれた方は,参考文献4,5を参照いただきたい.
表1 熱処理工程の前後で適用される防錆油に関連する不良事例と対策
|
2.3 水切油と防錆油混合時の不具合とその対策
2.3.1 課題
切削後の部品,特に水溶性切削油が付着した部品に防錆油を塗布すると,防錆油の油膜に水溶性切削油の主成分である水が混入することで防錆油の可溶化作用の限界を超えること,防錆油中の防錆添加剤が部品表面に吸着できないことによって,防錆油が本来の防錆性能を発揮できなくなる事例が認められる.また,両油剤に含有される成分同士の反応によって粘着性のある固形物が生成して部品表面に付着することがあり,そのままの部品が熱処理工程に持ち込まれることで焼入れ不良の原因となる事例もある.そのため,防錆油の塗布前には,部品表面から水溶性水切油等の前工程油剤を除去することが重要である.しかし,前工程油剤の脱脂洗浄工程を設けると生産性が低下してしまうため,有効な方策が必要とされてきた.
本課題に対しては,JIS K 2246の3種1号に分類される溶剤希釈形防錆油の中でも,特に水置換性・水分離性を向上した防錆油(以降,水置換性防錆油と略記)の適用が有効である.水置換作用とは,固体すなわち金属と水との界面張力が金属と防錆油との界面張力よりも大きくなると,金属表面の水の脱離と同時に,水に置き換わって防錆油が金属表面に付着する作用*7のことである.この作用によって,後から塗布した防錆油が部品表面に存在する水や水溶性切削油等を部品表面から除去して,防錆油本来の防錆効果が発揮できるようになる.
防錆油の塗布工程では,水溶性切削油が付着した部品を水置換性防錆油の油槽に浸漬後に引き上げて部品表面から水溶性切削油を置換除去する.置換された水溶性切削油は防錆油に比べて密度が高く分離して油槽の下層に沈降するので,定期的に油槽内からドレンアウトすることで防錆油の水置換作用,水可溶化作用が一定期間維持される.そのため,防錆油と水溶性切削油等との分離性も重要な特性である.
本節では,水置換性防錆油と一般的な防錆油との比較で,水溶性切削油に対する置換性,分離性を評価した結果について述べる.
2.3.2 実験方法
置換性の評価は,JIS G 3141:2017に規定のSPCC鋼板(厚さ0.8mm,幅60mm,長さ80mm)を,1vol%濃度のソリューション系水溶性切削油(JIS K 2241:2017 A3種に規定)へ5秒間浸漬し,引き上げて各防錆油に浸漬した後,目視で観察して鋼板上に水溶性切削油が認められなくなるまでの秒数を測定して行った.分離性については,100mLのガラスシリンダに水溶性切削油および各防錆油をそれぞれ50mL投入して蓋を締め,手振りで上下に激しく10秒間振盪後に静置し,1分および5分経過後の油水分離状態を目視観察した.
2.3.3 置換性と分離性の比較
図2に,各防錆油によって鋼板表面に付着した水溶性切削油が置換されるまでの秒数を比較した.水置換性防錆油では,1秒後には水溶性切削油を置換している.一方で,水置換性を考慮しない一般的な防錆油では,水溶性切削油を置換するのに30秒を要している.本稿に用いた油剤に限らず,一般的な防錆油は含有する防錆添加剤の効果により水置換性を有するものである.したがって,通常の用途であれば,数10秒程度で水置換が可能であれば水溶性切削油が付着した部品に適用しても十分な防錆効果を発揮する.ただし,部品の形状,表面状態や浸漬条件によっては,一般的な防錆油では水溶性切削油の置換が不十分となる可能性がある.このような場合には,水置換性に優れる水置換性防錆油の適用がより有効なことを示している.
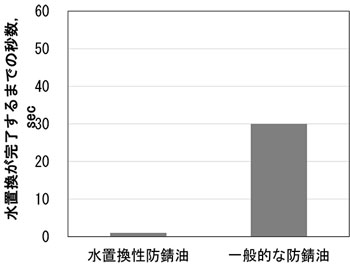
図2 水溶性切削油が置換される秒数の比較
次に,図3の分離性操作後の油水分離状態をみると,水溶性切削油との分離性も考慮した水置換性防錆油では,振盪して静置1分後には油層の一部が分離し始め,5分後には油水が完全に分離している.一方で,一般的な防錆油では静置5分後でも液全体が乳化した状態である.このことは,防錆油が油槽内で乳化した油剤を部品に塗布すると,水溶性切削油の基剤成分の種類によっては,防錆油の防錆効果の低下や部品上での固形物の生成が懸念されることを示している.
図3 分離状態の比較
|
以上の結果から,水溶性切削油等の水系油剤が付着した部品に防錆油を塗布する場合には,部品表面から迅速に水系油剤を取り除くことができ,分離性も兼ね備えた水置換性防錆油の適用を推奨する.
2.4 防錆油の脱脂洗浄不良とその対策
2.4.1 課題
防錆油が付着した部品をそのまま浸炭焼入れ処理(鋼等の部品を浸炭ガス等で加熱して,部品表面近傍の炭素濃度を高めることによって部品内部の優れた靭性を維持しながら表面を硬くする処理法)すると,浸炭不良や外観不良を生じることがある.その原因は,部品表面の防錆油油膜によって焼入れ時に浸炭ガスが部品内部に侵入できない.防錆油中の炭化水素と金属分が焼入れ時の高温で炭化・灰化する.あるいは防錆油の油膜内に含まれる溶存酸素や水分が焼入れ時の部品表面の酸化状態に影響することによると考えられる.そのため,焼入れ処理の前工程での防錆油の脱脂洗浄を推奨しているが,部品表面に薄くて強固な油膜を形成させる防錆油の設計思想によって,防錆油の種類によっては短時間で脱脂洗浄し難い油剤がある.例えば,部品へ塗布後に溶剤が揮発する溶剤希釈形防錆油においては,溶剤揮発後の油膜粘度が低いと脱脂洗浄性は良好であるが,高くなると劣ることがある.また,脱脂洗浄性には,部品表面に直接吸着している防錆添加剤の部品表面への吸着の強さと脱脂液中での脱離のしやすさも大きく関係する.
本節では,防錆油の溶剤揮発後の油膜粘度が脱脂洗浄性に与える影響を評価するため,動粘度および配合する添加剤が同じであり,塗油後に溶剤揮発後の油膜粘度が異なる2種類の溶剤希釈形防錆油を用いて,炭化水素系洗浄剤による脱脂洗浄性を比較評価した結果について述べる.
2.4.2 実験方法
油剤の40℃動粘度はいずれも2.6mm2/sであるが,溶剤揮発後の油膜粘度がそれぞれ129,55mm2/sとなる防錆油を準備した.脱脂洗浄の操作については,SPCC鋼板(厚さ0.8mm,幅60mm,長さ80mm)を防錆油へ30秒浸漬後に引き上げ,吊り下げた状態で24時間油切りして鋼板上防錆油膜内の溶剤を揮発させた.次に,鋼板を炭化水素系洗浄剤に1~7分間浸漬し,80℃で乾燥60分後の鋼板重量から防錆油の付着量を測定して,脱脂洗浄試験前後の重量変化から鋼板上の防錆油の残存率を算出した.
2.4.3 脱脂洗浄性の比較
図4に示す炭化水素系洗浄剤による脱脂洗浄後の防錆油の残存率の経時変化をみると,いずれの油膜粘度の防錆油の場合も脱脂洗浄時間とともに鋼板上の残存率が低下している.油膜粘度の高い防錆油の方が残存率は高く,脱脂洗浄し難いことを示している.
この結果から,防錆油の残存に起因した後工程の焼入れ不良を懸念する場合には,溶剤が揮発した後の油膜粘度の低い溶剤希釈形防錆油の適用を推奨する.

図4 脱脂洗浄後の防錆油残存率に対する油膜粘度の影響
おわりに
熱処理工程の前後で使用される防錆油に関連する課題に対して,本稿では,水置換性防錆油の適用による水溶性切削油の部品表面からの除去性の改善事例,溶剤希釈形で油膜粘度の低い防錆油の選定による部品からの防錆油の脱脂洗浄性改善事例について述べた.
本稿で紹介した以外にも,適切な防錆油選定と防錆処理により,熱処理工程の部品防食に関わる様々な問題の多くが解決可能になると考えている.
今後も,筆者がこれまで蓄積してきた経験・ノウハウを基に,様々な提案を続けていく.
<参考文献>
*1 日本熱処理技術協会:熱処理用語辞典,日刊工業新聞社(2002)
*2 日本規格協会:JIS K 2246:2018 防せい油(2018)
*3 長瀬直樹:防錆管理,64,237(2020)
*4 長瀬直樹:防錆管理,64,295(2020)
*5 長瀬直樹:防錆管理,64,386(2020)
*6 日本防錆技術協会:第59回防錆技術学校 工業包装科テキスト 防錆油剤(2019)
*7 桜井俊男:石油製品添加剤,幸書房(1979)