メンテナンスコスト削減およびシステム稼働率向上の抜本的な解決策は流体の清浄度管理である。流体の清浄度を管理するには,適切な性能のフィルターを設置することは必要だが,十分ではない。常に清浄度をモニターし,清浄であることを検証して必要にして十分な管理を遂行できる。
はじめに
現在の経済環境では,企業は利益体質を強化するために効率改善を競っている。企業によっては,必死にビジネスに留まるためにだけ,このような改善活動を実施している。製品品質と生産工程の効率の改善は生産性向上の二つの要である。多くの企業が品質改善プログラムやTQC(トータル・クオリティ・マネージメント)システムを実施し,生産効率の最適化と廃棄物の最小化のために,生産工程の継続的評価および改善を行っている。
機械や設備の摩耗で多くの企業は毎年多額のコストを支払っている。50~80%の故障原因は作動油や潤滑油中の異物であるということは,よく知られている。したがって,すでに確立された清浄度管理技術を正しく適用することが,解決策のひとつである。このことは,コストの削減だけでなく,運転効率やサービスの改善をもたらす。
しかしながら,機械や設備のメンテナンスは,単純に利益を減らすだけの間接コストと考えられている。しかし,これは誤った考えで,米国における調査結果によると,状態基準保全の導入によりメンテナンスコストを25~45%削減している。状態基準保全では,機械や設備の性能要素があらかじめ定められた基準を外れた時にだけ,メンテナンスが実施される。したがって,設備の性能を表す要素の連続的なモニターは重要で,基準を外れた状態で機械や設備が運転される時間は最小限に留められる。
メンテナンスコスト削減およびシステム稼働率向上の抜本的な解決策は流体の清浄度管理である。流体の清浄度を管理するには,適切な性能のフィルターを設置することは必要だが,十分ではない。常に清浄度をモニターし,清浄であることを検証して必要にして十分な管理を遂行できる。今回は,作動油や潤滑油の清浄度管理における清浄度モニターの役割についてまとめる。
1. 故障削減によりコスト低減
潤滑不良に起因する故障コストを聞くとびっくりする。ドイツでの調査結果によると,1987年におけるドイツ産業界での損失コストは現在の貨幣価値にすると1兆円以上であった。また,英国での1992年の調査では,潤滑不良に係わる問題解決で,年間約4,000億円が節約できたはずだとの結果もある。
信頼性が低いと,生産活動の妨げになるために運転コストが大幅に増加する。たとえ製品が部品であろうと,機器やシステムであろうと,またはサービスであろうと。サービスへの質に多大な影響を与え,お客様を怒らせ,お客様を失う結果になりかねない。さらには,保証費用の支払などになる場合もある。信頼性が低いと,突発故障による生産活動の停止による更なるコスト増への圧力となりメンテナンスコストの増大となる。経済状況の悪化などで最初に削減対象となるのが,削減が安易なメンテナンス予算である。英国の調査によると,メンテナンス関連の投資を切り詰めることによる総コスト削減の手法は,メンテナンス投資が1に対して利益効果は40であり,安易なメンテナンス予算の削減は逆効果であると報告している。さらに,総コスト削減には,メンテナンス活動の方針を再検討し,戦略的なメンテナンス活動を実施することが重要であると報告している。
メンテナンスコストについては,数多くの調査結果があるが,一般的に設備性能のモニターを基本としたメンテナンス手法が効果的な解決策であることを示している。この手法は,状態基準保全と呼ばれている(図1)。
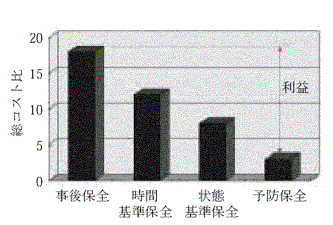
図1 保全手法の相違によるコスト比較
状態基準保全では,設備の機能に関連するパラメーターを測定し,その傾向を分析し,メンテナンス項目や計画を決定する。この手法により,故障に至る前に異常を検出し,メンテナンス計画の立案やメンテナンスに必要な材料の手配に十分な時間が取れる。これによって,生産計画に一致したメンテナンスが可能となり,生産損失を防止できる。このメンテナンス手法の真の利点は,設備の状態を継続的にモニターし,あらかじめ定めた許容値を超える前に是正できることである。この方法により常に最適な状態で設備を運転できることになる。そのため,生産目標,製品品質の維持,不必要なエネルギー消費の削減などを達成できる。
状態基準保全の先には予防保全がある。繰り返し発生する故障や問題の再発防止だけでなく,設備の寿命延長に貢献する。故障原因を調査し,設備の運転効率に与える影響度を考慮して,設計や操作方法を変更することによって故障フリーの設備運転と設備の長寿命化が可能となる。その結果が総コストの削減となる。この方法によって,より効果的で利益性の高いメンテナンス資源の活用が可能となる。最終的に,メンテナンスが間接コストではなくなり,企業の有力な利益源となる。
前述のように,潤滑不良による故障が減少することによって大きなコスト削減が可能である。しかし,そのためには潤滑不良の主要原因である汚染異物の体系的な管理が重要となる。すなわち,全生産工程において,汚染異物の影響を受ける機械や設備の部位を科学的に識別し,その結果生ずる問題や課題を把握し,その影響を最小化するように生産設備を設計,管理することである。各工程,機械,設備への汚染異物の侵入を最小化し,侵入又は発生した異物を迅速に除去できる設計であることが,部品や機械の損傷を最小にする。その結果,大きなコスト削減が達成できる。
潤滑不要の主要因が汚染異物であることから,清浄度管理は予防保全である。図1に示すように,予防保全が最も総コスト比の低い保全手法である。この予防保全手法である流体の清浄度管理では,高性能なフィルターを設置するだけでは十分ではない。機械や設備が故障しない清浄度管理基準を常に満足していることを検証するために,清浄度をモニターすることも必要である。
2. 清浄度モニターの考え方
上述のように,コスト削減には設備を最適な状態で運転しなければならない。そのためには,設備の状態を連続的にモニターする必要がある。その結果,清浄度のわずかな上昇も検出でき,即座に是正処置が施せるため,摩耗量を最小限に止めることができる。
このような連続的な清浄度モニターの必要性については,基本的な摩耗発生プロセスを理解することが重要である(図2)。設備や機械に適切なフィルターが搭載され,維持されており,潤滑条件が仕様の範囲内で,あらかじめ定められた条件で運転されている場合,摩耗粉は摺動面材料の疲労によって発生する10μm以下の非常に小さな粒子である。これらの摩耗粉は摺動面の材料に繰り返し作用する応力によって,材料表面が疲労破壊し微細な粒子を放出する。これは,非常に穏やかな摩耗形態であり,摩耗粉は設備や機械のすき間に引っかかることなく通過してしまい,摩耗の発生は最小限である。
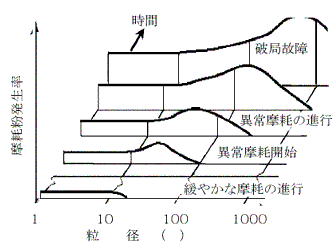
図2 破局故障への摩耗発生率
適切なフィルターが設置されていない場合,使用中に性能が劣化するフィルターを使用している場合,あるいは潤滑性が悪化する場合,摩耗粉の発生量とフィルターによって除去される汚染粒子の量のバランスが崩れ,摩耗率が上昇する。摩耗率の上昇を検出し是正しなければ,摩耗粉発生の連鎖が起こり,摩耗粉の粒径および粒子数ともに急激に増加する。その結果,摩耗形態は緩やかな疲労摩耗からアブレシブ摩耗へと変化する。アブレシブ摩耗では摺動部表面は急激に削り取られてしまう。
ここで提案している手法は,汚染異物の増加を検出し,是正処置を施し,正常な状態に戻すことである。これによって機器への恒久的な損傷を最小限に止めるだけでなく寿命も延長できる。そのため,清浄度のモニターとその技術は,14μm(c)以下の微細な粒子を正確にしかも再現性良く検出でき,さらに短時間で結果を示せるようなものでなくてはならない。
3. 試料採取と分析方法
(1)清浄度モニターなくして清浄度管理なし
図2で示す「緩やかな摩耗の進行」の領域に留めるためには,適切なフィルターを設置することに加えて,管理状態を検証するために清浄度をモニターすることが必要である。たとえ信頼性の高い性能のフィルターによってシステムが保護されていたとしても,部品の経年変化,運転条件の変化,予期せぬ使用条件の変化などによって摩耗率は変化する。また,外部環境からの異物の侵入などによる清浄度の悪化も見逃せない。システムのわずかな変化も見逃さずに,高い信頼性を維持してシステムを運転するためには,常に清浄度をモニターすることが要求される。
(2)モニターによる分析法
採取および分析方法には,図3のように3種類の方法がある。第一,第二の方法は,システムから試料油を直接モニターに取り込むと同時にその場で分析するオンラインおよびインラインモニター法,第三の方法は,システムから一度容器に流体を採取し,分析室や外部分析機関で分析を行うオフラインモニター法である。第一,第二の方法と第三の方法では,分析結果の信頼性に大きな相違がある。
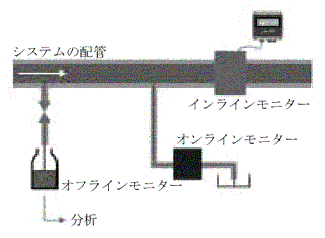
図3 サンプリング法
1. オンラインモニター法
オンラインモニター法は,システム運転中に試料を採取すると同時に分析する方法である。あらかじめシステムに設けた採取口にモニターを接続し,わずかの分析用の流体をシステムから分岐してモニターに導く。モニターから排出された分析終了後の流体はタンクへ戻す。モニターを永久にシステムに接続することも,必要な時に取り付けて清浄度をモニターすることも可能である。この手法の効果としては,連続した分析が可能なこと,わずかの変化も検出できること,採取および分析に伴う廃液が発生しないことである。
2. インラインモニター法
インラインモニター法は,システムのライン中にモニターを永久に設置し,システムを流れる流体の清浄度を直接モニターする方法である。後述するオフラインモニター法の場合,採取時に採取ラインのフラッシングが必要だが,インラインモニターの場合,流体は常に流れているためフラッシングの心配はない。また常にラインに設置されているために,清浄度をモニターする手間が省ける。圧力計で圧力を読む感覚で清浄度を知ることができる。
3. オフラインモニター法
オフラインモニター法では,システムから分析用の試料液を試料瓶または容器に採取し,分析室または外部分析機関で分析を行う方法である。採取量が限られていること,採取から分析までの過程で試料液への汚染が発生し,大きな誤差原因となる。試料液の汚染による誤差要因としては,上述のように廃液量を節約するためにフラッシングが十分できないこと,試料瓶や容器を異物フリーにすることが不可能なこと,採取場所の雰囲気からの汚染が避けられないこと,さらには分析装置での測定時にも異物フリーできないことなどにより測定結果の信頼性に限界がある。たとえISO4021などによって定められた採取方法に従ったとしても,誤差を最小限に止めることは可能だが,防止することはできない。特に現代のシステムの清浄度は大幅に改善されているために,誤差の影響はますます大きくなっている。
図4は採取方法による誤差の大きさを調査した結果である。総数133のシステムにおいて,オフラインモニター法とオンラインモニター法の調査結果である。ISO4406による清浄度コードが17より清浄な流体の場合,ISO清浄度コードで1を超える差が生じている。例えば,オンラインモニターでISO清浄度コードが11の流体を試料瓶に採取するオフラインモニターの場合,15またはそれ以上となる。NAS等級で表すと,NAS3級の流体のはずが,NAS7級よりも汚れたものと評価されてしまう。多くの場合,忠実にISO4021に従い試料を採取することは少ないため,採取時に汚染され,NAS3級の流体はNAS7級ではなく,NAS8級にも9級にもなってしまう。
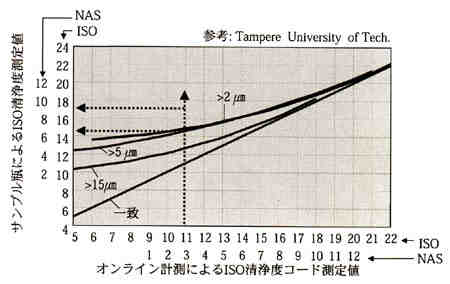
図4 サンプル瓶使用による分析誤差
さらに,オフラインモニター法では,清浄な試料瓶の準備,採取に伴う種々の作業,外部分析機関へ送る場合,試料瓶の梱包・発送などの作業が必要である。また分析結果も2~4週間後であり,システムのわずかな変化を検出し,迅速に是正処置を施すには適さない。
4. モニター結果の活用
システムの信頼性が低い場合,メンテナンスコストが増加するだけでなく,製品の歩留まり,製品品質,納期など数々の問題を引き起こし,単なるシステムの故障だけにはとどまらない。このような状態を避けるために,清浄度を正しく,しかも,定期的または連続的にモニターすることによって,故障が進行する前に異常を検出し,問題点を迅速に解決することが可能となる。
図5はシステムまたは個々の機器の性能劣化パターンを示す。正常な状態であれば,システムは100%の性能の状態で運転されている。異常摩耗や運転時間の経過などによって性能が悪化し始め,性能劣化が検出できるレベルになると,AE(アクースティック・エミッション)や振動などの測定器により異常を検出できる。さらには,機能限界を超えると寿命または故障となる。清浄度が原因で性能が悪化する場合を考えてみよう。現象としては,清浄度の悪化が始まり,摩耗の連鎖が始まり,その結果システムの性能劣化や機能不全が起こる。清浄度をモニターしていない場合,摩耗が進み性能劣化で初めて異常に気が付く。清浄度の変化を常にモニターすることによって,摩耗の連鎖に進む前に適切な是正処置を施すことができ,システムの性能劣化を未然に防止することができる。
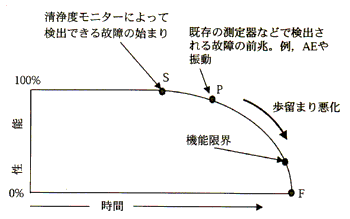
図5 清浄度モニターによって検出できる故障の始まり
おわりに
油圧や潤滑システムの故障率を低減する手法の一つとして清浄度モニターが重要な役割を果たす。システムにおける清浄度の変化は故障の前兆である。適切な方法でシステムの清浄度をモニターできれば,重大な損傷に発展する前に根本原因を調査できる。また,モニター結果の記録を分析することによって予防保全が可能になる。すなわち予防保全手法によりメンテナンスコストの削減,すなわち利益創出に貢献できる。